【実践向け】A5056フライス加工のための最適ツール選択ガイド
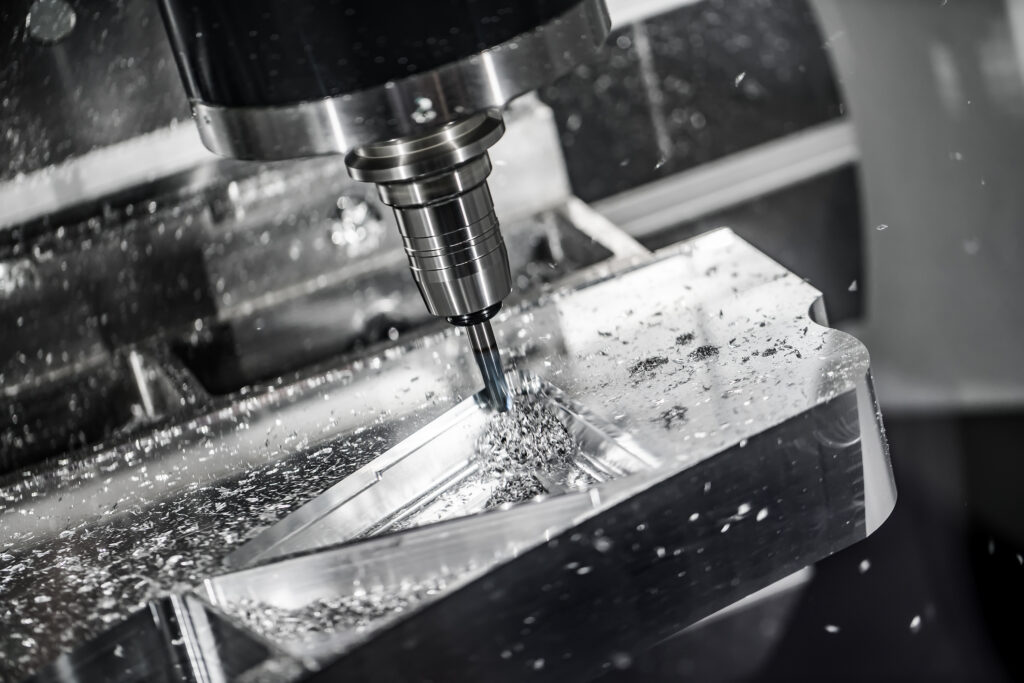
フライス加工を行う際に、最適なツールを選択することは非常に重要です。特にA5056という材料に焦点を当てると、適切なツール選びはますます重要になります。本ガイドでは、A5056フライス加工における最適なツール選択について解説します。A5056の特性やフライス加工のポイントについて理解し、効果的なツールを選ぶための具体的な方法を紹介します。さまざまな状況に対応できるツール選択のコツや実践的なアドバイスを掲載しています。フライス加工におけるツール選択の重要性を理解し、A5056材料を用いた加工において最適な結果を得るために、ぜひ本ガイドをご活用ください。
1. A5056フライス加工の基礎知識
A5056フライス加工では、適切な工具選びが非常に重要です。この合金は、その耐食性と加工性のバランスが評価され、多くの産業で使用されています。ただし、適さない工具を使用すると、加工品質が低下したり、工具の寿命に影響を与える可能性があります。具体的な例としては、A5056合金の場合、高速度鋼よりも超硬合金の方が良好な結果をもたらすことが多いです。超硬合金は硬度が非常に高く、耐摩耗性に優れているため、A5056合金の加工に適しています。また、チップの形状やコーティングの種類によっても加工効率や仕上がりが変わってきます。最適なツール選択を行えば、効率的で高品質なフライス加工が可能となります。結論として、A5056のフライス加工は正しい工具の選定から始まり、これにより加工の効率化および品質の向上が期待できるということです。
2. A5056フライス加工におけるCNCの役割
A5056フライス加工で最適なツールを選択することは、加工効率の向上とコスト削減に直結します。A5056材は、その優れた強度と耐食性から多くの工業分野で使用されていますが、適切なツールを選ぶことでその特性を最大限に活かすことができるのです。例えば、硬質合金製のエンドミルは、A5056のような非鉄金属加工において高い切削性能を発揮し、長寿命を実現するために推奨されます。また、切削速度や送り速度、切りくずの排出方法などの加工条件も、ツールの選択に大きく影響します。最適なツール選択により、A5056材のフライス加工はより精度高く、効率的に行えるようになります。このように、適切なツールと加工条件の見極めが、高品質な製品をコスト効率よく生産する鍵となるのです。
3. 切削加工とA5056フライス加工の違い
切削加工とA5056フライス加工は異なる特性を持っています。通常の切削加工が多種多様な金属に適用されるのに対し、A5056フライス加工はアルミニウム合金の一種であるA5056材専用の加工方法です。このA5056材は軽量でありながら高い強度を持っているため、航空機や自動車の部品によく使用されます。最適なツール選択では、この材料の特性に合わせた刃物材質や形状を選ぶことが重要です。具体的には、切削抵抗が小さく、耐熱性に優れた刃物が推奨されます。また、A5056材の高い延性を考慮して、精度の高い加工が可能な工具を選ぶべきです。このように適切な工具を選ぶことで、A5056フライス加工はより効率的かつ精密に行えるため、その選択は製造の質とコストに直結するという結論に至ります。
4. A5056フライス加工のための設計ガイドライン
A5056フライス加工に最適なツールを選択することは、加工の品質と効率を大きく左右します。A5056合金は軽量かつ耐食性に優れているため、航空宇宙産業や自動車部品の加工に広く利用されています。適切なツールを選ぶ際には、A5056の物性を考慮する必要があります。たとえば、硬質のカッターやコーティングが施されたエンドミルは、この合金の加工に適しています。また、高速で精度良く加工を行うためには、切削抵抗が小さく、熱伝導率の高いツールが推奨されます。具体例としては、ダイヤモンドライクカーボン(DLC)コーティングを施したエンドミルがA5056加工で好結果をもたらすことが報告されています。このようなツールの選択により、製品の精度を高めると同時に、工具の寿命を延ばし、コスト削減にも繋がります。結論として、A5056フライス加工には、材質やコーティングに特化したツールを選ぶことが、加工の成功への鍵となるでしょう。
5. A5056フライス加工の最適ツール選択
A5056フライス加工における最適なツール選択は、加工品質向上とコスト削減の両方を達成するために重要です。A5056はアルミ合金の一種で、その特性を考慮したツールが必要とされます。例えば、高速度鋼(HSS)製のエンドミルや、アルミニウム削りに特化した超硬ツールが適しています。これらはA5056の柔らかい材質に対応し、精度の高い加工を可能にします。さらに、切削抵抗が小さく、耐摩耗性に優れたダイヤモンドコーティングツールは、長寿命でコストパフォーマンスに優れています。最後に、ツールの選択に際しては、切削条件や機械の仕様と相談し、トライアル加工などで最適なものを見極めることが重要です。結局のところ、ツール選択はA5056フライス加工の成功に直結しており、適切な選択が高品質な製品を安定して生産する鍵となります。
6. A5056フライス加工における部品の欠陥と対策
A5056フライス加工に使用する最適なツール選択は、製造業にとって重要な判断です。A5056材は軽量かつ耐食性に優れており、そのため航空機や自動車産業で広く使用されています。しかし、適切でない工具を使用すると、加工面に傷がついたり精度が低下することがあります。たとえば、硬質合金製のエンドミルはA5056の加工に適しており、その切れ味と耐久性から部品の精密性を高めることができます。一方で、切削速度や送り速度、カッターの直径などが部品の仕上がりに大きく影響するため、これらのパラメータも慎重に選定する必要があります。最終的に、最適な工具とパラメータの選定により、A5056フライス加工時の部品の欠陥を最小限に抑え、製造効率と製品品質の向上に寄与します。
7. A5056フライス加工の精度向上テクニック
A5056フライス加工の精度を向上させるためには、最適な工具の選択が重要です。このアルミニウム合金は、その優れた強度と軽量性から、航空機や自動車の部品などに幅広く使用されています。しかし、その加工には専門の知識と適切なツールが必要です。例えば、超硬エンドミルやダイヤモンドコーティングの工具は、A5056のような非鉄金属の加工に適しており、精度の高い仕上がりを実現します。加工速度や送り速度の調整も精度に影響を与えるため、ツールや材料に応じて最適な条件を見つけることが大切です。正しい工具と加工条件の選択によって、A5056フライス加工の品質は大きく向上し、経済的な生産が可能になります。したがって、工具と条件の選定には十分な検討が求められるのです。
8. A5056フライス加工の活用事例と応用
A5056フライス加工では、最適なツールの選択が非常に重要です。なぜなら、適切なツールを選ぶことで加工精度が向上し、製品の品質が保たれるからです。特に、航空機や自動車の部品製造に使われるA5056合金は、その耐食性と軽量性から高い耐久性が求められます。例えば、航空機の燃料タンクや自動車のフレーム部分に使用されることが多いため、加工には精密さが要求されます。そのため、硬質合金やダイヤモンドコーティングされたエンドミルなど、材質に合わせた特化したツールが推奨されています。適切なツールを使用することで、耐久性と効率の両立が可能となり、コスト削減にも繋がります。結論として、A5056フライス加工においては、用途と材質に応じたツール選択が成功の鍵となるのです。
9. A5056フライス加工のトラブルシューティング
A5056フライス加工において最適なツールを選択することは、加工品質の向上と生産効率の高さに直結します。A5056材は、その優れた耐食性や加工性により幅広い産業で使用されていますが、適切なツールを用いなければ、加工時の問題が発生することがあります。例えば、硬質のツールを使用した場合、材料の熱伝導率が高いため、切削時に発生する熱が逃げにくく、ツールの耐久性に影響を及ぼすリスクがあります。そこで推奨されるのは、切削抵抗が低く熱伝導性に優れたツールを選ぶこと。具体的には、ダイヤモンドコートされたエンドミルや、高い放熱性を持つ超硬エンドミルが効果的です。これらのツールを選択することで、A5056のフライス加工におけるトラブルを防ぎながら、精度の高い加工を実現できるのです。結論として、材料の特性を理解し、それに合ったツールを選ぶことが、最適なフライス加工を行うための鍵となるでしょう。
10. A5056フライス加工の将来展望と技術進化
A5056フライス加工における適切なツール選択は、効率的で高品質な製品を生産する上で重要です。この合金は軽量でありながら高い強度を持っているため、航空機や自動車産業での需要が高まっています。最適なツールを選ぶ際には、切削抵抗が低く、耐久性に優れたものを選ぶことが肝心です。例えば、超硬質のエンドミルやチタンコーティングされたドリルは、A5056の加工に適しており、精密な加工を実現させます。さらに、適切な潤滑剤の使用は、切削面の仕上がりを向上させ、工具の寿命を延ばす効果があります。最終的に、正しいツールと加工条件の選択によって、A5056フライス加工はより効果的かつ経済的に行えるようになるでしょう。
まとめ
A5056のフライス加工において、最適なツール選択にはいくつかのポイントがあります。材料の特性や加工する形状によって適したツールは異なるため、十分な検討が必要です。また、適切な切削条件を設定し、十分な冷却を行うことも重要です。これらのポイントに気を配りながら、効率的で精密な加工を目指しましょう。