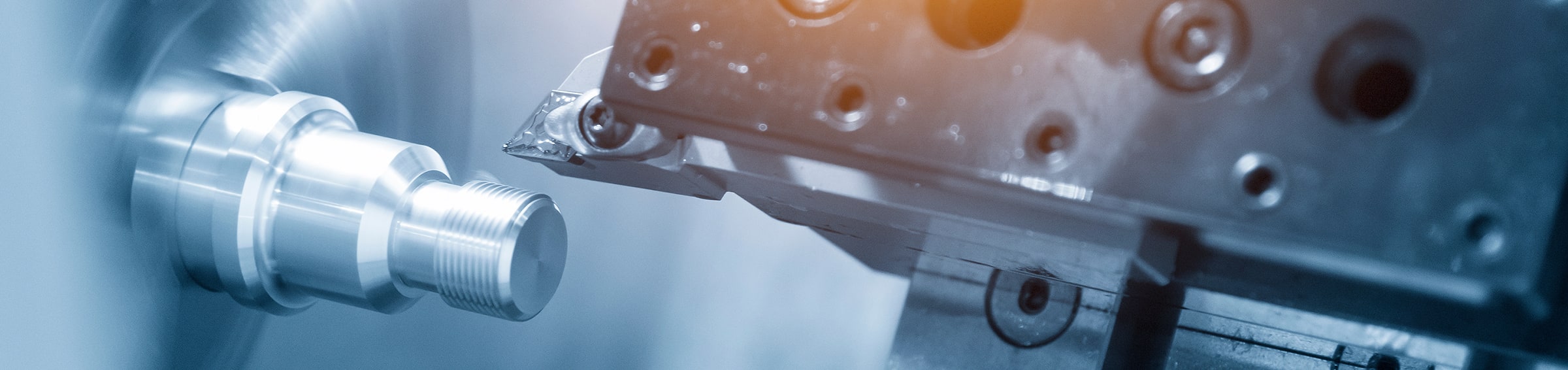
加工技術 column
フライス盤活用ガイド:そのメリットとデメリットを徹底解説
フライス盤という言葉を聞いたことはありますか?ホビーから産業用途まで多岐にわたるこの機械は、様々な分野で活躍しています。本記事では、フライス盤の利点と欠点について徹底的に解説していきます。工作や加工に興味がある方、または製造業界で活躍する方々にとって、この情報はきっと役立つはずです。フライス盤を活用する上でのポイントや注意点を知りたい方は、ぜひご覧ください。
1. フライス盤の基礎知識
1-1. フライス盤とは
フライス盤を活用することは、多くの製造業で広く行われています。これには明確な理由がありますが、利点とともに欠点も存在します。まず、フライス盤の最大のメリットはその汎用性にあります。様々な形状を加工できるため、複雑な部品や独特のデザインの製品も容易に作成可能です。例えば、自動車の部品や精密機械の部品加工において、フライス盤は不可欠です。さらに、精度の高い加工が可能であり、製品の品質を大きく向上させることができます。
しかしながら、デメリットも存在します。フライス盤の運用には高度な技術が必要であり、操作する技能者には長期の訓練が必要です。また、設備そのものの初期投資費用も高額であり、中小企業にとっては大きな負担となることもあります。
結論として、フライス盤の利用はその汎用性と高精度な加工能力によって、多くの製造業で重宝されています。しかし、運用には専門の知識と技術、そして初期投資が必要となります。そのため、フライス盤を導入する際には、これらのメリットとデメリットを十分に理解し、企業のニーズに合った選択をすることが重要です。
1-2. フライス盤の歴史と進化
フライス盤は製造業で広く使われている機械の一つであり、多様な加工を可能にするそのメリットは計り知れません。しかし、使い方を誤るとデメリットも存在します。この機械のメリットとしては、高い精度で複雑な形状を加工できる点が挙げられます。例えば、航空宇宙産業や自動車産業では、フライス盤を用いて精密な部品を製造しています。また、多様な素材を加工できる汎用性もメリットとして大きいです。
一方で、フライス盤のデメリットとしては、操作に高い技術が必要となり、熟練した操作者が不足している点があります。また、大きな機械のため、設置には十分なスペースが必要となります。さらに、高価であるため、初期投資が大きくなることも考慮しなければなりません。
結論として、フライス盤は製造業における多様な加工ニーズに応える非常に有効な機械です。その高い加工精度と汎用性は、多くの産業での利用を可能にしています。しかし、操作には熟練が必要であり、設置スペースやコストも考慮する必要があります。フライス盤を導入する際は、これらのメリットとデメリットをしっかりと理解し、効果的に活用することが重要です。
1-3. フライス盤の種類とその用途
フライス盤は工業製品の加工に不可欠な機械として、多くのメリットを提供しますが、一方でデメリットも存在します。この機械が提供する最大のメリットは、その高い精度と複雑な形状の加工能力です。例えば、自動車のエンジン部品や航空機の部品など、精密な加工が必要な製品の製造に欠かせません。しかし、フライス盤を使用するには高度な技術と経験が必要であり、初期投資も大きいというデメリットがあります。また、操作が複雑であるため、熟練した操作者が不足していることも問題の一つです。さらに、大型のフライス盤は場所を多く取るため、小規模な工場では導入が難しい場合があります。これらのメリットとデメリットを踏まえ、フライス盤の導入を検討する際には、製品の種類、加工する材料の性質、工場のスペース、技術者の技量など、多角的な観点から総合的な判断が求められます。フライス盤はその高い加工能力により多くのメリットを提供しますが、デメリットも理解した上で適切に活用することが重要です。
1-4. フライス盤の基本的な構造と機能
フライス盤は、金属やプラスチックなどの材料を加工するための重要な工作機械です。この機械の活用は、製造業において大きなメリットをもたらしますが、一方で注意すべきデメリットも存在します。まず、フライス盤の最大のメリットは、複雑な形状や精密な部品を高い精度で加工できる点にあります。例えば、航空宇宙産業や自動車産業で要求される精密な部品製造には、この機械が不可欠です。また、CNC(コンピュータ数値制御)技術を用いたフライス盤では、プログラミングによって自動で加工が行えるため、作業の効率化が図れます。
しかし、これらのメリットがある一方で、フライス盤を扱うには高度な技術と経験が必要であり、操作ミスが大きな損害に繋がる可能性がある点がデメリットです。さらに、高価な設備投資が必要であるため、中小企業にとって導入のハードルが高い場合もあります。
結論として、フライス盤を活用することで、精密な加工が可能になり生産効率を大きく向上させることができます。しかし、運用には専門的な知識と技術が求められ、初期投資も無視できません。このため、フライス盤の導入を検討する際には、これらのメリットとデメリットを十分に理解し、自社のニーズに合った最適な利用方法を見極めることが重要です。
1-5. フライス盤の操作方法の概要
フライス盤を活用することは、多くの製造業での生産性向上に不可欠であり、そのメリットとデメリットを理解することは重要です。フライス盤の利点は多岐にわたりますが、特に精密な加工が可能である点が挙げられます。複雑な形状や細かい部品も、高い精度で製造することが可能です。例えば、自動車のエンジン部品や航空機のコンポーネントなど、精密さが求められる分野で広く利用されています。
しかし、デメリットも存在します。その一つが、高い導入コストです。特に、高性能な機械への投資は初期費用が高くつきます。また、操作や保守には専門的な知識が必要であり、技術者の育成にも時間がかかることが挙げられます。
結論として、フライス盤の活用は、製造業における競争力を高める上で非常に有効です。その精密な加工能力により、高品質な製品の提供が可能になります。一方で、高い初期投資と技術者の確保は、導入の際の大きな課題です。このように、フライス盤のメリットとデメリットを踏まえた上で、導入を検討することが重要です。
2. フライス盤のメリット・デメリットは?
2-1. フライス盤のメリット
フライス盤は、精密な金属加工に欠かせない重要な機械です。その最大のメリットは、高い加工精度と柔軟性にあります。フライス盤を使用することで、複雑な形状や細部まで精密に加工することが可能となり、多様な製品製造に応用できます。例えば、自動車のエンジン部品や航空機のコンポーネントなど、精密な加工が求められる分野で広く利用されています。また、フライス盤は、様々な種類の素材に対応できるため、使用範囲が広いことも大きな利点です。
しかし、デメリットも存在します。フライス盤は、その高い精密性と柔軟性を生かすためには、操作する技術者の高度なスキルが必要です。加えて、初期投資コストが高いことも挙げられます。高品質なフライス盤の導入には、相応の資金が必要になるため、中小企業やスタートアップにとっては、投資のハードルが高くなりがちです。
結論として、フライス盤はその高精度な加工能力と柔軟性から、多くの製造業で不可欠な機械です。しかし、高度な操作技術と初期投資の必要性というデメリットも理解した上で、導入を検討することが重要です。このバランスを考慮することで、フライス盤の活用はさらに効果的となるでしょう。
2-2. フライス盤のデメリット
フライス盤を利用する際のデメリットを理解することは、その活用方法を最大限に引き出す上で不可欠です。まず、フライス盤の大きな欠点の一つは、その高い初期費用です。購入費用だけでなく、メンテナンスや操作研修にも費用がかかります。また、操作には専門知識が必要であり、熟練した操作者が不足している場合、機械の能力を十分に活用することが難しいことがあります。例えば、複雑な形状の加工を行う場合、高度な技術が必要とされ、その習得には時間とコストがかかります。しかし、これらのデメリットを克服することで、フライス盤は精密な加工を実現し、製造業の効率化に貢献します。結論として、フライス盤のデメリットは存在しますが、これらを適切に管理し、対策を講じることで、その高いポテンシャルを最大限に活かすことができます。
3. フライス加工の特徴とメリット
3-1. フライス加工の基本的な特徴
フライス盤は、精密な加工が可能で多様な形状を削り出せるため、製造業で広く利用されています。そのメリットとして、高い精度で複雑な形状の加工が可能であり、大量生産にも対応できる点が挙げられます。例えば、自動車のエンジン部品や航空機の部品製造において、フライス盤の精度と効率性が求められます。しかし、デメリットとしては、操作に高度な技術が必要であり、設備投資の初期費用が高いことがあります。特に、最先端のフライス盤を導入する場合、そのコストはさらに高くなります。また、複雑な形状の加工には時間もかかるため、短納期の案件には向かない場合があります。結論として、フライス盤はその高い精度と多様性により多くの利点を提供しますが、操作の難易度やコストの面での考慮も必要です。適切に活用すれば、製造業の生産性と品質の向上に大きく貢献することが期待できます。
3-2. フライス加工の応用分野
フライス盤を活用することは、多くの製造業での生産性向上に繋がりますが、そのメリットとデメリットを理解することが重要です。フライス盤の最大のメリットは、高精度で複雑な形状の加工が可能であることです。例えば、航空宇宙産業や自動車産業では、非常に複雑な部品もフライス盤を使用して精密に加工することができます。これにより、製品の品質を大幅に向上させることが可能です。
しかし、デメリットとしては、フライス盤自体やその保守に高額な費用が掛かることが挙げられます。また、操作には専門的な技術や知識が必要となり、熟練したオペレーターが不可欠です。特に日本のような労働人口が減少している国では、高度な技術を持つ人材を確保することがさらなる課題となっています。
結論として、フライス盤の活用は製造業における生産性の向上には欠かせないものですが、高い初期投資や専門人材の必要性などのデメリットも理解し、対策を講じることが重要です。適切に管理し、活用すれば、フライス盤は製品の品質向上や生産効率の向上に大きく貢献できるでしょう。
3-3. フライス加工における精度と仕上がり
フライス盤を活用することには多くのメリットがあり、同時にいくつかのデメリットも存在します。まず、フライス盤の最大のメリットは、その高い精度と美しい仕上がりにあります。この機械を使うことで、複雑な形状や細かい部品も正確に加工することが可能になります。たとえば、自動車のエンジン部品や航空機の部品製造では、極めて高い精度が求められるため、フライス盤が頻繁に使用されます。
しかし、デメリットも無視できません。フライス盤は高価であり、操作には専門の知識と技術が要求されます。また、大きな機械のため、設置には十分なスペースが必要となります。これらの側面は、特に小規模な製造業者にとっては大きなハードルとなることがあります。
結論として、フライス盤を活用することは、その精度と仕上がりにおいて大きなメリットを提供しますが、初期投資や運用には注意が必要です。適切な知識と技術があれば、この機械は製造工程における強力なツールとなり得ます。
3-4. 小ロット生産におけるフライス加工の役割
フライス盤は多様な加工が可能で、特に小ロット生産においてその利点が顕著です。フライス盤の活用は、生産の柔軟性を高め、短期間で多種多様な製品の製造を可能にします。その主なメリットは、加工の精度が高く、複雑な形状でも対応できる点です。例えば、機械部品や精密機器のプロトタイピングにおいて、フライス盤は不可欠な役割を果たします。しかし、デメリットとしては、設備投資が大きくなりがちで、操作には専門技術が必要となる点が挙げられます。特に、高度な形状を加工する場合、その設定には時間とコストがかかることがあります。
結論として、フライス盤は小ロット生産において非常に有効なツールであり、その高い加工精度と柔軟性は多くのメリットを提供します。しかし、その導入と運用にはコストと専門知識が必要となるため、利用を検討する際には慎重に評価する必要があります。
4. NC工作機械導入のメリット・デメリット
4-1. NC工作機械とは
フライス盤は、金属や木材などの材料を加工するための重要な工作機械です。フライス盤を活用することで、精密な加工が可能になり、製品の品質向上につながります。しかし、フライス盤にはメリットとデメリットの両方が存在します。
フライス盤の最大のメリットは、その高い精度と柔軟性です。複雑な形状や微細な加工が必要な場合でも、フライス盤を使用すれば精密な作業を実現できます。例えば、自動車の部品製造や航空宇宙関連の部品加工において、フライス盤は欠かせない存在です。これらの分野では、極めて高い精度が求められるため、フライス盤の能力が大いに活かされます。
一方で、フライス盤のデメリットとしては、高い導入費用や運用に伴うコストが挙げられます。フライス盤自体の価格だけでなく、運用するためには専門の技術者が必要となり、維持管理費もかかります。また、大型のフライス盤を設置するためには、十分なスペースも必要です。
結論として、フライス盤は高い精度と柔軟性を実現する非常に有効な工作機械ですが、導入および運用にはコストがかかるというデメリットが存在します。それでも、必要な精度と加工能力を考慮した場合、フライス盤は多くの製造現場で重要な役割を果たしています。
4-2. NC工作機械の機能と利点
フライス盤は、精密な部品加工に不可欠な工作機械であり、その利便性により幅広い産業で利用されています。しかし、利点と共にいくつかのデメリットも存在します。この文章では、フライス盤のメリットとデメリットを詳しく見ていきましょう。
フライス盤の最大の利点は、その高い精度と柔軟性です。複雑な形状や細部まで精密に加工できるため、自動車や航空機の部品製造など、厳密な寸法精度が求められる領域で重宝されています。例えば、エンジン部品の加工では、フライス盤を使用することで、微細な加工が可能になり、製品の品質向上に寄与しています。
一方で、フライス盤にはいくつかのデメリットも存在します。特に、高いコストが挙げられます。フライス盤自体の価格だけでなく、維持管理や操作に高度な技術が必要なため、導入初期には大きな投資が必要になることがあります。また、複雑なプログラミングや設定が必要な場合が多く、操作に習熟するまでに時間がかかることも、デメリットとして考えられます。
まとめると、フライス盤はその精密さと柔軟性により多くの産業で重宝されていますが、高いコストや習熟に時間がかかるというデメリットも理解しておく必要があります。利点を最大限に活かしつつ、デメリットを適切に管理することが、フライス盤を効果的に活用する鍵となります。
4-3. NC工作機械の限界と課題
フライス盤を活用することには、多くのメリットがありますが、同時にデメリットも存在します。フライス盤は、精密な加工が可能で多様な材料に対応できるため、製造業や工作業界で広く使用されています。特に、日本の製造業では高い精度と効率を求められるため、フライス盤の利用は欠かせません。
メリットとしては、まずその精度の高さが挙げられます。フライス盤は、複雑な形状や細かいパーツの加工にも対応できるため、多様な製品の製造が可能です。また、CNCフライス盤を使用することで、プログラムによる自動操作が可能となり、大量生産においても一貫した品質を維持できる点も大きなメリットです。
デメリットとしては、高度な技術が必要となる点が挙げられます。操作には専門的な知識と経験が必要であり、熟練した技術者の育成には時間とコストがかかります。また、初期投資として高額な設備投資が必要となることも、導入の障壁となり得ます。
総じて、フライス盤の活用は、精密加工が求められる製造業において大きなメリットをもたらしますが、その導入と運用には、技術者の育成や設備投資といった検討すべきポイントも存在します。適切な導入計画と運用管理が、フライス盤を最大限に活用するための鍵となるでしょう。
4-4. NC工作機械と従来機械の比較
フライス盤を活用することは、製造業での生産性向上において非常に有効な手段です。フライス盤のメリットは多岐にわたりますが、デメリットも存在します。まず、フライス盤の最大のメリットは、複雑な形状の加工が可能であり、精密な部品製造に欠かせないことです。例えば、航空宇宙産業や自動車産業で使用される部品の製造において、フライス盤はその精度と柔軟性によって重宝されています。また、CNCフライス盤を使用すれば、プログラミングによる自動化が可能となり、大量生産においても一貫した品質を保つことができます。
しかし、フライス盤のデメリットとしては、高い初期投資が必要になる点が挙げられます。特に、先端技術を取り入れたCNCフライス盤は、その価格が高額になる傾向にあり、中小企業にとっては導入が難しいケースもあります。また、操作やプログラミングには専門的な知識が求められるため、技術者の育成にも時間とコストがかかります。
結論として、フライス盤の活用は製造業における生産性の向上に寄与しますが、高い初期投資や専門知識の必要性というデメリットも理解した上で、その導入を検討する必要があります。効率的な生産とコスト削減のバランスを考えながら、フライス盤の利用を最大化することが、産業の発展につながるでしょう。
5. 切削加工のメリットとデメリット
5-1. 切削加工の基本
フライス盤は、金属やプラスチックなどの材料を削り出して形を整えるために使われる機械です。その最大のメリットは、高度に複雑な形状でも、精密で均一な加工が可能であることです。例えば、自動車や航空機の部品製造においては、フライス盤による加工が不可欠です。これにより、製品の品質と機能性が保証されます。
しかし、フライス盤を用いるには高い技術が必要とされ、操作に熟練した技術者が不可欠です。加えて、機械自体の初期投資も高額であるため、中小企業やスタートアップにとっては負担となることもあります。また、複雑な形状を加工する際には、設計段階での細かな配慮も求められます。
これらの点を踏まえると、フライス盤は高い精度と効率性を誇る一方で、導入と運用にはコストと技術的なハードルが存在します。しかし、それらを克服することができれば、幅広い産業での製品品質の向上に寄与する重要な機械と言えるでしょう。
5-2. 切削加工の効率とコスト
フライス盤は、金属やプラスチックなどの材料を切削して形を整えるために用いられる工作機械です。これの利用には多くのメリットがありますが、同時にデメリットも存在します。フライス盤の最大のメリットは、複雑な形状や精密な部品を効率的に大量生産できる点にあります。例えば、自動車業界や航空宇宙産業では、フライス盤を使ってエンジン部品やフレーム部品などを製造しています。これにより、製造コストの削減と生産性の向上が可能になります。
しかし、フライス盤を利用する上でのデメリットも無視できません。その一つが、高額な初期投資が必要となる点です。質の高いフライス盤は価格が高く、また、操作技術を習得するための教育やトレーニングにも時間とコストがかかります。また、フライス加工は騒音や振動が大きいため、作業環境にも十分な配慮が必要です。
結論として、フライス盤は製造現場での多様な要求に応える柔軟性と効率性を提供します。しかし、その導入には高い初期投資や運用のデメリットも認識しておく必要があります。適切な導入計画と技術習得を通じて、フライス盤のメリットを最大限に活用することが重要です。
5-3. 切削加工の品質と制約
フライス盤は、金属加工で不可欠な機械です。その使用は高い精度と効率を実現しますが、一方で特定のデメリットも存在します。フライス盤の最大のメリットは、複雑な形状や平面、溝など、多様な加工が一台で可能な点です。たとえば、自動車のエンジン部品や航空機の部品製造において、精密な加工が求められる場合、フライス盤はその要求を満たします。また、CNC(コンピュータ数値制御)フライス盤を使用すれば、プログラムに従って自動で加工が行われるため、作業者の技術依存度を下げ、一貫した品質を保つことができます。
しかし、フライス盤には投資コストが高いというデメリットがあります。特に最先端のCNCフライス盤は、高価であり初期投資が重くのしかかります。また、機械の操作やメンテナンスには専門知識が必要であり、適切な訓練を受けた人材を確保する必要があります。これらのデメリットにより、特に小規模な製造業者にとっては、導入が難しい場合があります。
結論として、フライス盤はその高い加工能力と効率性により、多くの製造業で重宝されています。しかし、高額な投資コストや専門知識の必要性といったデメリットも認識し、採用を検討する際はそれらを十分に考慮する必要があります。適切に活用すれば、フライス盤は製造業の生産性を大きく向上させることができるでしょう。
5-4. 切削加工の安全性と環境への影響
フライス盤を利用することは、様々な製造業において不可欠であり、そのメリットは多岐にわたります。しかし、デメリットも存在するため、これらを理解した上で活用することが重要です。
フライス盤の最大のメリットは、精密な加工が可能である点です。多様な刃を使い分けることで、複雑な形状や細かい加工も精度高く仕上げられます。例えば、機械部品や工具など、高い精度が求められる製品の加工には欠かせません。
しかし、デメリットとしては、操作には専門的な知識と技術が必要となることが挙げられます。設定ミスや操作ミスは大きな事故につながる可能性があり、安全対策と熟練した操作技術が求められます。また、初期投資が高額であることも、利用を検討する上での障壁となり得ます。
これらのメリットとデメリットを考慮した上でフライス盤を活用することは、製造業の生産性向上に大きく貢献します。精密な加工が可能である点を活かし、専門的な知識と技術を身に付け、安全対策を徹底することが、効果的なフライス盤の活用には欠かせません。
6. フライス加工と旋削加工の違いや注意点
6-1. フライス加工と旋削加工の基本的な違い
フライス盤を活用することには、多くのメリットと一部のデメリットが存在します。最初に、そのメリットについて触れましょう。フライス盤は、複雑な形状や精密な部品を効率的に加工することができます。例えば、溝や歯車などの加工に適しており、多様な材料に対応することができる点も大きな利点です。さらに、CNC(コンピュータ数値制御)技術と組み合わせることで、高精度で複雑な形状の加工が可能になり、作業者の技術依存度を下げることも可能です。
しかし、デメリットも無視できません。フライス盤の導入や運用には、高額な初期投資が必要となります。また、操作や設定には高度な技術が求められ、熟練した技術者が不足している場合、その活用は難しくなります。さらに、大規模な機械であるため、設置場所にも十分なスペースが必要です。
結論として、フライス盤の活用は、そのメリットを最大限に引き出すことができれば、製造業において大きな競争力をもたらすことができます。しかし、そのためには、適切な技術者の確保やコスト管理が重要になります。フライス盤を導入する際は、これらの点を慎重に考慮することが求められます。
6-2. 各加工法の適用範囲と選択基準
フライス盤は、金属や木材の加工に広く使われる機械で、その活用には多くのメリットがありますが、いくつかのデメリットも存在します。まず、フライス盤の最大のメリットは、高い精度で複雑な形状の加工が可能である点です。例えば、ギアやカムなどの精密部品を作成する際には、この機械が不可欠です。さらに、多様な切削ツールを装着できるため、一台で多彩な加工が行える点も大きな魅力です。
しかし、デメリットとしては、高い導入コストが挙げられます。特に、最先端のフライス盤を導入する場合、その費用は小規模な工場や個人の職人にとって大きな負担となることがあります。また、操作には専門的な知識や技術が必要であり、熟練した操作者が不足している場合、その性能を十分に発揮させることが難しい場合があります。
結論として、フライス盤は多様な加工が可能であり、製品の品質向上に寄与する非常に有効な機械です。しかし、導入と運用にはコストや技術的な課題が伴います。これらを踏まえた上で、自社のニーズに合ったフライス盤を選定することが重要です。
6-3. フライス加工と旋削加工の組み合わせと応用
フライス盤を活用することは、多くの製造現場で重要なプロセスです。その主な理由は、フライス盤が提供する高い柔軟性と精度にあります。フライス盤を用いれば、複雑な形状や細かい加工も可能になり、製品の品質を一層向上させることができます。例えば、精密なギアや航空宇宙部品の製造において、フライス盤の能力は不可欠です。しかしながら、フライス盤を使用するには高度な技術と経験が必要であり、また、設備投資の初期費用が高いというデメリットも存在します。このため、小規模な製造業者にとっては導入が難しい場合もあります。しかし、長期的に見れば、フライス盤の導入は製品の品質向上と生産効率の向上に大きく寄与するため、そのメリットはデメリットを上回ると言えるでしょう。結局、フライス盤を適切に活用することで、製造業の競争力を高めることが可能です。
6-4. 加工方法選択時の注意点と最適化のヒント
フライス盤は、金属加工の分野において広く利用されている重要な機械です。そのメリットは大きく、しかし注意すべきデメリットも存在します。フライス盤の最大のメリットは、その高い精度と多様性にあります。複雑な形状や精密な部品の加工が可能であり、一台で多くの加工を行えるため、製造業において非常に重宝されています。例えば、自動車のエンジン部品や航空機の部品製造など、高い精度が求められる場面で活躍します。
しかし、デメリットとしては、高いコストが挙げられます。フライス盤自体の価格だけでなく、操作を行うためには高度な技術が必要となり、適切な訓練を受けたオペレーターを雇う必要があります。また、複雑な設定やプログラミングが求められることが多く、初期投資として大きな負担がかかることも少なくありません。
結論として、フライス盤はその高い加工能力により多くのメリットを提供しますが、高コストや操作の難しさといったデメリットも考慮する必要があります。製造プロセスにフライス盤を導入する場合は、これらの点を総合的に検討し、最適な運用方法を見つけることが重要です。
まとめ
フライス盤は、精密加工や金属加工において非常に重要な機械です。そのメリットとしては、高精度な加工が可能であり、複雑な形状も加工できる点が挙げられます。一方、デメリットとしては、大きなスペースが必要であり、設置や操作には専門知識が必要となります。また、メンテナンスも必要であるため、適切な管理が求められます。加工品質を重視する場合や大量生産に向いているフライス盤ですが、その活用には慎重な計画と適切なスキルが不可欠です。
工作機械の選択:フライス盤が持つ長所と短所
工作機械の選択は、製造業における重要な決定です。特に、フライス盤はその性能や特性によって注目を集めています。フライス盤のメリットとデメリットを理解することは、効果的な選択をする上で不可欠です。
フライス盤は、精密な加工や複雑な形状の加工に適しており、その高度な制御システムによって幅広い用途に活用されています。一方で、運用やメンテナンスには専門知識が必要であり、初期投資も比較的高額となることが課題となります。
本記事では、フライス盤の選択における重要な要素としてのメリットとデメリットについて詳しく解説します。製造業に携わる皆さんにとって、フライス盤の選択がより明確になるように、是非ご一読ください。
1. フライス盤とは?
1-1. フライス盤の基本的な概要
フライス盤は、金属加工の現場で広く使用される工作機械の一つです。この機械の最大の長所は、その汎用性にあります。複雑な形状や細かい加工が要求される部品でも、フライス盤を使用することで精密な加工が可能となります。例えば、歯車や溝、平面など、多種多様な処理を一台でこなすことができます。これは、様々な切削工具を装着することで、多角的に対応できるためです。
しかし、フライス盤の短所も存在します。その一つが、機械自体のコストの高さです。高性能なフライス盤は、非常に高価であり、特に中小企業や個人の工作室では導入が難しい場合があります。また、操作や設定には専門的な知識が必要であり、熟練した技術者が不可欠となります。
総じて、フライス盤はその汎用性と高い加工能力により多くの工場で重宝されていますが、高コストや専門知識が要求される点が短所として挙げられます。適切な導入検討と熟練したオペレーターの確保が、フライス盤を最大限に活用する鍵となるでしょう。
1-2. フライス盤の歴史と進化
フライス盤は多様な工作機械の中でも特に優れた汎用性と精密性を誇ります。これらの特性は、多くの製造プロセスにおいてフライス盤を不可欠な機械として位置づけています。しかし、フライス盤を選択する際には、その長所と短所の両方を理解することが重要です。
フライス盤の最大の長所は、その汎用性にあります。複雑な形状や困難な素材を加工することが可能であり、一台で多様な作業をこなせるため、製造の現場で高く評価されています。例えば、金属を削る作業だけでなく、穴を開けたり、溝を切ったりすることも可能です。これにより、さまざまな製品の製造にフライス盤が用いられています。
しかしながら、フライス盤を使用する際の短所も存在します。その一つは、高い技術が要求される点です。操作には専門知識と経験が必要であり、初心者には扱いが難しい場合があります。また、大型の機械であるため、設置には十分なスペースが必要です。そのため、小規模な工場や狭い作業スペースでは、設置が困難な場合があります。
結論として、フライス盤はその汎用性と精密性から多くの製造現場で重宝されていますが、操作には専門知識が必要であり、設置にも十分なスペースが要されます。これらの長所と短所を理解し、自身の製造ニーズに合った選択をすることが、効果的なフライス盤活用の鍵と言えるでしょう。
2. フライス盤のメリット・デメリット
2-1. フライス盤の長所
フライス盤は、その多様性と精密さで多くの工業分野で重宝されています。主な長所として、複雑な形状や平面、溝など、多様な加工が一台で可能である点が挙げられます。例えば日本の自動車産業では、エンジンや車体の一部分をフライス盤で加工することが一般的です。この柔軟性は、少量多品種の生産が求められる今日の製造業において特に価値があります。
一方で、フライス盤の短所としては、比較的大きな初期投資が必要であること、そして操作には専門的な技術が必要であることが挙げられます。特に小規模な工場や初めてフライス盤を導入する場合、そのコストと習熟には注意が必要です。
結論として、フライス盤はその多様性と精密性により高い価値を持ちますが、導入にはコストと技術面での検討が必要です。適切に選択し、使用することで製造業の柔軟性と生産性を高めることが可能です。
2-2. フライス盤の短所
フライス盤は金属加工において多用される工作機械であり、その多様性と精密さで多くのメリットを提供しますが、短所も存在します。主な短所として、初期投資とメンテナンス費用の高さが挙げられます。フライス盤の高度な機能性は、それに応じたコストがかかるため、特に小規模な工場やスタートアップにとっては大きな負担となり得ます。さらに、操作には専門的な技術が必要であり、熟練したオペレーターの不足は、生産性の低下を招く可能性があります。例えば、日本では技術者の高齢化が進んでおり、若手の技術者不足が課題となっています。このように、フライス盤はその優れた加工能力により多くの利点をもたらす一方で、コストや人材の面で短所も抱えています。
2-3. フライス盤と旋盤の比較
フライス盤は、精密な加工が可能で多様な形状を創出できるため、製造業界で広く利用されています。その長所は、複雑な形状や溝、平面を加工できる柔軟性にあります。たとえば、ギアやプロペラなどの精密部品の加工には欠かせません。また、様々な材料に対応でき、一つの機械で多くの作業が完結する点も大きなメリットです。
しかし、フライス盤には短所も存在します。高い技術を要するため、操作には熟練した技術者が必要であること、そして高価な機械であるため初期投資が大きくなる点が挙げられます。さらに、大型のフライス盤は場所を取るため、工場のスペースの確保も課題です。
結論として、フライス盤はその柔軟性と精密な加工能力によって多くの製造業で重宝されていますが、高い技術力と初期投資が求められる点は留意が必要です。適切な運用と熟練した技術者の育成が、フライス盤を最大限に活用する鍵となります。
3. フライス盤と旋盤の使い分け
3-1. 各工作機械の特徴と適用範囲
フライス盤は、精密な金属加工に不可欠な工作機械であり、その選択は製造業において重要な意味を持ちます。フライス盤の長所として、多様な加工が可能である点が挙げられます。これは、異なる形状やサイズの工具を使用し、平面、溝、歯車など、さまざまな加工を一台で行えるためです。特に、複雑な形状や精密な部品製造には、フライス盤のこの能力が不可欠です。
しかし、短所としては、比較的高い初期費用が必要であることが挙げられます。また、操作には専門的な知識と技術が必要であり、熟練した技術者が不足している場合、その有効活用には時間がかかることがあります。例えば、精密な部品を製造する際、設計通りの寸法や形状を実現するには、操作者の高度な技術が必須となります。
結論として、フライス盤はその多機能性により、さまざまな加工が一台で行える利点を持ちますが、高い初期投資と技術者の確保が課題です。適切な投資と人材育成により、これらの課題を克服することが、製造業における競争力の向上につながるでしょう。
3-2. 切削加工におけるフライス盤と旋盤の役割
フライス盤は多様な加工が可能であり、その選択には明確な長所と短所が存在します。フライス盤の最大の長所は、その汎用性にあります。平面、溝、複雑な形状の切削が可能で、様々な材料に対応できるため、幅広い製品の加工に利用されています。例えば、自動車の部品や航空機の部品製造に不可欠です。しかし、この汎用性が短所ともなり得ます。特殊化された加工を要求される場合、フライス盤だけでは対応しきれないことがあります。さらに、高度な技術を要する操作が必要とされるため、操作者のスキルに依存する部分も大きいです。
結論として、フライス盤はその汎用性から多くの製造現場で重宝される一方で、特化した加工や高度な技術が求められる場合には限界もあります。これらの長所と短所を理解し、適切な場面での使用が、効率的な製造プロセスに繋がります。
4. 強力NCフライス盤の選択基準
4-1. NCフライス盤の機能と特性
フライス盤、特にNC(数値制御)フライス盤は製造業で不可欠な機械です。その選択にあたり、長所と短所を理解することが重要です。フライス盤の最大の長所は、精度の高さと複雑な形状の加工能力にあります。数値制御により、一貫した結果を得ることが可能で、これは特に大量生産を要する場合に有利です。例えば、自動車部品や航空機部品など、精密な仕上がりが必要な製品の製造に適しています。また、プログラムの変更が容易であるため、様々な形状の加工に迅速に対応できる点もメリットとして挙げられます。
一方で、短所としては、初期投資が高額であることが挙げられます。NCフライス盤は従来型のフライス盤に比べて高価であり、導入には大きなコストがかかります。さらに、操作やプログラミングには専門知識が必要となり、熟練した技術者が不可欠です。これは、特に中小企業にとっては大きな負担になり得ます。
結論として、NCフライス盤はその精度の高さと柔軟な加工能力により、多くの製造業で重宝されています。しかし、高額な初期投資が必要であり、操作には専門知識が求められます。それらの長所と短所を慎重に検討した上で、自社のニーズに合ったフライス盤の選択をすることが肝心です。
4-2. 強力NCフライス盤の仕様と性能
フライス盤を選択する際、その長所と短所を把握することが重要です。フライス盤は高い精度や多様な加工が可能というメリットを持ちますが、反面、設備投資の大きさや操作の複雑さといったデメリットも存在します。
まず、フライス盤の最大の長所は、その加工の精度と多様性にあります。例えば、平面や曲面、溝など、複雑な形状も精密に加工できるため、自動車や航空機の部品製造など、幅広い産業で活用されています。また、多軸制御が可能なフライス盤では、一度の設定で複数面の加工も行え、効率的な生産が可能です。
しかし、このような多機能性は、設備投資が大きくなる一因ともなります。特に最新鋭のフライス盤は価格が高く、小規模な製造業にとっては大きな負担となる場合があります。また、操作の複雑さも課題であり、操作者の技術習得には時間とコストがかかります。
結論として、フライス盤を選択する際には、その高い加工能力と多様性を評価する一方で、設備投資の規模や操作スタッフの教育についても慎重に検討する必要があります。適切なフライス盤を選ぶことで、製造業の生産性や品質の向上につながります。
4-3. 購入前に考慮すべきポイント
フライス盤の選択に際しては、その長所と短所を理解することが重要です。フライス盤の最大の長所は、その汎用性にあります。多様な材料を加工することができ、平面、曲面、溝など、複雑な形状も精密に加工可能です。例えば、機械部品や工具、金型などの製造に欠かせない設備です。また、CNCフライス盤を使用すれば、プログラムによる自動加工も可能で、一貫した高精度な加工が行えるため、大量生産にも適しています。
しかし、デメリットも存在します。フライス盤はその性能やサイズによって価格が高額になることがあり、初期投資が大きくなる可能性があります。また、操作やプログラムの設定には専門知識が必要で、熟練した技術者が不足している場合、その能力を十分に発揮できないこともあります。さらに、大型のフライス盤は設置スペースを多く必要とし、小規模な工場では導入が難しい場合もあります。
締めくくりとして、フライス盤を選択する際は、その長所としての汎用性と高精度な加工能力を活かすことができる一方で、初期投資や運用の難しさという短所も十分に考慮する必要があります。最適なフライス盤を選択することで、製造工程の効率化と製品品質の向上につながります。
5. フライス盤の選び方とメーカー比較
5-1. フライス盤の選択ポイント
フライス盤を選択する際には、その長所と短所を理解することが重要です。フライス盤の最大の長所は、高い精度と柔軟性にあります。複雑な形状や平面、溝など、多様な加工が一台で可能であり、特に小ロットや多品種の製品製造に適しています。例えば、精密部品や特殊な形状の加工にはフライス盤が不可欠です。また、様々な切削工具を使い分けることで、幅広い材料に対応可能な点もメリットです。
一方で、デメリットとしては、初期投資が高いことや、操作に高度な技術が必要な場合があることが挙げられます。特に高性能なフライス盤は価格が高く、中小企業にとっては購入が難しい場合もあります。また、複雑な機械のため、使用方法を習得するまでに時間がかかることもあります。
結論として、フライス盤はその高い加工能力と柔軟性により、多様な製造ニーズに対応できる優れた機械です。しかし、高い初期投資が必要であり、操作には技術が求められます。したがって、購入を検討する際には、これらの長所と短所をしっかりと考慮することが重要です。
5-2. 信頼性と評判に基づくメーカー比較
工作機械の選択は製造業にとって重要な意志決定の一つです。特にフライス盤に関しては、その長所と短所を理解することが選択の鍵となります。フライス盤は多様な材料を精密に加工できる点が最大の長所です。これは、金属からプラスチックまで、幅広い材料に対応可能ということを意味します。たとえば、自動車部品の製造や航空機の部品加工など、様々な産業でのニーズに応えることができます。
しかし、フライス盤の短所も無視できません。一つは、高い初期投資が必要なことです。特に、精度が高く多機能な機械ほど価格は高くなります。また、操作には専門的な技術と知識が要求され、熟練したオペレーターが不足している場合、その能力を十分に発揮できない可能性があります。
フライス盤を選択する際は、これらの長所と短所を総合的に考慮することが重要です。例えば、高い精度と多様性が求められる製造業では、初期投資や技術者の確保に対する課題を克服する価値があるかもしれません。一方で、単純な作業が中心の場合は、投資対効果を慎重に検討する必要があります。
結論として、フライス盤はその優れた加工能力により多くの産業で重宝されていますが、高いコストと専門技術の要求という短所も持ち合わせています。選択にあたっては、製造のニーズとこれらの短所を慎重に比較検討することが求められます。
5-3. 価格と機能性のバランス
フライス盤の選択にあたっては、その長所と短所を理解することが重要です。フライス盤は、精密な加工が可能であり、多様な形状を創出することがその最大の長所です。例えば、複雑な曲面や溝を加工する場合、フライス盤は非常に有効です。これらの特性は、自動車や航空機の部品製造など、高度な技術を要する分野で特に求められています。
一方で、フライス盤の短所としては、初期投資の高さが挙げられます。高品質なフライス盤はその性能と耐久性のために高価であり、特に小規模な製造業者にとっては大きな負担となることがあります。また、操作には専門的な知識と技術が必要であり、適切なトレーニングが無ければ、機械の潜在能力を十分に引き出すことが難しいです。
結論として、フライス盤はその精密な加工能力によって多くの産業で不可欠な機械ですが、高価であり、操作には専門的な技術が必要です。これらの点を踏まえた上で、フライス盤の導入を検討することが求められます。
6. 切削加工の基礎知識
6-1. 切削加工とは?
フライス盤を選択する際には、その長所と短所を理解しておくことが重要です。フライス盤は、金属やプラスチックなどの材料を加工するための工作機械で、特に複雑な形状や平面を削り出すのに適しています。日本では、精密な加工が求められる製品製造において重宝がられています。
フライス盤の最大の長所は、その柔軟性にあります。異なる種類の切削ツールを装着することで、様々な形状の加工が可能となり、一台で多目的に使用できるため、設備投資の削減にも繋がります。例えば、平面はもちろん、溝や歯車などの加工もフライス盤一台でこなすことができます。
しかし、フライス盤には短所も存在します。その一つが、大量生産には向かない点です。フライス盤は柔軟性が高い反面、設定や切削ツールの交換に時間がかかるため、同じ作業を繰り返し行う大量生産には不向きです。また、高度な技術を要する操作が必要な場合もあり、操作に熟練した技術者が必要となる場合もあります。
結論として、フライス盤はその柔軟性と多様性により、特定の加工ニーズに合わせた製品製造には非常に適しています。しかし、大量生産や特化した製造プロセスを求める場合には、他の工作機械の選択も検討する必要があります。日本の製造業でフライス盤を選択する際には、これらの長所と短所を踏まえた上で、製品の特性や生産体制に最適な機械選びを心掛けることが重要です。
6-2. 工作機械の種類と特徴
フライス盤は、その多様性と用途の広さで知られる工作機械です。しかし、これを選択する際には、その長所と短所を理解しておくことが重要です。フライス盤の最大の長所は、複雑な形状や正確な平面を削り出す能力にあります。例えば、金型の製作や部品の加工など、精密な作業が求められる場面で重宝されます。また、異なる種類の切削工具を装着することで、幅広い材料を加工できる汎用性もフライス盤の大きな利点です。
しかし、短所も存在します。フライス盤はその性能を最大限に発揮するためには、操作する技術者のスキルが求められます。高度な技術が必要なため、初心者には扱いが難しい場合があります。また、大きなフライス盤は場所を取るため、小規模な工場では設置スペースの問題が生じることもあります。
結論として、フライス盤はその多様性と高い精度で多くの製造業で重宝されていますが、操作には技術が必要であり、設置には十分なスペースが求められるという点を考慮する必要があります。適切な選択と運用により、フライス盤は製造業での生産性向上に大きく貢献することができます。
6-3. 切削工具の選択と使用法
フライス盤は製造業において不可欠な切削工具の一つです。その選択には、フライス盤が持つ多くのメリットといくつかのデメリットを理解することが重要です。フライス盤の最大の長所は、その高い精度と多様性にあります。例えば、平面、溝、歯車など、様々な形状を加工できることが挙げられます。さらに、一定の設定の下で長時間安定した加工が可能であるため、大量生産にも適しています。
しかし、フライス盤を使用する際にはデメリットもあります。その一つが、高い初期投資が必要な点です。また、操作や設定には専門的な知識が必要となり、熟練した技術者が不足している場合、その機能を十分に活かすことが難しいこともあります。さらに、大きな機械であるため、設置には十分なスペースが必要です。
結論として、フライス盤はその高精度と多様性で製造業における幅広い加工ニーズに応えることができます。しかし、高い初期投資や専門的な操作知識が必要な点を理解し、自社のニーズに合った機械選択を行うことが重要です。適切な選択と運用により、フライス盤は製造プロセスの効率化と品質向上に大きく貢献することでしょう。
7. CNC工作機械の選択方法
7-1. CNC技術の基本
工作機械の選択においてフライス盤は、その汎用性と精密性により高い評価を受けています。フライス盤の最大の長所は、複雑な形状や硬質材料の加工が可能であることです。この特徴により、自動車の部品や精密機械の製造に不可欠な役割を担っています。例えば、エンジンの部品など、細かい加工が必要な製品の製造には、フライス盤が用いられることが多くあります。しかしながら、フライス盤はその汎用性に対して、高い技術を要求されることが短所として挙げられます。操作には熟練した技術が必要であり、加工誤差を最小限に抑えるためには高度な知識が求められます。さらに、設備投資としての初期コストも高く、小規模な製造業者にとっては導入が難しい側面もあります。結論として、フライス盤はその高い汎用性と精密性により多くの製造業で重宝されていますが、操作や初期投資における課題も持ち合わせています。適切な訓練と予算計画により、これらの課題を乗り越えることが可能です。
7-2. CNCフライス盤の選択ポイント
フライス盤は、金属加工の現場で欠かせない機械の一つです。特に、CNCフライス盤は高精度な加工が可能であり、多くの企業が利用しています。この機械選択の際に知っておくべき長所と短所を考えてみましょう。
まず、長所としては、複雑な形状や精密な部品の加工が可能である点が挙げられます。例えば、航空宇宙産業や自動車産業で使われる部品の製造には、このような高度な加工技術が必要不可欠です。また、CNCフライス盤を使用することで、加工の自動化が進み、生産効率の向上が期待できます。
一方で、短所としては、高い初期投資が必要であることが挙げられます。特に、最新技術を取り入れた高性能のフライス盤は価格が高く、中小企業にとっては大きな負担となることがあります。加えて、操作やプログラミングには専門的な知識が必要であり、熟練した技術者が不足している場合、その効果を十分に発揮できないことがあります。
結論として、CNCフライス盤はその精密さと効率の良さで多くの製造業界で重宝されていますが、導入にあたっては初期投資の負担や技術者の確保といった課題も把握しておく必要があります。適切な機械選択を行うことで、製造プロセスの向上とコスト削減につながります。
7-3. 適したCNC工作機械の選択基準
フライス盤は、多様な材料を加工できる柔軟性と高精度での作業能力が魅力で、製造業で広く利用されています。しかし、適切なフライス盤を選択するには、その長所と短所を理解することが不可欠です。
フライス盤の大きな長所は、その汎用性にあります。金属、プラスチック、木材など、さまざまな材料の加工が可能であり、複雑な形状や曲線を正確に加工することができます。また、CNCフライス盤の場合、プログラムによって自動運転が行え、一度に多くの部品を高い精度で製造することができる点も大きなメリットです。
一方で、短所としては、初期投資コストが高いことが挙げられます。特に最新のCNCフライス盤は高価であり、小規模な製造業者にとっては、その購入が難しい場合もあります。また、操作やプログラミングには専門知識が必要で、熟練したオペレーターやプログラマーを確保することも課題となります。
結論として、フライス盤はその汎用性と高精度な加工能力により多くのメリットを提供しますが、高い初期投資や技術者の確保といった課題もあります。このため、フライス盤を導入する際には、その長所と短所を十分に考慮し、自社のニーズに最も合った機種の選択が重要です。
まとめ
フライス盤は工作機械の一種であり、その利点と欠点を正しく理解することが重要です。フライス盤の主なメリットには、高い精度での加工が可能であり、広範囲の材料に対応できるという点が挙げられます。一方で、フライス盤のデメリットとしては、大規模な設備や高い運用コストがかかることが挙げられます。工場の生産能力や加工ニーズに合わせて、フライス盤を選択する際には注意が必要です。
アルミの加工性を徹底解説!初心者にもわかる加工のポイント
アルミの加工性について知りたいけれど、初心者にとっては難しいと感じることもあるかもしれませんね。しかし、安心してください!この記事では、アルミの加工性を徹底的に解説し、初心者の方々にもわかりやすい加工のポイントをお伝えします。
アルミは加工しやすい素材として知られていますが、その理由やポイントを知ることで、より効果的に取り組めるようになるでしょう。加工の基礎から応用まで、この記事ではアルミの加工性について包括的に紹介します。さあ、アルミの素材特性を活かした加工の世界へ一歩踏み出してみましょう!
1. アルミ加工の基本
1-1. アルミとは?基本的な性質と特徴
アルミニウムは、その優れた加工性で知られています。実は、アルミは非常に柔軟性があり、熱や圧力を加えることでさまざまな形に加工することが可能です。これは、アルミニウムが持つ低い融点と、比較的低い密度に起因しています。具体的な例として、アルミは飛行機の部品や自動車のボディ、日用品の缶など、幅広い用途で利用されています。これらの製品は、アルミニウムが軽量でありながら強度を持っているため、選ばれています。
また、アルミニウムは優れた耐食性を持つため、外部の環境にさらされる製品にも適しています。たとえば、食品を保存するための容器や建築材料としても、アルミは広く採用されています。これらの特性から、アルミニウムは加工しやすい金属として、様々な産業で重宝されているのです。
結論として、アルミニウムはその加工性の高さから多岐にわたる用途で使用されています。軽量でありながら強度を持つこと、さらに耐食性にも優れているため、初心者にも扱いやすい素材と言えるでしょう。これらの理由から、アルミは日々の生活から産業界に至るまで、広く利用されているのです。
1-2. アルミ加工の種類とその利点
アルミニウムはその優れた加工性から、様々な製品の材料として広く利用されています。初心者でも理解しやすいように、アルミの加工性のポイントを解説します。まず、アルミは軽量でありながら強度が高いという特性を持っています。これにより、自動車や航空機の部品など、重量を抑えつつ耐久性が求められる製品に適しています。また、アルミは熱伝導率が高く、熱を効率的に伝えることができるため、冷却装置やキッチン用品などにも使用されます。
特に日本でのアルミ加工技術は高いレベルにあり、精密な部品製造が可能です。例えば、日本の電子機器や自動車産業では、複雑な形状や細かい部品をアルミで作成することが一般的です。これらの産業では、アルミの加工性が製品の品質を左右する重要な要素となっています。
結論として、アルミはその軽量性、強度、熱伝導率の高さから、多岐にわたる用途に適しており、特に日本の高度な加工技術によって、その利点を最大限に活かすことができます。アルミ加工の種類とその利点を理解することは、さまざまな産業での製品開発やイノベーションに繋がります。
1-3. アルミは加工しやすいですか?アルミの加工性について
アルミニウムは、軽量でありながら強度を持つ素材として、多くの産業で活用されています。その理由の一つに、アルミニウムが加工しやすいという特性があります。ここでは、その加工性について、その理由と具体例を通じて解説します。
まず、アルミニウムは柔らかく加工しやすい金属であるため、押し出しや曲げ加工、切断などのさまざまな方法で形状を変えることができます。例えば、自動車のボディパーツや家庭用のアルミホイルなどが挙げられます。これらの製品は、アルミニウムの加工性を活かして様々な形に加工されています。
さらに、アルミニウムは耐食性にも優れており、さびにくい特性があるため、屋外で使用される製品にも適しています。たとえば、自転車のフレームや建築材料など、耐久性が求められる場所での使用が一例です。
このように、アルミニウムはその加工しやすさと耐久性から、幅広い用途で活用されています。初心者でも理解しやすいように、アルミニウムの加工性とは、その柔らかさと強度、さらには耐食性によって、さまざまな形状に加工しやすく、長期間使用できる特性を指します。この特性が、多くの産業でアルミニウムが選ばれる理由の一つとなっています。
1-4. アルミ加工に適した工具と設備
アルミはその加工性の高さから、多くの産業で広く使用されています。加工がしやすいという点で、初心者にも取り組みやすい素材です。アルミ加工のポイントを理解することで、さらに効率良く、質の高い製品を作ることが可能になります。
アルミの加工性の高さの理由は、その軽量性と強度にあります。また、熱伝導率が高く、耐腐食性に優れているため、多様な加工方法が可能です。例えば、切削加工では、アルミ専用の刃物を使用することで、滑らかな仕上がりを得ることができます。曲げ加工においても、アルミの柔軟性を活かし、複雑な形状でも精確に加工することができるのです。
また、アルミは溶接性にも優れています。特殊な技術を必要とすることなく、比較的容易に溶接加工ができるため、さまざまな製品の製造に適しています。ただし、アルミ加工には適した工具や設備が必要となります。たとえば、アルミ専用の切削液を使用することで、加工中の熱を効率良く逃がし、工具の摩耗を防ぐことができます。
結論として、アルミは加工しやすい素材であり、適切な工具や設備、技術を用いることで、初心者でも高品質な加工が可能です。アルミ加工の基本を理解し、適切な手法を選択することが、製品品質の向上に直結します。
2. アルミ板加工のコツ
2-1. アルミ板の選び方と準備
アルミは、その優れた加工性により、多くの産業で広く使われています。初心者にもわかりやすくアルミの加工ポイントを解説します。まず、アルミは軽量でありながら強度が高く、熱伝導率や耐食性にも優れているため、加工しやすい金属です。例えば、自動車や飛行機の部品、キッチン用品など、身の回りにある多くの製品にアルミが使用されています。
加工の際には、アルミ板の厚さや硬度、用途に応じて適切な加工方法を選ぶことが重要です。例を挙げると、薄いアルミ板は曲げ加工が容易であり、装飾品や軽量部品の製造に適しています。一方、厚いアルミ板は、強度が必要な自動車のボディや建築材料に利用されます。また、アルミは溶接や切削といった様々な加工方法にも適しており、これらの技術を駆使することで、複雑な形状の製品製造にも対応可能です。
結論として、アルミの加工性の良さは、その軽量性、強度、耐食性に起因しています。アルミ板を選ぶ際には、その用途に最適な厚さや硬度を考慮し、適切な加工方法を選択することがポイントです。これにより、初心者でもアルミ加工の基本を理解し、幅広い用途に対応できる製品を作り出すことができます。
2-2. 切断・曲げ・穴あけの基本テクニック
アルミニウムはその軽量さと強度を活かして、自動車や航空機、電子機器など多岐にわたる分野で使用されています。その加工性の良さから初心者にも扱いやすく、さまざまな製品の製造に利用されています。その理由として、アルミニウムは比較的柔らかく加工しやすい金属であり、切断、曲げ、穴あけなどの加工が容易であることが挙げられます。例えば、切断には金属用のノコギリや切断機が使われ、曲げにはプレス機や手動での作業が適しており、穴あけにはドリルが使用されます。これらの加工は特別な設備や技術を必要とせず、基本的なツールと注意を払うことで、比較的簡単に行うことができます。ただし、アルミニウムは加熱によって硬化する性質も持つため、加工時には温度管理にも注意が必要です。結論として、アルミニウムはその加工のしやすさから初心者にも扱いやすく、多くの製品の製造に役立てられることが理解できます。
2-3. 表面処理と仕上げの方法
アルミニウムは加工しやすい素材として知られています。その理由は、アルミニウムが持つ柔軟性と耐久性にあります。例えば、アルミニウムは比較的低温で溶けるため、押し出しや鋳造などの加工が容易に行えます。また、軽量でありながら強度が高いため、自動車や航空機の部品、日用品など幅広い用途で利用されています。
加工の際のポイントとして、アルミニウムの表面処理は特に重要です。アルミニウムは自然に酸化皮膜を形成し、耐食性を高めますが、さらにアルマイト処理を施すことで耐久性が向上します。アルマイト処理を行うことで、製品の寿命を延ばし、美観を保つことができます。また、アルミニウムの塗装も一般的な方法の一つです。これにより、製品に色を付けることが可能となり、用途に応じたカスタマイズが可能になります。
このように、アルミニウムの加工性はその柔軟性と耐久性に由来しており、表面処理の方法によっては、その特性をより一層引き出すことが可能です。これらのポイントを押さえることで、初心者でもアルミニウムの加工に関する理解を深めることができます。
2-4. アルミ板加工の際の一般的なトラブルと対策
アルミはその軽量性と強度のバランスから、様々な工業製品にとって非常に魅力的な材料です。特に、加工性の良さはアルミを使用する大きな理由の一つとなっています。しかし、加工する際にはいくつか留意すべき点があります。
まず、アルミは熱伝導率が高いため、加工時には熱が素早く分散します。これは加工速度が速くなる利点がある反面、不均一な加熱により材料が歪む原因ともなり得ます。したがって、適切な冷却手段を取りながら加工することが重要です。
加工における一般的なトラブルとしては、アルミの柔らかさからくる切削時のバリが挙げられます。この問題に対処するためには、切削工具の選定や切削速度の調整が効果的です。例えば、アルミ専用の刃物を使用し、適切な速度で加工することで、バリの発生を抑えることが可能です。
また、アルミの表面処理においても注意が必要です。アルミは表面が酸化しやすく、これが原因で塗装や接着が困難になることがあります。このような場合、表面処理技術を用いて酸化層を除去し、処理後のアルミ表面が適切な状態を保つようにします。
結論として、アルミの加工性は非常に良いものの、その特性を理解し、適切な加工方法を選択することが重要です。材料の熱伝導率、柔らかさ、および表面処理の要件を考慮に入れ、それぞれに適した方法で加工を行うことで、トラブルを避けることができます。
3. 旋盤加工でのアルミ加工の基礎知識
3-1. 旋盤加工のプロセスとアルミの取り扱い
アルミニウムはその優れた加工性で知られ、初心者でも扱いやすい素材です。この記事では、特に旋盤加工においてアルミの取り扱い方を解説します。まず、アルミは比較的柔らかく、熱伝導率が高いため、加工時に生じる熱が素早く逃げる性質を持っています。このため、加工時に生じる温度上昇が抑えられ、切削工具にかかる負担が少なくなります。例えば、アルミ合金A6061はその加工性の良さで広く利用されています。この合金は、航空機の部品や自動車の部品など、精密な加工が要求される分野で特に重宝されています。さらに、アルミは再加工が容易であり、加工後の材料の再利用が比較的簡単なため、環境に配慮した材料としても注目されています。結論として、アルミの加工性の良さは、その物理的特性に起因しています。初心者にとっても、扱いやすい素材であり、様々な用途に応じた加工が可能です。
3-2. アルミ旋盤加工のための切削条件の設定
アルミニウム(アルミ)は、その加工のしやすさから多くの産業で利用されています。特に、旋盤加工においては、アルミの性質を理解して適切な切削条件を設定することが重要です。アルミは軽くて加工性が良いため、初心者にも取り扱いやすい素材の一つです。しかし、その軟らかさ故に、加工時には切削速度や送り速度、切削液の選択に注意が必要です。
たとえば、アルミの旋盤加工では、高い切削速度を利用することができます。これは、アルミの熱伝導率が高いため、加工中に生じる熱を素早く逃がすことができるからです。しかし、切削速度が高すぎると、工具の摩耗が早まったり、加工面に傷がつく可能性があります。そのため、加工するアルミの種類や形状に合わせて、適切な切削速度を選択することが重要です。また、アルミは粘り気があるため、切削液を適切に使用することで、切りくずの排出を助け、加工精度を向上させることができます。
このように、アルミの旋盤加工においては、その特性を踏まえた上で切削条件を適切に設定することが、加工効率と品質の向上に繋がります。アルミは加工しやすい素材ではありますが、その性質を理解し、適切な加工方法を選択することが成功の鍵となります。
3-3. 旋盤加工時の冷却液の役割と選択
アルミニウムはその軽量さと強度のバランスから、多くの産業で利用されています。また、加工しやすいという特性もアルミニウムの大きな利点の一つです。では、なぜアルミニウムは加工しやすいのでしょうか?その理由として、アルミニウムは比較的柔らかく、熱伝導率が高いため、切削や曲げなどの加工時にエネルギーが少なくて済み、また加工時の熱が素早く逃げるため、加工精度も高くなります。具体的な例として、アルミニウムは航空機の部品や自動車の部品、さらには日用品まで幅広い分野で利用されています。これらの部品では、アルミニウムの加工性が高い点が非常に重要です。最終的に、アルミニウムの加工しやすさは、その利用範囲を広げ、多くの産業で重宝される理由となっています。このように、アルミニウムは加工性に優れ、様々な分野での応用が可能であることが理解できるでしょう。
4. アルミ加工の方法と注意点
4-1. アルミ加工の一般的な方法と流れ
アルミはその軽量性や耐食性に優れ、多岐にわたる産業で利用されています。その加工性の良さは、初心者にも取り扱いやすい重要なポイントです。ここでは、アルミの加工性が高い理由と、具体的な加工方法の例を簡単に解説します。
まず、アルミは柔らかく、加工しやすい性質を持っています。これは、アルミニウム合金が作業しやすく、形状を変えやすいためです。例えば、切削加工では、アルミは少ない力で切断や削り取りが可能です。また、曲げや押し出し加工も、アルミの柔軟性により、簡単に形状を作り出すことができます。
具体的な加工方法の例としては、CNC(コンピュータ数値制御)マシニングがあります。これは、コンピュータのプログラムに従って自動でアルミを切削する技術で、複雑な形状でも正確に加工できるため、精密な部品製造に適しています。
このように、アルミはその加工しやすさから、多くの製造分野で重宝されています。初心者でも扱いやすいことから、DIYや趣味の工作材料としても人気が高く、その用途はますます広がっています。アルミの加工性を理解することで、より多くの可能性をこの素材から引き出すことができるでしょう。
4-2. アルミ加工時の安全対策と保護具
アルミは加工しやすい素材として知られていますが、適切な方法で加工しなければなりません。その理由は、アルミが持つ独特の物理的特性にあります。例えば、アルミは軽量でありながら高い耐久性を持ち、熱伝導性も優れているため、多くの工業製品や建築材料に利用されています。しかし、これらの特性が加工時には特別な注意を要する場合があります。
具体的には、アルミの加工においては、その軟らかさと熱伝導性が関係してきます。アルミは比較的柔らかい金属なので、加工時には形が崩れやすく、また、熱を伝えやすいため、過度の加熱による品質の劣化が起こりやすいです。これを防ぐためには、適切な切削液の使用や、加工速度の調整が重要です。たとえば、アルミニウム合金を加工する際には、専用の切削液を使うことで熱の発生を抑え、品質を保つことができます。また、旋盤などで加工する際には、回転速度を適切に設定することが、アルミの加工性を高めるポイントです。
結論として、アルミは加工しやすい素材ですが、その特性に合わせた注意が必要です。軽量で耐久性があり、熱伝導性が高いアルミを上手く扱うことで、さまざまな用途に合わせた高品質な製品を作ることができます。加工時の適切な切削液の使用や加工速度の調整を心がけることが、アルミ加工の成功への鍵となります。
4-3. アルミ加工の品質を左右する要因
アルミニウムはその加工性の高さから、幅広い産業で利用されています。加工しやすさの背後には、アルミニウム特有の物理的特性が理由として挙げられます。例えば、軽量であることや、熱伝導性が高いことが、その加工性を支えています。これにより、自動車や航空機の部品、日用品など、様々な製品にアルミニウムが用いられています。
特に、アルミニウムは熱を加えることで柔らかくなり、成形しやすくなる特性を持っています。これは、熱伝導性が高いため、加熱時に材料全体が均一に温まりやすいからです。例を挙げると、アルミニウム箔はこの特性を生かし、薄く伸ばしても破れにくいため、食品の包装材料などに広く利用されています。
また、アルミニウムは再加工が容易で、リサイクルしやすいという利点もあります。これは、アルミニウムの融点が比較的低いためで、溶解して再び成形することが可能です。そのため、資源としての価値も高く、環境にやさしい素材としても注目されています。
結論として、アルミニウムの加工性の高さは、その物理的特性によるものであり、これが多岐にわたる用途での利用を可能にしています。加工しやすさ、リサイクルの容易さから、アルミニウムは今後も多くの産業で重宝されることでしょう。
4-4. アルミ加工の精度を高めるポイント
アルミは非常に加工しやすい素材であるということは、多くの人にとって重要なポイントです。その理由として、アルミの物理的特性が挙げられます。アルミは軽量でありながら強度が高く、熱伝導率も良いため、さまざまな加工技術に適しています。例えば、アルミは切削加工が容易であるため、精密な部品製造によく用いられます。また、アルミは曲げ加工やプレス加工もしやすく、機械部品や建築材料など幅広い用途で活用されています。
加工性を高めるためには、アルミの特性を理解し、適切な加工技術を選択することが重要です。例えば、アルミ合金の種類によって耐熱性や硬度が異なるため、使用目的に応じて最適な合金を選ぶ必要があります。さらに、加工時の温度管理や工具の選定も、加工精度に大きく影響します。適切な加工条件を選ぶことで、アルミの潜在的な性能を最大限に引き出すことが可能です。
結論として、アルミはその加工しやすさから、多様な産業で広く利用されている素材です。その加工性をさらに高めるためには、アルミの物理的特性を深く理解し、適切な加工技術を選択することが重要です。これにより、より高品質なアルミ製品の製造が可能となります。
5. アルミ加工の難しい理由と対策
5-1. アルミ加工が難しい理由とその背景
アルミは加工が比較的容易であり、初心者でも理解しやすい加工のポイントがいくつかあります。アルミの加工性の良さは、その軽量さと強度の高さに起因します。この性質がアルミを自動車や航空機材料として非常に人気のある選択肢にしています。具体的な例として、アルミは熱伝導性が良く、加工中に生じる熱を効率的に分散させることができます。これは、加工時に材料が損傷するリスクを減少させるために非常に重要です。また、アルミは柔らかい金属であり、加工機械への負担が少なく、切削や曲げ加工がしやすいという利点があります。しかし、この柔らかさが原因で精密な加工を行う際には注意が必要です。例えば、細かい部品を加工する場合、アルミの柔らかさが原因で加工精度が落ちることがあります。このような問題に対処するためには、適切な工具選択や加工パラメーターの調整が重要です。結論として、アルミはその加工性の良さから幅広い用途で使用されていますが、その特性を最大限に活用するには、加工方法についての基本的な理解が不可欠です。
5-2. アルミ加工の際の一般的な問題点
アルミはその軽量性や耐食性から、多くの産業で広く利用されています。特に、加工しやすいという点がアルミを更に魅力的な材料にしています。しかし、初心者にとってアルミ加工にはいくつか把握すべきポイントがあります。
主な理由として、アルミの熱伝導率が高いため、加工中に材料が急速に熱くなりやすいことが挙げられます。これを防ぐためには、適切な切削液の使用や適切な切削速度の選定が重要です。例えば、アルミニウム合金6061を加工する場合、一般的には高速での加工が推奨されますが、これは熱の発生を抑え、加工品質を保つためです。
また、アルミは柔らかいため、切削時には刃物による引っ掛かりが少なく、滑らかな仕上がりを期待できます。しかし、この柔らかさが原因で、加工中に材料が変形しやすいという問題もあります。具体的には、薄い部分の加工時には特に注意が必要で、サポートを使うなどして材料が安定するよう工夫することが大切です。
このように、アルミの加工はしやすいものの、熱の管理や材料の変形に注意する必要があります。適切な方法を用いれば、アルミの加工は初心者にも手軽に、そして効果的に行うことができます。アルミ加工の際は、これらのポイントを心掛け、成功への道を切り開きましょう。
5-3. アルミ加工の失敗を避けるためのテクニック
アルミはその軽量さと強度のバランスが取れているため、多くの産業で加工され使用されています。しかし、正しい知識がないと加工時に失敗する可能性もあります。アルミ加工の成功のカギは、材料の特性を理解し、それに合わせた技術を適用することにあります。例えば、アルミは熱伝導率が高く、加工時に熱が発生しやすいため、適切な冷却方法を用いることが重要です。また、アルミの柔らかさにより、加工時に刃物が材料に引っかかりやすいため、専用の切削液を使用すると良いでしょう。これらのポイントを抑えることで、アルミの加工精度を高め、加工後の仕上がりに差をつけることができます。結論として、アルミを加工する際は、その特性を十分に理解し、適切な加工方法を選択することが失敗を避ける上での最も重要なポイントです。
5-4. アルミ加工難易度を下げる工夫とアプローチ
アルミは加工しやすい素材として知られています。その理由は、アルミが持つ独自の物性にあります。例えば、軽量であることや、熱伝導性が高いことが挙げられます。これにより、加工時のエネルギー消費が抑えられ、加工精度を高めることができます。具体的には、アルミは薄い板材の成形や、複雑な形状への加工が可能であり、自動車や航空機の部品、さらには日用品まで幅広く用いられています。日本では、特に精密機械や電子機器の分野でその加工性の良さが活かされています。しかし、注意点もあります。アルミは柔らかい材質であるため、加工時に表面が傷つきやすい点や、切削工具の摩耗が早い点には工夫が必要です。例えば、適切な切削液の使用や、工具の材質選びが重要になります。加工技術の進歩によりこれらの問題も徐々に解決されつつあり、アルミの加工性をさらに高めることが可能です。結論として、アルミは加工しやすい素材であり、その特性を理解し、適切な加工方法を選ぶことで、様々な用途に応じた高品質な製品を効率良く生産することができます。
まとめ
アルミの加工性について理解し、初心者でもわかりやすく加工のポイントを抑えることが重要です。アルミは軽量で加工しやすい素材であり、切削や溶接、曲げなど幅広い加工方法が可能です。また、表面処理によって耐食性や耐摩耗性を向上させることもできます。初心者がアルミを加工する際には、適切な工具や技術を用いて安全かつ効果的に加工を行うことがポイントです。
加工方法の選択:フライスとマシニングの異なる利点とは?
工業製品の生産プロセスにおいて、加工方法の選択は極めて重要です。特にフライスとマシニングは、製造業においてよく用いられる2つの加工方法ですが、その違いを正確に理解することが必要です。本記事では、フライスとマシニングの異なる特性や利点について詳しく解説していきます。製造業に携わる方やこれらの加工方法に興味をお持ちの方にとって、参考になる情報が満載です。加工方法の選択に迷った際には、ぜひこのガイドをご活用いただき、自分に最適な選択を行ってください。
1. マシニング加工とフライス加工の基本
1-1. マシニング加工とは:基礎から理解する
フライス加工とマシニング加工は、製造業で広く使用される2つの異なる方法であり、それぞれが特有の利点を持ちます。フライス加工は、回転する工具を使用して材料から部品を削り出す方法です。この技術は、特に複雑な形状や大量生産が不要な場合に有効です。一方、マシニング加工は、高速で精密なカットを可能にするコンピュータ数値制御(CNC)マシンを使用します。これにより、極めて正確な寸法と複雑な形状の部品を効率的に製造できます。
例えば、フライス加工は航空宇宙産業で一部の特殊部品の製造に利用されることがあります。これらは、特定の強度や耐久性が求められるため、精密なカットが不可欠です。一方、マシニング加工は、自動車業界でのエンジン部品やギアなど、高い精度と大量生産が要求される部品に適しています。
結論として、フライス加工とマシニング加工は、それぞれ独自の利点を持ち、製造業の異なるニーズに応えることができます。選択は、製造する製品の要件、如何に精密である必要があるか、そして生産の規模によって決まります。適切な加工方法を選択することで、製品の品質、コスト、そして生産効率を最適化することができます。
1-2. フライス加工の概要
フライス加工とマシニングは、製造業で広く使用されている加工技術ですが、それぞれ独自の利点があります。最適な加工方法を選択することは、製品の品質、生産効率、コストを大きく左右します。フライス加工は、主に複雑な形状や大きな部品の加工に適しています。例えば、飛行機の部品や大型機械の部品製造に多用されています。これに対し、マシニング(CNC旋盤加工)は、精密な部品や複雑な内部形状を持つ小さな部品の加工に最適です。時計の小さな部品や精密機器の部品などがその例です。フライス加工は、大きな切削力と柔軟性を持ち、一方、マシニングは高精度と繊細な仕上がりが求められる場合に優れています。結論として、製品の要求仕様に応じて、これらの加工方法のどちらかを選択することが重要です。大きくて複雑な部品ではフライス加工が、小さく精密な部品ではマシニングが適しています。適切な加工方法を選択することで、効率的な生産と高品質な製品が実現します。
1-3. マシニングとフライスの歴史的背景
加工方法において、フライスとマシニングはそれぞれ異なる利点を持っています。この違いを理解することは、製品の効率的な製造に不可欠です。フライス加工は、特定の形状を作るために工具を回転させ、被加工物に対して多方向からアプローチする方法です。一方、マシニングは、高速で正確な切削が可能なコンピュータ制御の機械を使用し、複雑な形状や細部の仕上げに優れています。
例えば、フライス加工は平面や曲面、溝など、比較的単純な形状の加工に適しています。これに対し、マシニングは、3Dモデリングをもとにした複雑な形状や、より精密な仕上げを要求される製品の製造に最適です。日本の製造業では、時計の部品や自動車のエンジン部分など、精密な加工が求められる場合にマシニングが重宝されています。
このように、フライスとマシニングはそれぞれ異なる長所を持ち、製品の性質や加工の要件に応じて最適な方法が選ばれます。フライス加工の利点は、大量生産に適した比較的低コストでの加工が可能である点にあります。一方でマシニングは、高度な精密加工が可能であり、複雑な形状や精密な部品製造に不可欠です。結論として、フライスとマシニングの選択は、製品の要求に応じて適切に行うことが、効率的な製造プロセスの鍵となるのです。
2. フライスとマシニングの違いと特徴
2-1. フライス加工の利点と特性
フライス加工とマシニングでは、加工における多面的な利点が存在します。フライス加工は、主に平面や異形面の加工に適しており、その特性から大量生産にも適していると言えます。たとえば、自動車のエンジン部品や航空機の部品製造において、フライス加工は重宝されています。これは、フライス加工が高い精度を持ちつつ、比較的短時間で複雑な形状を創出できるからです。
一方、マシニングは、3次元的な加工が可能で、より複雑な形状や細部の加工に優れています。これにより、プロトタイプの製造や特殊な部品の加工に適しているといえます。例えば、独特なデザインのジュエリーや精密機器の部品など、細かい加工が必要な製品にはマシニングが選ばれることが多いです。
結論として、フライス加工とマシニングは、それぞれが持つ利点を生かして、製品の需要に応じた最適な選択が可能です。大量生産を前提とした場合はフライス加工が、複雑性や精密性を要する場合はマシニングが適しています。どちらの技術も、製造業における重要な役割を担っており、その選択は製品の品質や生産効率に大きく影響します。
2-2. マシニング加工の利点と特性
フライス加工とマシニング加工は、それぞれ異なる利点を持っています。フライス加工は、複雑な形状でも高精度で加工できる点が大きな利点です。これは、回転する工具を用いて材料を削り取る方法で、特に平面や溝、歯車などの加工に適しています。一方、マシニング加工は、3D CADデータをもとに、材料を削除していくことで、より複雑な形状や細部の精密な加工が可能です。この方法では、フライス加工よりもさまざまな形状を自由自在に加工できるため、プロトタイプ製作や小ロット生産に特に適しています。
例えば、フライス加工では、機械の構造上、特定の角度や深さでしか加工できない場合があります。しかし、マシニング加工では、5軸制御などの高度な技術を使うことで、これらの限界を克服し、より複雑な3D形状を高精度で加工することが可能になります。
結論として、フライス加工は平面や溝など比較的シンプルな形状の加工に適しており、高精度が求められる場合に有利です。一方で、マシニング加工は複雑な3D形状や細かいディテールの加工が可能であり、プロトタイピングや特殊な形状を必要とする小ロット生産に最適です。それぞれの加工方法を理解し、目的に合わせて適切に選択することが重要です。
2-3. 両加工方法の比較
フライスとマシニングは、製造業において異なる利点を持つ二つの重要な加工方法です。フライス加工は、特に複雑な形状や平面を必要とする部品に適しています。これは、刃が回転しながら工作物に対して横または縦に移動することで材料を削り取る方法です。例えば、自動車のエンジン部品や航空機の部品製造において広く用いられています。一方、マシニング(特にCNCマシニング)は、非常に高い精度と再現性が求められる作業に最適です。コンピュータによる制御下で、工具と工作物の両方が複雑な動きをすることで、微細な部品や複雑な3D形状も精密に加工できます。特に、医療機器や精密機械部品の製造に不可欠です。
結論として、フライス加工は複雑な形状や大きな部品の加工に適しており、マシニングは高精度が求められる小さな部品や複雑な3D形状の加工に適しています。どちらの方法も、それぞれの特定の用途において重要な役割を果たし、製造業における多様なニーズに応えています。
3. 切削加工の基礎知識
3-1. 切削加工とは:種類とプロセス
フライス加工とマシニングセンタ加工は、製造業で広く使用される二つの主要な加工方法です。これらの選択は、製造する製品の精度、量、そしてコストに大きな影響を及ぼします。フライス加工は、回転する工具を用いて材料から部品を削り取る方法で、特に平面や溝などの加工に適しています。一方、マシニングセンタ加工は、CNC(コンピュータ数値制御)技術を活用し、より複雑な形状や精度が求められる部品の製造に優れています。
たとえば、フライス加工は一般的に大量生産に適しており、比較的低コストで部品を製造できることがその最大の利点です。例えば、自動車のエンジン部品や建設機械のコンポーネントなど、大量に生産される部品の加工には、フライス加工がよく使用されます。一方で、マシニングセンタは、高い精度と複雑な形状を実現できるため、航空宇宙産業や医療機器の部品製造など、特定の要件を持つ製品に適しています。
結論として、フライス加工とマシニングセンタ加工はそれぞれ異なる利点を持っています。製品の要求される精度、形状、生産量に応じて適切な加工方法を選択することが重要です。正しい選択によって、製造コストの削減や製品品質の向上につながり、競争力のある製品を市場に提供することができます。
3-2. 加工方法の選択:材料と製品による違い
加工方法の選択においては、フライスとマシニングそれぞれの利点を理解することが重要です。フライス加工は、特に平面や溝を加工するのに適しており、大量生産にも向いています。一方、マシニング加工は、複雑な形状や精密な部品の製造に優れた方法とされています。
例えば、日本の自動車産業では、フライス加工がエンジンの部品やフレームの製造に広く利用されています。これは、フライス加工が大きな部品の効率的な製造を可能にするからです。一方、時計やカメラなどの精密機器においては、マシニング加工がその精度と複雑な形状の製造能力のために好まれます。
結論として、フライス加工とマシニング加工は、それぞれ異なる利点を持っており、製品の要件や材料に応じて適切な加工方法を選択することが重要です。大量生産や単純な形状の製造にはフライス加工、精密な部品や複雑な形状の製造にはマシニング加工が適していると言えます。
3-3. 切削加工のポイント:品質と効率
フライス加工とマシニングセンタの選択は、品質と効率の観点から重要な意思決定です。フライス加工は、平面や曲面などの加工に適しており、特に大量生産において高い効率を発揮します。一方、マシニングセンタはその汎用性により、複雑な形状の加工や精密な作業が可能です。例えば、フライス加工では、一定の形状を持つ部品の生産に適しているが、マシニングセンタは3次元で複雑な形状の部品も高精度で加工できます。このように、フライス加工は量産性に優れ、マシニングセンタは加工の柔軟性と精度が高いという異なる利点があります。結論として、製品の要求仕様や生産量に応じて、フライス加工とマシニングセンタの選択を慎重に行うことが、品質と効率の向上に繋がります。
4. 金属加工の世界
4-1. 金属加工の基本知識
金属加工において、フライス加工とマシニング センター加工は、それぞれ異なる利点を持っています。フライス加工とは、回転する工具を用いて金属材料を削り取る加工方法で、特に大量生産に向いています。これに対し、マシニングセンター加工は、工具の交換が自動で行われ、複雑な形状の加工が可能です。例えば、フライス加工は、平面や溝といった比較的単純な形状の加工に適しており、自動車の部品製造などに広く利用されています。一方、マシニングセンターでは、3次元の複雑な形状や、精密な加工が求められる製品に対応可能で、航空宇宙産業や医療機器の分野で重宝されています。したがって、加工方法の選択は、加工する製品の形状や生産量、精度などの要件によって異なります。総じて、フライス加工は大量生産に向き、マシニングセンター加工は複雑で精密な加工が必要な場合に適していると言えます。
4-2. 金属加工の種類とその応用
フライス加工とマシニングセンターの選択において、それぞれの利点を理解することは非常に重要です。フライス加工は、複雑な形状や大量生産に適しており、特に平面や溝加工、輪郭形状の加工に非常に有効です。一方で、マシニングセンターは、その高い柔軟性と精度で知られており、一つの設備で多様な加工が可能である点が大きな利点です。例えば、日本の自動車部品製造業では、フライス加工を用いてエンジンの部品を大量に生産する一方、マシニングセンターを活用して複雑な形状のプロトタイプや少量生産品を高精度に加工しています。最終的に、加工方法の選択は、加工する部品の形状、量、そして求められる精度によって決定されます。フライス加工とマシニングセンターのそれぞれの利点を理解し、適切な選択をすることが、効率的かつ精密な金属加工の鍵となります。
4-3. 加工方法選択のためのポイント
加工方法の選択において、フライス加工とマシニング加工はそれぞれ異なる利点があります。フライス加工は、特に複雑な形状や大きな部品の加工に適しています。これは、フライス加工機が多様な切削工具を使用して、様々な面を効率良く加工できるためです。例えば、自動車のエンジンブロックや航空機の部品など、精密さと大量生産が求められる場合に特に有効です。
一方、マシニング加工は、高精度で複雑なディテールが必要な小〜中サイズの部品に適しています。マシニングセンターは、回転する工具と移動する作業台を使用して、部品を多角度から加工できるため、非常に細かい部分の加工も可能です。例えば、精密機器の部品や医療器具などがこれに該当します。
結論として、フライス加工は大きくて複雑な部品の効率的な加工に、マシニング加工は小〜中サイズで高精度が求められる部品の加工に適していると言えます。加工する部品のサイズ、形状、精度要求に応じて、最適な加工方法を選択することが重要です。
5. マシニング加工での精密加工
5-1. 精密加工の定義と重要性
精密加工とは、製品や部品を高い精度と仕上がりで加工する技術のことです。この技術は、自動車や航空機、医療機器など、多岐にわたる分野で不可欠です。特に、日本の製造業では、精密加工技術の向上が競争力の源泉となっています。その中でも、フライス加工とマシニングセンターによる加工は、精密加工における二つの主要な方法ですが、それぞれ異なる利点を持っています。
フライス加工は、主に平面や溝、歯車などの加工に適しており、比較的大きな物体の加工にも対応できるという利点があります。例えば、自動車のエンジンブロックや大型の金型など、大きな部品の加工にはフライス加工が欠かせません。一方、マシニングセンターを用いた加工は、その高い自動化と柔軟性により、複雑な形状や細かい部品の加工に適しています。医療機器の部品や精密機器の部品製作など、高精度が求められる場合に特にその能力を発揮します。
このように、フライス加工とマシニングセンターによる加工は、それぞれが異なる場面でその長所を発揮します。製品の要求される精度や形状、大きさに応じて適切な加工方法を選択することが、高品質な製品製造には不可欠です。日本の製造業が世界で競争力を保ち続けるためには、これらの加工技術の選択と適用が鍵となります。
5-2. マシニングによる精密加工の特徴
フライス加工とマシニング加工は、製造業において重要な役割を果たしますが、それぞれに異なる利点があります。フライス加工は、主に平面や曲面などの複雑な形状を持つ部品の加工に適しています。これに対し、マシニング加工は、より高い精度と細部の仕上がりが求められる場合に選ばれます。例えば、精密機械の部品製造や航空宇宙部品の加工などにマシニング加工が用いられることが多いです。これは、マシニング加工が微細な加工を可能にし、加工後の部品の品質を高めるためです。
フライス加工が適しているのは、比較的大きな部品や、特殊な形状を持つ部品の加工です。例として、自動車のエンジンブロックやギアなどの加工にしばしば用いられます。これに対して、マシニング加工は、その高精度な加工能力を生かして小さな電子部品や精密機械の部品の製造に使われます。このように、フライス加工とマシニング加工は、それぞれの特性を活かして様々な分野で利用されています。
結論として、フライス加工とマシニング加工は、それぞれ独自の利点を持ち、製造業において欠かせない技術です。利点を理解し、適切な加工方法を選択することが、製品の品質向上と生産効率の向上につながるでしょう。
5-3. 精密加工の手順と技術
フライスとマシニングは、精密加工の分野で広く用いられる二つの主要な技術です。これらの加工方法は、その利点と用途が異なるため、製品の設計や用途に応じて選択されます。まず、フライス加工は、平面や曲面を削るのに適しており、特に大きな部品や複雑な形状を持つものの加工に優れています。例えば、自動車のエンジンブロックや航空機の部品製造に多く用いられます。一方、マシニングセンタ(CNC加工)は、更に高精度かつ複雑な加工が可能で、小さな部品や精密な製品の製造に適しています。時計の部品や医療機器など、細かい作業が要求される製品に多く利用されています。
これらの加工方法の選択には、製品の仕様、量産性、コストなど様々な要因が考慮されますが、最終的には目的とする製品の品質や機能を最大限に引き出す方法を選ぶことが重要です。結論として、フライス加工とマシニングはそれぞれ独自の利点を持ち、日本の製造業において不可欠な技術であるといえます。適切な選択を通じて、より高品質な製品の製造が可能となります。
6. 金属加工技術の種類と選択
6-1. 金属加工技術の概観
金属加工技術は、製品製造の根幹をなす重要な工程であり、その中でもフライス加工とマシニング加工は、それぞれ異なる利点を持ちます。フライス加工は、主に平面や曲面、溝などの加工に適しており、大量生産に向いています。その理由は、フライス加工機が一度に多くの工具を使用でき、効率良く加工できるからです。例えば、自動車のエンジン部品や航空機の部品製造において、フライス加工は広く利用されています。一方、マシニング加工は、複雑な形状や高い精度を要求される部品に適しています。コンピュータ数値制御(CNC)技術を用いることで、極めて繊細な作業が可能となり、例えば、精密機械や医療機器の部品製造で重宝されています。このように、フライスとマシニング加工は、その利用目的や求められる精度によって適した選択肢が異なりますが、どちらも製品製造において不可欠な技術であることに変わりはありません。したがって、製品の要求仕様を正確に理解し、それぞれの加工方法の利点を活かすことが重要です。
6-2. 各技術の特徴と適用範囲
フライス加工とマシニング加工は、製品製造における重要な技術ですが、それぞれ異なる利点があります。フライス加工は、特に平面や溝、歯車などの加工に適しており、切削能力が高いため、大量生産に向いています。例えば、自動車のエンジン部品や機械のフレームなど、大きなパーツの生産に多く用いられます。一方、マシニング加工は複雑な形状や精密な部品の加工に優れており、3Dモデリングに基づいた加工が可能なため、航空宇宙産業や医療機器など、高い精度が求められる分野で活用されています。
したがって、加工方法を選択する際には、製品の要件や生産量を考慮する必要があります。大量生産が必要であればフライス加工が、複雑さや精度が重視される場合にはマシニング加工が適していると言えます。各技術の特性を理解し、製品の性質に合わせて最適な加工方法を選択することが、効率的で品質の高い製造につながります。
6-3. 適切な技術選択のためのポイント
フライス加工とマシニング加工は、製造業における重要な工程ですが、それぞれ異なる利点があります。選択の決め手となるのは、加工する製品の材質、形状、そして精度要求です。フライス加工は、平面や曲面などの多様な形状を加工できる柔軟性が特徴です。例えば、複雑な形状の金型製作によく用いられます。一方、マシニング加工(CNC旋盤加工を含む)は、高精度が求められる部品製造に適しています。特に、円形や複雑な内径の加工が必要な場合に優れた能力を発揮します。ジェットエンジンの部品製作などがその例です。
したがって、適切な加工方法の選択には、製品の要求される品質と製造効率を総合的に考慮する必要があります。フライス加工の柔軟性とマシニング加工の高精度を理解し、それぞれの利点を生かすことが、製造業における品質とコストのバランスを最適化する鍵となります。
7. 加工方法の選択:フライスとマシニングの異なる利点
7-1. プロジェクトに合わせた加工方法の選択
加工方法を選択する際、フライス加工とマシニング加工の違いを理解することが重要です。フライス加工は、回転する工具を使用して材料から部品を削り取る方法であり、比較的大きな平面や溝を効率よく加工するのに適しています。一方、マシニング加工は、より複雑な形状や細部の精密加工に優れています。たとえば、フライス加工では平面や直線的な形状を、マシニング加工では立体的な形状や狭い部分の加工が可能です。このため、プロジェクトの要件に合わせて最適な加工方法を選択することが、品質向上とコスト削減につながります。最終的に、フライス加工とマシニング加工を適切に選択し組み合わせることで、効率的かつ高品質な製品製造が可能となるでしょう。
7-2. コストと品質のバランスを考える
加工方法を選択する際、フライス加工とマシニングの違いを理解することが重要です。フライス加工は、主に平面や溝、歯車などの加工に適しており、比較的大きな部品の加工に適しています。一方、マシニングは、複雑な形状や細かな部品の加工に優れ、高精度が求められる作業に適しています。
例えば、フライス加工では、大きな金属ブロックから部品を削り出すことができ、効率良く大量生産が可能です。一方、マシニングでは、3D CADデータを基にして、より複雑な形状や細かい部品を正確に加工することができます。
結論として、フライス加工は大量生産や比較的シンプルな部品の加工に適しているのに対し、マシニングは複雑で精密な部品の加工に適しています。そのため、加工する部品の形状や精度、生産量などを考慮して、最適な加工方法を選択することが重要です。
7-3. 加工方法の将来性と進化
加工方法としてのフライスとマシニングは、それぞれに異なる利点を持っています。結論から言えば、適切な加工方法を選択することは、製品の品質、生産性、そしてコスト効率に直接影響を与えます。
フライス加工は、特に平面や曲面などを加工する際に優れた能力を発揮します。具体的な例として、大量生産が必要な部品や、複雑な形状をもつものの加工に適しています。その一方で、マシニング加工は、高い精密度と複雑な内部形状を実現可能な点で優れています。たとえば、航空宇宙産業や医療機器の部品など、極めて精度が求められる製品の加工には適しています。
選択を誤ると、製品の品質不良につながるだけでなく、生産効率の低下やコストの増加を招くことになります。そのため、製品の要件に合わせた適切な加工方法の選択が重要です。
最終的に、フライスとマシニングはそれぞれ異なる利点を持ち合わせています。製品の特性を理解し、それぞれの加工方法の特性を最大限に活用することが、高品質な製品を効率よく生産する鍵となります。
まとめ
フライスとマシニングは金属加工の方法で、それぞれ異なる利点があります。フライスは回転するカッターで金属を削り取る方法であり、マシニングは工具を使用して金属を形成する方法です。フライスは精密な形状を作るのに適しており、マシニングは大量生産に向いています。また、フライスは複雑な加工が可能で、マシニングは素早く加工ができるという利点があります。どちらの方法も、目的や加工する素材によって適切な選択を行うことが重要です。
フライスとマシニングの違いをわかりやすく解説!
「フライス」と「マシニング」、これらの用語を耳にしたことがありますか?では、実際にはどのような違いがあるのでしょうか?今回は、その疑問を解消すべく、丁寧に解説していきます。
工作業界では、フライスとマシニングはよく使われる用語ですが、その具体的な違いを知っている人は少ないかもしれません。なぜなら、両者は似たようなプロセスを行うため、見分けるのが難しいからです。しかし、実際には微妙な違いがあり、その違いを理解することで、作業効率が向上し、品質が向上することもあります。
この記事では、フライスとマシニングの違いについてわかりやすく解説します。どちらも重要な工作プロセスであり、正しい選択をするためにはその違いを把握することが必須です。さあ、フライスとマシニングの謎を解き明かしましょう!
1. フライスとマシニングの基本的な違い
1-1. フライス加工の概要
フライス加工とマシニングの違いを理解することは、製造業において非常に重要です。まず、フライス加工とは、回転する刃を使用して材料を切削し、所望の形状や仕上がりに加工する方法です。その主な特徴は、複雑な形状や平面、溝を効率良く加工できる点にあります。例えば、自動車のエンジン部品や航空機の構造部材など、精密な部品製作に頻繁に用いられます。
一方、マシニングは、フライス加工を含む幅広い加工技術を指し、旋盤加工や研磨加工なども含まれます。マシニングの特徴は、多様な加工技術を利用できるため、様々な材料や製品の加工が可能です。具体的には、プラスチック製の小物から、大きな金属製の部品まで、幅広い範囲にわたります。
結論として、フライス加工は、特定の加工方法を指し、特に複雑な形状の精密加工に適しているのに対して、マシニングはより広い範囲の加工技術を総称し、多様な材料や製品の加工が可能であるという違いがあります。この理解を深めることにより、製造業においてより適切な加工方法を選択し、効率的な生産活動を進めることができます。
1-2. マシニング加工の概要
フライスとマシニングの違いを理解することは、製造業において重要です。簡単に言うと、フライス加工は回転する刃を使用して材料を削る加工方法です。一方で、マシニングはフライス加工を含む広範な加工技術を指し、旋盤加工や研磨などもマシニングの一部と言えます。フライス加工は主に平面や曲面、溝などの加工に用いられるのに対し、マシニングはより複雑な形状や精度が要求される部品製造に欠かせない技術です。たとえば、自動車のエンジン部品や航空機の構造部材など、高度な技術を必要とする製品の加工には、マシニングが用いられます。結論として、フライス加工はマシニングの一部であり、マシニングはより広範囲な加工技術の総称であることがわかります。この理解を深めることで、製造業における加工技術の選択や適用がより効果的になります。
1-3. 加工方法の比較
フライス加工とマシニングセンタの使用は、製造業で頻繁に行われる加工方法ですが、その違いを正確に理解している人は意外と少ないかもしれません。基本的に、両者の主な違いは加工の柔軟性と生産性にあります。
フライス加工は、回転する工具を使用して材料から不要な部分を削り取る加工方法です。この方法は、比較的単純な平面や溝、歯車などの加工に適しています。一方、マシニングセンタとは、フライス加工に加えて、穴あけやタッピングなど複数の加工機能を持つ高度なCNC(コンピュータ数値制御)機械のことを言います。マシニングセンタは、複雑な形状や精度が要求される部品の製造に非常に適しており、一度に多様な加工を実行できるため、生産性が高いという特長があります。
例えば、自動車のエンジン部品や航空機の部品製造では、その複雑性と高い精度要求のため、マシニングセンタが広く利用されています。これに対して、一般的な建設機械の部品や家具の金具など、比較的単純な形状の加工にはフライス加工が適しています。
結論として、フライス加工とマシニングセンタの違いは、加工の柔軟性と生産性にあります。加工する部品の複雑さや生産量に応じて、どちらの加工方法を選択するかが重要です。日本の製造業では、これらの加工技術を駆使して高品質な製品を効率良く生産しているのです。
2. フライス加工とマシニング加工の具体的な違い
2-1. 加工できる材料の種類
フライスとマシニングの違いを理解することは、製造業において重要です。簡単に言うと、フライス加工は回転する刃を使用して材料から部品を作り出す工程であり、マシニングはコンピュータ制御(CNC)によるより精密な加工方法です。フライス加工では、主に平面や曲面を削り取る作業が行われますが、マシニングでは3Dの複雑な形状も精密に加工することが可能です。
たとえば、フライス加工は一般的な部品の製造に用いられ、比較的単純な形状を持つ製品の加工に適しています。一方、マシニングは航空宇宙や自動車業界など、より高度で複雑な精密部品が必要とされる分野で頻繁に利用されます。この差は、フライス加工の機械が主に手動または半自動であるのに対し、マシニングセンターは完全に自動化されており、コンピュータによるプログラムに従って作業を行う点にあります。
結論として、フライス加工とマシニングの主な違いは、加工の精度と複雑さにあります。フライスは単純な形状の部品製造に適しており、マシニングは複雑で精密な部品を求める業界で重宝されています。どちらの加工方法も、その用途と要求される精度に応じて適切に選択することが、製造の効率化と品質向上に繋がります。
2-2. 加工精度と仕上がり
フライス加工とマシニングの違いは、加工方法とその応用範囲にあります。フライス加工は、回転するカッターを使用して材料の表面から所望の形状を削り取る方法です。これに対し、マシニングは、旋盤やマシニングセンターなどの機械を用いて、材料を精密に削り出す加工技術の総称です。フライス加工は平面や溝、歯車などの加工に適しており、特に複雑な形状を持つ部品の製造に有効です。例として、自動車のエンジン部品や航空機の部品製造に多用されています。一方、マシニングにはCNC(コンピュータ数値制御)技術を用いたものがあり、これにより高度な精度と複雑な形状が要求される部品の製造が可能になります。例えば、精密機器の部品や医療機器の部品加工に利用されています。結論として、フライス加工とマシニングは、それぞれ特定の用途に最適化された加工方法であり、製造する製品の形状や精度、材質によって適切な加工方法を選択することが重要です。
2-3. 加工速度と生産性
フライスとマシニングの違いを理解することは、精密な製品製造において非常に重要です。簡単に言えば、フライス加工は回転する工具を用いて材料を削る加工方法です。一方、マシニングは、フライス加工を含む幅広い加工技術の総称であり、旋盤加工や研磨なども含みます。
フライス加工の具体的な例としては、平面や溝を削り出す作業が挙げられます。この方法は、複雑な形状でも比較的簡単に加工できるという利点があります。一方、マシニングは、これらのフライス加工だけでなく、より精密な加工が求められる場合に用いられる技術です。例えば、エンジン部品の製造など、非常に高い精度を要求される製品には、このマシニング技術が不可欠です。
結論として、フライス加工はマシニングの一部であり、マシニングは幅広い加工技術を包含する総称です。フライス加工は特定の加工方法を指すのに対し、マシニングはより広範な概念であり、多くの異なる加工技術を含んでいます。それぞれの技術は特定の製品製造において最適な方法を提供します。
3. NCフライス盤とマシニングセンタの特徴
3-1. NCフライス盤の役割と機能
フライスとマシニングの主な違いを理解することは、製造業において非常に重要です。フライスは、主に金属を削る工程に使用される工作機械の一種で、回転する刃を使って材料から不要な部分を取り除きます。これに対し、マシニングは、フライス加工を含むより広範な加工技術を指し、旋盤やドリルなど他の多様な工作機械を使用して材料を形成します。
例えば、フライス加工では、平面や溝、歯車などの加工が可能ですが、マシニングセンター(CNCマシニングセンターとも呼ばれます)を使用すると、これらに加え、複雑な形状や3D形状の加工も行うことができます。日本の製造業では、精密部品の製造において、このような高度なマシニング技術が求められています。
簡単に言うと、フライスは特定の加工技術を指し、マシニングはそれを含む広範な加工方法を意味します。フライス加工が単一の工程に焦点を当てているのに対し、マシニングはより多角的で高度な加工を可能にします。この違いを理解することで、製造プロセスの効率化や品質の向上につながります。
3-2. マシニングセンタの役割と機能
フライス加工とマシニング加工は、製造業で広く用いられる二つの重要な手法ですが、これらの違いを明確に理解することは非常に重要です。まず結論から申し上げると、フライス加工は主に平面や曲線の加工に用いられる一方で、マシニング加工はより複雑な形状や3次元の加工に適しています。
この違いの理由は、両加工方法の工具の動き方にあります。フライス加工では、工具は主に回転運動をし、加工面に対して直線的に進むことで材料を削り取ります。具体的な例としては、平らな面を作るための面取りや、溝を彫る作業などがあります。
一方、マシニング加工では、工具が多方向に動くことができ、更に複雑な形状を作り出すことが可能です。これは、例えば、空間を複雑に曲がった形状や、精密な穴の加工など、フライス加工では難しい作業を可能にします。
結論として、フライス加工は比較的単純な形状の加工に適しており、マシニング加工はより高度で複雑な形状を必要とする場合に選ばれる加工方法です。それぞれの特性を理解することで、製造プロセスを最適化し、効率的で高品質な製品を作り出すことができます。
3-3. 操作性とプログラミング
フライスとマシニングの違いを理解することは、製造業において非常に重要です。フライス加工は、回転する刃を用いて材料から不要な部分を削り取る加工方法です。これに対して、マシニング加工は、フライス加工を含む広範囲な加工技術を指し、旋盤加工や研削加工なども含まれます。簡単に言えば、フライス加工はマシニング加工の一部と言えるでしょう。
例を挙げると、フライス加工は部品の平面や溝を削るのに適しています。一方で、マシニング加工の範疇には、複雑な形状を持つ部品を製造するための旋盤加工や、非常に滑らかな表面を実現するための研削加工があります。つまり、フライス加工はより特定の用途に対して、マシニング加工はより広範な加工技術の応用に対して用いられます。
結論として、フライス加工とマシニング加工は、加工技術の中で異なる位置づけにありながらも、共に製造業で不可欠な役割を果たしています。各加工技術の特性を理解し、適切な技術を選択することが、製品の品質向上へとつながるでしょう。
4. 金属加工におけるフライスとマシニングの使い分け
4-1. フライス加工が適している場合
フライス加工とマシニングの違いを理解することは、工業製品の製造において非常に重要です。この二つの違いを簡単に言うと、フライス加工は主に平面や曲面を削る作業に適しているのに対し、マシニングはより複雑な形状や細かい部分の加工に適しています。たとえば、フライス加工は機械の部品の溝や平面を削るのに用いられますが、マシニングは3Dの複雑な形状を持つ部品の製作に用いられることが多いです。これは、マシニングが工具の動きが多軸であるため、より多様な形状を実現できるからです。結論として、フライス加工は比較的シンプルな形状の加工に、マシニングは複雑な形状や精密な加工を要する場合に適しています。各々の適切な使用を理解することで、効率的かつ効果的な製造プロセスを実現することができます。
4-2. マシニング加工が適している場合
フライス加工とマシニングの違いを理解することは、製造業において非常に重要です。簡単に言えば、フライス加工は主に平面や曲面を削る作業に適しており、マシニング(特にCNCマシニング)はより複雑な形状の加工に適しています。
フライス加工は、回転する刃を使用して材料から余分な部分を取り除く方法です。これは主に、直線的な溝や平らな表面を作るのに使用されます。例えば、平らな金属板から特定の形状を切り出す場合などが挙げられます。一方、マシニングは、コンピュータ制御により、非常に精密な形状や複雑な3D形状を作り出すことができます。これは、航空宇宙部品や自動車のエンジン部品など、高度に複雑で精密な部品を製造する際に特に重要です。
具体的な例として、フライス加工では、シンプルな金属のフレームや基板の加工が挙げられます。それに対して、マシニングでは、複雑な形状を持つプラスチックのギアや金属製のタービンブレードの製造が可能です。
結論として、フライス加工は比較的シンプルな形状の加工に適しており、マシニングは複雑で精密な加工が必要な場合に適しています。どちらの技術も、製造業において重要な役割を果たしており、使用する目的に応じて適切な加工方法を選択することが重要です。
4-3. 複合加工としての利点
フライスとマシニングの違いを理解することは、精密な製造プロセスを探求する上で極めて重要です。フライス加工は、回転する工具を使用して材料から部品を削り出す方法であり、一方、マシニングは、より広義に機械加工の全プロセスを指します。フライス加工はマシニングの一種であり、特に複雑な形状や表面を削り出すのに適しています。
たとえば、フライス加工機を使用して、歯車やエンジン部品などの精密部品を製造できます。このプロセスでは、多様な工具が使用され、材料の異なる部分を効率よく削除できます。対照的に、一般的なマシニングプロセスでは旋盤加工も含まれ、これは材料を回転させながら固定された切削工具で形を作る方法です。
日本では、製造業の高い技術力と精密加工への需要により、これらの加工技術が非常に重要です。自動車や電子機器の製造など、多くの産業でフライス加工とマシニングの技術が活用されています。
結論として、フライスとマシニングの違いを理解することは、製品の設計から製造まで、より効率的で精密な方法を選択するために重要です。特に、フライス加工はマシニングの中でも特化したプロセスとして位置づけられ、複雑な形状や精密な部品の製造に不可欠です。日本の製造業においても、これらの加工技術の理解と応用が、高品質な製品を生み出す鍵となっています。
5. フライス盤とマシニングセンタの選択基準
5-1. 加工する製品の複雑性
フライスとマシニングの違いを理解することは、製造業界における重要な知識の一つです。フライス加工は、回転する刃を使用して材料から部品を削り取る工程です。これに対し、マシニングは、フライス加工を含むさまざまな加工技術を組み合わせた、より包括的な製造プロセスを指します。例えば、フライス加工機を使用して平面や溝を削ることができますが、マシニングセンタでは、フライス加工に加えて、穴あけやタッピングなど、複数の加工を一台の機械で行うことが可能です。
日本では、精密な製品製造が求められることが多く、マシニングセンタが活躍する場面が多いです。たとえば、自動車や航空機の部品製造では、複雑な形状や高い精度が要求され、これらを効率良く製造するためにマシニングセンタが使用されます。
結論として、フライス加工は特定の加工技術に限定されるのに対して、マシニングは複合加工能力を持つ、より進化した製造プロセスと言えます。日本の製造業界では、製品の複雑性が高まるにつれて、マシニング技術の重要性がさらに増しています。
5-2. 製造コストと投資回収
フライスとマシニングの違いについて、その核心を理解することは、製造業に携わる上で非常に重要です。フライス加工とは、主に平面や曲面などの加工に用いられる方法で、回転する刃が材料を削り取ることで形状を作り出します。一方、マシニング加工は、フライス加工よりも広範囲にわたる加工技術を指し、旋盤加工や研削加工など、様々な種類の加工が含まれます。特に、CNC(コンピュータ数値制御)マシニングは、高精度な加工が可能であり、複雑な形状や微細な部品でも精密に加工することができます。
例えば、フライス加工を使用して平面を削り出す時、主にその平面加工に特化していますが、CNCマシニングを用いることで、3D形状の加工も容易に行えるといった具体例があります。このように、フライス加工はある特定の用途に適しているのに対して、マシニング加工はより多様な加工を可能にします。
したがって、フライスとマシニングの違いは、加工技術の範囲と適用範囲にあると言えます。フライス加工は特定の加工方法に限られるのに対し、マシニング加工はそれを含む幅広い加工技術を指します。この違いを理解することで、製品の設計や加工方法の選定においてより適切な選択が可能となり、製造コストの削減や生産効率の向上に繋がります。
5-3. 機械設備のメンテナンスとアフターサービス
フライスとマシニングの違いを理解することは、精密な加工技術を要する業務において非常に重要です。フライス加工は、主に回転する刃を用いて材料から余分な部分を削り取る加工方法です。これに対し、マシニング加工は、フライス加工を含むより広範な概念で、旋盤加工や研磨加工など、多様な加工技術を総称しています。つまり、フライス加工はマシニング加工の一部ということになります。
たとえば、自動車のエンジン部品を製作する際、フライス加工によって大まかな形状を創出し、その後、精密な寸法を実現するために旋盤加工を行うことがあります。このプロセス全体がマシニング加工に含まれます。
結論として、フライス加工はマシニング加工の一手法に過ぎず、マシニング加工はそれを含めた多様な加工技術の集合体であると言えます。この基本的な違いを理解することは、製造業務において正確な加工技術の選択と適用を行う上で不可欠です。
6. 現代の製造業におけるフライスとマシニングの役割
6-1. インダストリー4.0と加工技術の進化
フライスとマシニングの違いをわかりやすく解説しましょう。これら2つの加工技術は、製造業で広く利用されていますが、それぞれに特徴があります。フライス加工は、回転する工具を使用して材料から部品を削り取る方法です。一方、マシニングとは、主にコンピュータ数値制御(CNC)を用いた加工のことを指し、より複雑で精密な加工が可能です。
たとえば、フライス加工では、平面や溝、歯車などの加工が一般的です。これに対して、マシニングでは、3D形状や非常に複雑な形状も高精度で製作できます。日本の製造業では、特に精密部品の製造において、このような技術の違いが製品の品質を大きく左右します。
フライス加工が単純な形状の加工に適しているのに対し、マシニングは複雑で精密な加工が求められる場合に選ばれる技術です。両者の違いを理解することは、製品設計や製造プロセスの選定において非常に重要です。結論として、フライスとマシニングはそれぞれ異なる特徴と適用範囲を持つ加工技術であり、製造業における適切な選択が求められます。
6-2. カスタマイズと小ロット生産への対応
フライスとマシニングの違いは、製造業において理解すべき重要なポイントです。フライス加工は、回転する刃を使用して材料を削り取る方法です。これに対して、マシニングとは、フライス加工を含む広範な加工技術を指し、旋盤加工や研削加工など、さまざまな方法が含まれます。つまり、フライスはマシニングの一部であると言えます。例えば、小さな部品の精密加工では、フライス加工が適している場合が多いです。一方、大きな部品や複雑な形状を加工する場合には、フライス加工以外のマシニング技術が選ばれることがあります。この違いを理解することは、製品の設計やコスト計算、さらには加工技術の選択において非常に重要です。まとめると、フライスは特定の加工法を指し、マシニングはそれを含む広範囲な加工技術全体を指します。適切な技術の選択は、製造の効率性や製品の品質に大きく影響します。
6-3. 環境への影響と持続可能な製造プロセス
フライスとマシニングの違いを理解することは、製造業での精密な加工技術を理解するうえで重要です。フライス加工は、回転するカッターを使用して材料の表面から削り取る方法であり、特に平面や溝を加工するのに適しています。一方、マシニングは、ドリルや旋盤など様々な切削工具を用いて、材料を加工する広範囲な技術を指します。フライス加工はマシニングの一種であり、その具体例として捉えることができます。
たとえば、自動車のエンジン部品の加工において、フライス加工はエンジンブロックの平面や溝を削り出すのに使用されます。これに対して、マシニングはエンジンのシリンダー穴を加工するために用いられるドリル加工など、より広い範囲の加工を指します。
結論として、フライスとマシニングの主な違いは、フライスが特定の加工技術を指すのに対して、マシニングは幅広い加工技術全般を含む用語であるという点です。それぞれの技術は製造業において特定の用途に適した方法であり、加工する製品の種類や必要な精度に応じて適切な技術が選択されます。
まとめ
フライスとマシニングの違いについて、フライスは工具を回転させながら切削する加工方法であり、マシニングは工具を移動させながら切削する加工方法です。フライスは旋盤よりも広い範囲の切削が可能で、複雑な形状を加工することができます。一方、マシニングは工具の移動によって加工を行うため、比較的直線的な形状を加工するのに適しています。両者の違いを理解することで、加工方法を適切に選択することができます。
フライス加工とマシニングセンタの違いを徹底解説!
フライス加工とマシニングセンタ、どちらも製造業において重要な役割を果たしていますが、その違いを正しく理解していますか?今回は、両者の違いに焦点を当て、徹底的に解説していきます。製造業に携わる方であれば、この情報を知ることで業務の効率化や品質向上につなげることができるかもしれません。さあ、フライス加工とマシニングセンタの違いについて掘り下げてみましょう。
1. フライス加工とは
1-1. フライス加工の基本
フライス加工とマシニングセンタの違いは、その機能と用途に大きく関わっています。フライス加工は、主に平面や曲面を削るために使用される工作機械です。これに対して、マシニングセンタはフライス加工機能を含む多機能な工作機械であり、穴あけやタッピングなど、さまざまな加工が一台で可能です。例えば、フライス加工機であれば、主に平面を削る作業に特化していますが、マシニングセンタを使用すると、その作業の他に、複数の工具を自動で交換しながら、複雑な形状の加工や精密な穴開け作業も行えます。このように、マシニングセンタはフライス加工を含む様々な加工が可能で、生産効率を大きく向上させることができます。結論として、フライス加工は特定の加工に特化しているのに対し、マシニングセンタは複数の加工を一台でこなせる多機能性が特徴です。それぞれの適用範囲や目的に応じて選択することが大切です。
1-2. フライス加工の用途とメリット
フライス加工とマシニングセンタの違いは主にその用途と機能性にあります。フライス加工は、主に平面や溝、歯車などの加工に用いられる工作機械です。この方法の利点は、複雑な形状でも柔軟に対応でき、比較的短時間で正確な加工が可能である点です。例えば、自動車のエンジン部品や精密機械の部品製造に広く応用されています。
一方、マシニングセンタはフライス加工を基本としつつ、穴あけやタッピングなど、さまざまな加工が一台で行える高度な工作機械です。この機械の最大の特徴は、多軸制御が可能であり、複雑な形状の加工も一度のセットアップで行える効率性にあります。このため、航空宇宙産業や医療機器といった分野で特に重宝されています。
結論として、フライス加工とマシニングセンタの主な違いは、その用途の広がりと加工の効率性にあります。フライス加工は比較的単純な形状の加工に適しており、マシニングセンタは複雑で精密な作業を効率良く行う必要がある場合に最適です。どちらの技術も、製造業の発展にとって不可欠な要素であり、適切な選択が求められます。
1-3. フライス加工が適している材料
フライス加工とマシニングセンタの違いを理解することは、製造業における重要な知識の一つです。まず、フライス加工は、回転するカッターを使用して材料から不要な部分を取り除く加工方法です。この方法は、比較的単純な形状や平面、溝を加工するのに適しています。一方、マシニングセンタは、フライス加工を含む多様な加工が一台でできる高度な機械です。この機械は、自動で工具を交換する機能を持ち、複雑な形状や3次元加工を効率的に行うことが可能です。
例えば、フライス加工では、平面や直線の加工が主に行われますが、マシニングセンタを使用すると、曲面加工や穴あけ、タッピングなど、より複雑な加工が可能になります。また、マシニングセンタはCNC(コンピュータ数値制御)により操作されることが多く、高い精度と再現性を持って多様な加工を自動でこなすことができます。
結論として、フライス加工は単純な形状の加工に適しており、マシニングセンタはそれを含む多様な加工を一台でこなすことができる、より進化した加工方法と言えます。用途に応じて適切な加工方法を選ぶことが、製造効率の向上につながります。
2. マシニングセンタの概要
2-1. マシニングセンタの基本構造
フライス加工とマシニングセンタの違いは主にその機能性と用途にあります。フライス加工は、切削工具が回転することで、金属などの材料から不要な部分を削り取る加工方法です。一方、マシニングセンタはフライス加工を含む多様な加工が一台で行える高度なCNC(数値制御)機械です。
具体例として、フライス加工機は単一の加工作業に特化しているのに対し、マシニングセンタは複数の工具を自動で交換しながら、フライス加工、穴あけ、タッピングなど複数の加工を一度に行えます。この柔軟性によりマシニングセンタは、複雑な形状の製品や精密な部品の製造に適しています。
また、マシニングセンタは生産性が高く、加工精度も非常に高いため、航空宇宙産業や自動車産業など、厳しい品質基準が求められる分野で特に重宝されています。フライス加工機に比べ、初期投資は高くなりますが、長期的に見ると高い生産効率と精度により、コストパフォーマンスは非常に良いと言えます。
結論として、フライス加工とマシニングセンタの主な違いは、その機能性と用途の広さにあります。単純な作業を大量にこなすならフライス加工機が、複雑かつ精密な部品の製造にはマシニングセンタが適しています。それぞれの特徴を理解し、目的に応じた機械選びが重要です。
2-2. マシニングセンタの機能と利点
フライス加工とマシニングセンタの違いを理解することは、製造業での効率的な生産において非常に重要です。フライス加工は、回転する工具を使用して被削材から材料を削り取る加工方法です。一方、マシニングセンタはフライス加工を含む複数の加工機能を備えた高度な機械で、自動工具交換や位置決めなどの機能を持っています。
たとえば、フライス加工では一つの加工が完了するたびに人の手で工具を交換しなければなりませんが、マシニングセンタではプログラムによって自動で工具交換が行われます。これは生産効率を大幅に向上させる点であり、複雑な形状や精密な部品製造においてマシニングセンタの優れた能力を示しています。
また、マシニングセンタは多軸加工が可能で、加工する面を変えるために被削材を手動で位置決めする必要がありません。これにより、一度の設定で複数の面を加工でき、作業時間の短縮と精度の向上が図れます。例えば、航空宇宙産業で使用される複雑な部品は、この高度な機能によって高い精度で製造されています。
結論として、フライス加工とマシニングセンタは、それぞれ特定の用途に適した利点を持っています。フライス加工は単純な形状の加工に適している一方で、マシニングセンタは複雑で精密な加工を効率良く実行するために開発された機械です。製造業においては、これらの違いを理解し、目的に応じて最適な加工方法を選択することが重要です。
2-3. マシニングセンタの種類と特性
フライス加工とマシニングセンタの違いを理解することは、精密な加工を必要とする現代の製造業において重要です。フライス加工は、回転する刃を使って材料から部品を削り出す加工方法です。これに対し、マシニングセンタはフライス加工はもちろん、穴あけやねじ切りなど、より多岐にわたる加工が一台で可能な高度な機械です。例えば、自動車の部品製造において、フライス加工では一つの部品を形成するだけですが、マシニングセンタを用いると、その部品に必要な複数の加工を組み合わせて一度に行うことができます。これにより、生産効率が大幅に向上します。したがって、マシニングセンタはフライス加工よりも柔軟で高機能なのです。結論として、フライス加工とマシニングセンタの主な違いは、加工の範囲と可能性にあり、後者は現代の製造業における多様なニーズに応えるための解決策を提供しています。
3. NCフライス盤の紹介
3-1. NCフライス盤の仕組み
フライス加工とマシニングセンタには、重要な違いがあります。まず結論から言うと、フライス加工は主に平面や曲面などの加工に用いられるのに対し、マシニングセンタはそれに加えて、穴あけやタッピングなど複雑な加工が一台で行える点が大きな違いです。
フライス加工は、刃の回転運動と被加工物の直線運動を組み合わせて材料を削り取る加工方法です。主に、平面加工、溝加工、歯車加工などがあります。一方、マシニングセンタは、フライス加工の機能に加えて、穴あけやねじ切りなどの加工も可能です。これは、工具を自動的に交換する機能を備えているため、一つの機械で多様な加工が行えるためです。
たとえば、ある部品が平面加工と穴あけ加工の両方が必要な場合、フライス盤を使うと、まずフライス加工で形状を作り、次にドリル盤で穴を開ける必要があります。しかし、マシニングセンタを使用すれば、この二つの工程を機械を変えることなく、効率良く行うことが可能です。
結論として、フライス加工は比較的単純な加工に対して使われることが多く、マシニングセンタは複雑な加工や多様な加工が一台で可能な点で、大きく異なります。それぞれの特性を理解し、適切な加工方法を選択することが大切です。
3-2. NCフライス盤の適用範囲
フライス加工とマシニングセンタの違いについて深く理解することは、製造業における効率と品質の向上に直結します。フライス加工とは、固定された材料に対して回転するカッターを用いて形状を削り出す加工方法です。一方、マシニングセンタは、フライス加工を含む多様な加工が一台で行える高度な装置を指します。たとえば、フライス加工は、主に平面や溝を削るのに使用されますが、マシニングセンタでは、それに加えて穴あけやタッピングなども自動で行えます。
日本における製造業では、小ロット多品種の生産が増えており、その柔軟性と高効率を追求するために、マシニングセンタの需要が高まっています。例えば、自動車部品の製造では、多種多様な形状の部品が必要とされ、マシニングセンタを使用することで、複数の加工工程を一台でこなすことが可能になります。
結論として、フライス加工は特定の加工に特化しているのに対し、マシニングセンタは複数の加工が一台で可能で、高い柔軟性と効率性を製造業に提供します。その違いを理解し、適切に活用することが、今日の製造業界における競争力の源泉となるでしょう。
3-3. NCフライス盤の操作方法
フライス加工とマシニングセンタの違いについて解説します。一見すると似ている二つの加工方法ですが、利用方法や機能に大きな違いがあります。フライス加工は、回転する工具を使用して材料の表面を削り取る加工方法です。一方、マシニングセンタは、フライス加工を含む多様な加工が一台で行える高度な装置です。
例えば、フライス加工機能だけでなく、穴あけやタッピングなども可能なマシニングセンタは、設計の複雑な部品や精密な加工が必要な場合に特に有効です。日本では、自動車や電子機器などの製造業でこの二つの加工技術が広く使われています。フライス加工機は比較的単純な部品の加工や大量生産に適しているのに対し、マシニングセンタは複雑な形状や精密加工が求められる製品の加工に向いています。
結論として、フライス加工とマシニングセンタの主な違いは、加工できる範囲と複雑性にあります。マシニングセンタはフライス加工以上の多様な機能を提供し、より高度な製品製造に対応できる点が大きな特徴です。それぞれの特性を理解し、製品の要求に合わせた適切な加工方法を選択することが、効率的で高品質な製品製造の鍵となります。
4. 旋盤との違い
4-1. 旋盤の基本と特徴
フライス加工とマシニングセンタの違いを理解することは、精密加工の世界では非常に重要です。フライス加工は、切削工具が回転する一方で、ワーク(加工する材料)が固定されている加工方法です。これに対して、マシニングセンタはフライス加工機能に加え、ボーリング(穴あけ)やタッピング(ねじ切り)など多様な加工が一台で行える高度な装置です。例をあげると、自動車のエンジン部品や航空機の部品制作など、複雑で精度が求められる部品加工にマシニングセンタが用いられます。フライス加工機は比較的単純な形状の部品の加工に適しています。つまり、マシニングセンタはフライス加工機能を含む多機能な機械であり、より複雑で精密な加工を可能にします。この違いを理解することは、加工の効率化やコスト削減、さらには製品の品質向上に直結します。
4-2. フライス加工と旋盤加工の比較
フライス加工とマシニングセンタの違いは、製造業での加工技術の進歩を象徴しています。簡単に言うと、フライス加工は材料を固定し、回転するカッターで材料を削る加工方法です。一方、マシニングセンタはフライス加工を含む多様な加工が一台で行える高度な装置です。例えば、フライス加工では平面や溝を削り出すことができますが、マシニングセンタではそれに加えて、穴あけやタッピング(ねじ切り)なども可能です。これは、マシニングセンタが複数の工具を自動で交換できるため、一連の加工を効率的に行えるからです。日本では、特に精密部品の製造において、このような高度な加工技術が求められており、マシニングセンタの利用が増えています。結論として、フライス加工とマシニングセンタの最大の違いは、加工の多様性と効率性にあり、後者がより複雑で高度な製造ニーズに応える設備であることがわかります。
5. フライスとマシニングの違いは何ですか?
5-1. フライス加工とマシニング加工のプロセス比較
フライス加工とマシニングセンタの違いを理解することは、製造業において非常に重要です。フライス加工は、回転する刃を使用して材料から部品を削り取る加工方法です。これは、平面や曲面を作成するのに適しています。一方、マシニングセンタは、フライス加工を含む複数の加工機能を備えた高度な機械で、自動工具交換機能や、複数の軸での動きができる点が特徴です。これにより、マシニングセンタは、より複雑な形状や、精度が要求される部品の製造に適しています。
たとえば、フライス加工機を使用して、単純な平面や溝を加工することができますが、複雑な3D形状の部品を製造する場合や、加工工程を減らしたい場合には、マシニングセンタの使用が望ましいです。マシニングセンタは、その高い柔軟性と精度により、航空宇宙や自動車などの産業で重宝されています。
結論として、フライス加工とマシニングセンタはどちらも重要な製造技術ですが、用途によって最適な選択が異なります。フライス加工は比較的単純な部品の製造に、マシニングセンタは複雑で精度が求められる部品の製造に適しています。これらの違いを理解し、適切な加工方法を選択することが、効率的で品質の高い製品を生み出す鍵です。
5-2. フライス加工とマシニング加工の精度と仕上がり
フライス加工とマシニングセンタの違いは、加工精度と仕上がり面の質において顕著です。フライス加工は、回転する切削工具を用いて材料を削り取る方法であり、特に大量生産に適しています。これに対し、マシニングセンタは、コンピュータ数値制御(CNC)を使用して、より複雑で精密な形状を加工することが可能です。例えば、航空宇宙部品や精密機械部品の製造において、マシニングセンタはその高い精度と複雑な形状の実現能力で重宝されています。フライス加工では、シンプルな形状の加工は得意ですが、マシニングセンタほどの細かい精度や複雑な3D形状の加工は得意ではありません。結論として、フライス加工は大量生産に適した加工方法であり、マシニングセンタは高精度・複雑形状の加工を要求される場合に適しています。各々の適切な用途を理解することで、製造工程の効率化と品質向上が期待できます。
5-3. コストと生産性の観点から見た違い
フライス加工とマシニングセンタの違いを理解することは、製造業での効率と生産性を高める上で非常に重要です。フライス加工は、主に平面や曲面を削り出すために使用される加工方法です。一方、マシニングセンタはフライス加工に加え、穴あけやタッピングなどの多様な加工を一台で行える高度な設備を指します。
例えば、日本の自動車産業では、部品の精密加工にフライス加工が用いられますが、複雑な形状や多様な加工が必要な場合にはマシニングセンタが選ばれることが多いです。これは、マシニングセンタの方が加工の自由度が高く、生産効率も向上するためです。
このように、フライス加工とマシニングセンタは、それぞれに適した用途があります。フライス加工は比較的シンプルな加工に適しており、コストが低い反面、マシニングセンタは複数の加工を一台でこなすことができ、生産性を大幅に向上させることができますが、設備投資が大きくなるという特徴があります。したがって、製品の要件や生産量に応じて、適切な加工方法を選択することが重要です。
6. マシニング加工の種類と特徴
6-1. 精密マシニングとは
フライス加工とマシニングセンタの違いを理解することは、製造業での効率的な生産に不可欠です。フライス加工は、回転する刃を用いて材料から部品を削り取る加工方法です。一方、マシニングセンタは、フライス加工に加え、穴あけやタッピングといった複数の加工を一台で行える高度な機械です。
フライス加工の例として、平面や溝を削る作業が挙げられます。これに対して、マシニングセンタは、その機能性から複雑な形状の加工や精密な部品製造に適しています。例えば、自動車のエンジン部品や航空機の部品製造など、複雑な形状や高い精度が求められる製品の加工に多く用いられます。
このように、フライス加工とマシニングセンタは、それぞれ異なる特長を持っています。フライス加工は比較的単純な加工に適し、マシニングセンタは複合的な加工が可能で、高い精度と効率を求める場合に選ばれます。適切な加工方法を選ぶことで、製造業の生産性と品質が向上します。
6-2. 5軸マシニングセンタの利点
フライス加工とマシニングセンタの違いを理解することは、製造業に携わる多くの人にとって非常に重要です。フライス加工は、主に平面や溝を削るために使用される工作機械です。これに対し、マシニングセンタは、フライス加工機能に加え、穴あけやタッピングなど多様な加工が一台で行える高度な設備です。例えば、自動車業界では、複雑な形状の部品を効率よく製造するためにマシニングセンタが広く利用されています。この設備は、一定のプログラムに従って自動的に工具を交換し、多角的な加工を一貫して実施できるため、作業の精度が高く、生産性も向上します。フライス加工は特定の加工に特化している一方で、マシニングセンタはその柔軟性と高機能性が大きな違いと言えるでしょう。このように、フライス加工とマシニングセンタは、それぞれの用途に応じた特性を持ち、製造現場において重要な役割を果たしています。
6-3. 多軸マシニングの可能性
フライス加工とマシニングセンタの違いについて詳しく解説します。これらは、製造業において非常に重要な加工技術ですが、その機能と適用範囲には大きな違いがあります。フライス加工は、主に平面や曲面などを削るために使用され、回転する刃を持つフライス盤によって材料を加工します。この方法は、比較的単純な形状の加工に適しています。
一方、マシニングセンタはフライス加工の機能を含む上で、穴あけやタッピングなど、さまざまな加工が一台で行える高度なCNC(コンピュータ数値制御)機械です。多軸の制御が可能で、複雑な形状や精密な部品の製造に適しています。たとえば、自動車のエンジン部品や航空宇宙関連の精密部品加工などに用いられています。
結論として、フライス加工は単純な形状の加工に、マシニングセンタは複雑で精密な加工にそれぞれ向いています。そのため、製造する製品の複雑さや加工の必要性に応じて、適切な加工技術が選択されるべきです。日本の製造業では、これらの技術を駆使して、世界トップクラスの製品が生産されています。
7. NCフライス盤とマシニングセンタの違い
7-1. 機能と性能の比較
フライス加工とマシニングセンタの違いは、主にその機能と性能にあります。フライス加工は、回転する刃を用いて材料を削り取る加工方法です。一方、マシニングセンタはフライス加工の機能に加え、穴あけやタッピングといった様々な加工が一台でできる高度な設備です。例えば、フライス加工だけでは、複数の加工プロセスを必要とする製品を製造する際に、加工機を変える必要がありますが、マシニングセンタではその必要がありません。これにより、製造工程が簡略化され、生産効率が向上します。このように、フライス加工とマシニングセンタは、それぞれが持つ特性を生かした加工方法であり、製品の複雑さや生産量に応じて適切に選択されるべきです。結論として、フライス加工は単一の加工に対応しているのに対し、マシニングセンタは複合的な加工が可能で効率性が高いという大きな違いがあります。
7-2. 制御システムの違い
フライス加工とマシニングセンタの違いを理解することは、高度な加工技術を要する日本において非常に重要です。これら二つの加工方法の主な違いは、機能の多様性と加工の効率性にあります。フライス加工は、主に平面や溝を削るために用いられ、比較的単純な作業に適しています。一方、マシニングセンタは、フライス加工の機能に加え、穴あけやねじ切りなど複数の加工を一台でこなせるため、より複雑な形状の加工が可能です。
例えば、自動車部品や航空機部品の製造において、精密な加工が求められる場合、マシニングセンタが選ばれることが多いです。この理由は、マシニングセンタが複数の工具を自動で交換しながら加工を行えるため、加工の精度を保ちつつ、生産効率を大幅に向上させることができるからです。
結論として、フライス加工は比較的単純な加工に適しており、マシニングセンタは複雑で精密な加工を効率よく行うのに適しています。日本の製造業における競争力を維持していく上で、これらの加工技術の違いを理解し、適切な機械を選択することが非常に重要です。
7-3. 適用される加工範囲の違い
フライス加工とマシニングセンタは、製造業で頻繁に使用される機械加工技術ですが、両者には明確な違いがあります。この違いを理解することは、より効率的な生産プロセスを実現するために重要です。
まず、フライス加工は、主に平面や曲面などを削るために使用される加工方法です。これに対して、マシニングセンタは、フライス加工機能に加え、穴あけやタッピングなど、さまざまな加工が一台でできる高度な機械です。
例えば、フライス加工では、刃が回転することによって材料を削り取ることが主な使い道ですが、マシニングセンタでは、プログラムに沿って自動的に工具を交換し、複数の加工を連続して行うことができます。これにより、マシニングセンタは複雑な形状の部品や、精度が要求される部品の加工に適しています。
結論として、フライス加工とマシニングセンタの最大の違いは、加工の自動化と多様性にあります。フライス加工が単一の加工に特化しているのに対し、マシニングセンタは多機能であり、複雑な加工を効率的に行うことが可能です。製造プロセスの効率化と高度化を図るには、これらの違いを理解し、適切な機械選択が重要となります。
8. 加工情報:NCフライスとマシニングの違い – 株式会社 遠藤
8-1. 株式会社 遠藤による技術紹介
フライス加工とマシニングセンタの違いについて、その基本を解説します。フライス加工とは、切削工具が回転することによって、被削材から材料を削り取る加工技術の一つです。一方、マシニングセンタは、フライス加工を含む多様な加工が一台で行える高度な機械を指します。つまり、マシニングセンタはフライス加工の機能を持ちながら、穴あけやタッピングなど、さらに多くの加工を可能にします。
たとえば、フライス加工機では、主に平面や曲面を削る作業に特化していますが、マシニングセンタでは、その機能に加えて、複雑な形状や精密な部品の加工も行えるのです。これは、マシニングセンタがコンピュータ数値制御(CNC)によって運用されるため、非常に高い精度で、複雑な加工が可能となるからです。
例えば、自動車のエンジン部品や航空機の部品製造において、マシニングセンタは不可欠な存在です。これらの部品は、単に形状を削り出すだけでなく、細部にわたる精密さが求められるため、マシニングセンタの精度と多機能性が強みとなります。
結論として、フライス加工は特定の加工に特化した技術であり、マシニングセンタはフライス加工を含む多種多様な加工が一台で行える、より進化した形の機械であると言えます。これにより、製造業における効率と精度の向上が図られています。
8-2. NCフライス盤とマシニングセンタの技術比較
フライス加工とマシニングセンタの違いを深く理解することは、製造業における効率と生産性の向上に不可欠です。フライス加工とは、回転する工具を用いて材料を削り取る加工方法で、特に平面や溝などの加工に適しています。一方、マシニングセンタはフライス加工を含む多くの機能を備えた高度な機械で、自動工具交換システムや多軸制御を通じて、より複雑な形状の加工が可能です。
たとえば、日本の自動車産業では、マシニングセンタを用いてエンジン部品やシャシーなどの複雑な部品を高精度で製造しています。このように、マシニングセンタは複数の工程を一つの機械で行えるため、生産効率が大きく向上します。
しかし、フライス加工は特定の加工においてはそのシンプルさから選ばれることもあります。例えば、大量生産ではなく、単品や小ロットの製品を加工する場合や、加工する材料によっては、フライス加工の方が適している場合があります。
結論として、フライス加工とマシニングセンタはそれぞれ異なる特徴を持ち、用途に応じて選択することが重要です。複雑な形状の加工や効率的な生産が求められる場合はマシニングセンタ、特定の加工において簡便さを求める場合はフライス加工が適しています。どちらの技術も日本の製造業において重要な役割を担っており、その違いを理解することは製品の品質向上と生産効率の向上に直結します。
8-3. 選択基準と企業の判断ポイント
フライス加工とマシニングセンタの違いを理解することは、製造業において非常に重要です。簡単に言えば、フライス加工は主に平面や溝、歯車などの加工に用いられる技術であり、マシニングセンタはそれに加えて、穴あけやタッピングなど多様な加工が一台で可能な高度な機械です。例えば、フライス加工機は主軸が回転する刃で材料を削り取りますが、マシニングセンタはその機能に加え、自動工具交換機能を持ち、プログラムに従って複数の加工を自動で実行できます。このように、マシニングセンタはフライス加工機に比べて加工の幅が広く、高効率で複雑な部品も加工できるため、生産性を大きく向上させることができます。しかし、その分、設備投資や運用コストが高くなるというデメリットもあります。結論として、フライス加工とマシニングセンタの選択は、加工したい製品の複雑さや生産量、コストの観点から検討する必要があり、それぞれの特性を理解することが重要です。
まとめ
フライス加工とマシニングセンタの違いについて、注目すべき点を解説します。
フライス加工は、工具を回転させながら材料を削り出す加工です。一方、マシニングセンタは、複数の切削加工を自動で行う装置です。両者の最大の違いは、自動化レベルにあります。フライス加工は、作業者が材料を手動で動かすため、人の技量に依存します。一方、マシニングセンタは、プログラムに基づいて自動的に作業を行うため、高い精度と生産性が得られます。
また、フライス加工とマシニングセンタのどちらを選択するかは、加工の複雑さや精度、生産性などの要件によって異なります。そのため、具体的な用途に合わせて適切な方法を選択することが重要です。
フライス加工とは何か?マシニングとの違いを専門家が解説
フライス加工とマシニングは、工業分野において重要な役割を果たすプロセスですが、その違いを理解することは容易ではありません。本記事では、専門家がこのテーマについて詳しく解説します。あなたは、フライス加工とマシニングの違いについて疑問を抱いていませんか?それぞれのプロセスの本質や特徴、利用される分野などについて、わかりやすく説明します。工業界におけるこれらの重要な概念を深く理解することで、製造プロセスにおける効率性や品質向上に貢献できるかもしれません。さあ、フライス加工とマシニングについての知識を深めてみましょう。
1. フライス加工とは
1-1. フライス加工の概要
フライス加工とは、工作機械を用いて材料の表面を削る加工方法の一種であり、精密な形状や平面を作り出すことが可能です。これに対し、マシニングはフライス加工を含む広範な加工技術全般を指し、旋盤加工や研削加工なども含まれます。その違いを理解することは、製造業において重要です。
具体例として、フライス加工ではカッターが回転しながら進むことで材料から削り取り、平面や溝、歯車などの加工が行えます。一方、マシニングの中に含まれる旋盤加工では、材料自体を回転させることで形状を削り出します。このようにフライス加工はマシニングの一部分であり、加工方法によって名前が異なるのです。
結論として、フライス加工はマシニングにおける特定の技術の一つであり、材料の表面を精密に削り出すのに適しています。マシニングはそれよりも広い概念で、様々な加工技術を包含しています。この違いを踏まえることで、適切な加工方法を選択し、効率的な製造が可能になります。
1-2. フライス加工の歴史と発展
フライス加工は、金属や樹脂などの材料を削り取る加工方法の一つであり、精密な部品製造に欠かせない技術です。マシニングと比較した場合、フライス加工は回転する刃を用いて材料の表面を削り取る点が特徴で、一方のマシニングは、ドリルや旋盤といった様々な工具を使用して材料を加工する広範囲の技術を指します。具体的には、フライス加工では平面や溝、歯車などの複雑な形状を作り出すことが可能で、例えば自動車のエンジン部品や航空機の構造部材など、日常生活で使われる多くの製品にフライス加工が用いられています。これに対し、マシニングは一般的により大きな範囲の材料加工法を指すため、フライス加工を含む多様な加工技術がマシニングの一部として位置付けられます。結論として、フライス加工はマシニングの一手法であり、その特定の技術を指し、複雑な形状の精密加工に特化していると言えます。
1-3. フライス加工の基本的なプロセス
フライス加工とは、旋盤加工と並んでよく利用される金属加工技術の一つであり、回転する刃を用いて材料から不要な部分を削り取る方法です。マシニングとの違いは、主に加工の精度と用途にあります。フライス加工は、比較的大きな平面や複雑な形状を持つ部品の加工に適しており、大量生産にも向いています。例えば、自動車のエンジン部品や航空機の構造材など、精密さと耐久性が求められる製品の製造に不可欠です。
一方、マシニングセンタと呼ばれる装置を使用するマシニングは、フライス加工よりもさらに高い精度を実現できます。これは、回転速度や工具の種類を細かく制御できるため、非常に複雑な形状や微細な加工が可能となります。したがって、高度な技術を要する電子部品や医療器具など、サイズが小さく、精密な加工が求められる製品に多用されています。
結論として、フライス加工とマシニングは、その適用範囲と目的によって使い分けられます。フライス加工は大規模で耐久性のある部品の製造に適しているのに対し、マシニングは高精度で複雑な形状の製品を必要とする場合に選ばれます。どちらの技術も、現代の製造業において欠かせないものであり、それぞれの特長を活かした加工が求められています。
2. フライスとマシニングの違い
2-1. フライス加工の特徴
フライス加工とは、工具の回転運動と被削材の直線または曲線の送り運動を用いて、素材から所望の形状を削り取る加工方法です。これは、精密な部品製造において欠かせない技術の一つであり、自動車や航空機の部品、金型など幅広い分野で利用されています。フライス加工とマシニング(CNC加工)の主な違いは、加工の制御方法にあります。マシニングは、コンピュータによる数値制御(CNC)で自動化されているのに対し、フライス加工は操作者の技術に大きく依存する場合が多いです。
例えば、複雑な形状の金型を作成する際、フライス加工では経験豊富な技術者が微細な調整を行いながら加工を進めます。一方、マシニングでは、3D CADデータをもとに機械が自動で加工を行うため、高い精度と効率が実現可能です。しかし、フライス加工は、小ロットや特殊な形状の加工においてその柔軟性と経済性で優れています。
結論として、フライス加工は手作業による技術の結晶であり、マシニングは高度な技術による自動化の代表例です。両者は製造現場において互いに補完的な役割を果たし、高品質な製品製造に不可欠です。
2-2. マシニングとの技術的差異
フライス加工とマシニングの違いは、その加工方法と応用範囲にあります。フライス加工は、回転する刃を使用して材料から余分な部分を削り取る加工技術です。一方、マシニングは、フライス加工を含む広範囲の加工技術を指し、旋盤加工や研磨加工など、材料を形成するための様々な方法を含みます。例えば、フライス加工は複雑な形状の部品や溝を作るのに適しており、自動車のエンジン部品や航空機の部品製造に多用されています。これに対し、マシニングはこれらのフライス加工だけでなく、円筒形の部品を作る旋盤加工や表面を滑らかにする研磨加工など、より広い範囲の加工技術をカバーしています。つまり、フライス加工はマシニングの一部であり、マシニングはより広範囲の加工技術を指す用語ということができます。この理解を深めることで、製造業における各加工技術の適切な選択と応用が可能になります。
2-3. 適用範囲と効率性の比較
フライス加工とマシニングの違いを理解することは、精密な部品製造において非常に重要です。まず、フライス加工は回転する刃を使用して材料から部品を削り出す加工方法です。これに対し、マシニングは広義には機械加工の一種であり、フライス加工を含む様々な加工技術を指します。
フライス加工の特徴としては、複雑な形状や平面、溝などを加工できる汎用性の高さが挙げられます。例えば、自動車のエンジン部品や航空機の構造部品の製造に多用されています。これに対して、マシニングはCNC(コンピュータ数値制御)技術を用いた加工を含むため、より高精度な加工が可能です。CNCマシニングでは、プログラムされた指示に従って自動で部品を加工するため、複雑な形状でも極めて高い精度で製造することが可能です。
結論として、フライス加工はその汎用性と柔軟性から広範囲の用途に利用される一方で、CNCマシニングを含むマシニングは高精度かつ複雑な加工が求められる場合に適しています。どちらの技術もその特性を理解し、適切な用途に応じて選択することが、効率的で高品質な部品製造への鍵となります。
3. フライス加工の専門用語
3-1. 切削工具に関する用語
フライス加工は、金属やプラスチックを削る加工方法の一つとして広く使用されています。この技術は、回転するフライスと呼ばれる刃を用いて、材料から不要な部分を削り取ることにより、製品の形状を作り出します。一方、マシニングは、フライス加工を含む広範な加工技術を指し、旋削や研磨など他の加工方法も含まれます。つまり、フライス加工はマシニングの一部と考えることができます。
例として、自動車のエンジン部品の製造では、フライス加工により細かい溝や形状を正確に削り出す必要があります。また、スマートフォンの金属フレームを作る際も、フライス加工が重要な役割を果たします。
このように、フライス加工は特定の形状を持つ製品を作り出すのに適している一方、マシニングはより広範な加工技術を指します。フライス加工の精度と多様性は、多くの製造分野でその価値を発揮しています。結論として、フライス加工は製品の精密な形状を削り出すために欠かせない技術であり、マシニングはそれを含む広範な加工技術の一つです。
3-2. 加工条件に関する用語
フライス加工とは、切削工具の回転運動と被加工物の直線的な移動を利用して、材料を削り取る加工方法です。これにより、平面や溝、歯車など、様々な形状を精密に加工することが可能になります。一方、マシニングとは、フライス加工を含む広範囲の加工技術を指し、旋盤加工や研磨加工なども含まれます。つまり、フライス加工はマシニングの一部であると言えます。
フライス加工の特徴としては、非常に高い精度での加工が可能であり、複雑な形状も加工できる点が挙げられます。例えば、自動車のエンジン部品や航空機の部品製造においては、この高精度なフライス加工が不可欠です。
しかし、マシニング全般に言えることですが、加工には適切な知識や設備が必要とされます。加工する材料の種類や加工する形状によって、最適な加工方法や条件が異なります。そのため、専門的な知識を持った技術者による運用が求められるのです。
結論として、フライス加工はマシニングの中で特に精密な加工を可能にする方法であり、複雑かつ精緻な部品製造において重要な役割を果たしています。その高い加工能力と柔軟性から、様々な産業分野において広く利用されているのです。
3-3. 加工精度に関連する用語
フライス加工とは、回転する工具を使用して、金属やプラスチックなどの材料から所望の形状を削り取る加工方法です。この加工技術は、その精度の高さから多くの産業で利用されています。しかし、マシニングとの違いについては、一見すると明確ではないかもしれません。実際、フライス加工はマシニングの一種であり、マシニングとは、材料を削り取る工程全般を指す広い概念です。したがって、フライス加工はマシニングの中の特定の技術と言えます。
たとえば、フライス加工では、特に平面や溝、歯車などの加工が得意で、複雑な形状でも高い精度で製作できます。一方、マシニングの範囲には、旋盤加工や研磨加工など、他の多くの加工技術も含まれます。旋盤加工は、主に円形の材料を加工するのに適しており、フライス加工とは適用する部分が異なります。
結論として、フライス加工とマシニングの主な違いは、フライス加工がマシニングの一部であるという点にあります。フライス加工は、その高い加工精度と多様な形状の製作能力により、多くの製造現場で重宝されています。しかし、マシニング自体はより広い加工技術を指すため、フライス加工を学び、理解することは、製造業の基礎となる重要なステップです。
4. フライス加工の技術向上
4-1. 基本的な技術とノウハウ
フライス加工とは、回転する切削工具を用いて被削材から材料を削り取る加工方法です。これに対し、マシニングとは、フライス加工を含む広範囲な金属加工技術全般を指す言葉です。つまり、マシニングはフライス加工だけでなく、旋削や研磨など他の加工方法も含まれます。
フライス加工の特徴は、複雑な形状や平面を効率的に加工できることにあります。例えば、ギアの歯や航空機の部品など、精密な加工が求められる場合に多く用いられます。一方、マシニングの範囲内であれば、材料の切削以外にも、穴あけや表面の仕上げなど多様な加工が可能です。
結論として、フライス加工はマシニング技術の一部であり、特定の加工方法に限定されます。マシニングはより広い範囲の加工技術を総称したものであることを理解することが重要です。知識と技術の進展に伴い、これらの加工方法はより高度で精密な製品の製造に不可欠なものとなっています。
4-2. 高度な技術とその応用
フライス加工とは、工作機械を使用して材料の表面を削り取る加工方法の一つです。この技術は、精密な形状や平滑な表面を必要とする部品の製造に広く用いられています。フライス加工とマシニング(機械加工)の違いは、主に使用される工具と加工法にあります。フライス加工では回転する刃を使って材料を削り取るのに対し、マシニングはドリルや旋盤など様々な種類の工具を使い、多様な加工を行うことができます。例えば、フライス加工は平面や溝、歯車などの加工に適しているのに対し、マシニングは円筒形の加工や複雑な形状を持つ部品の製造に利用されます。日本では、高い精度と効率を求められる機械部品の製造において、これらの技術が重要な役割を果たしています。要するに、フライス加工とマシニングは、製造業で使用される基本的な加工技術でありながら、それぞれ特有の特徴と適用範囲を持っています。
4-3. トラブルシューティングと改善策
フライス加工とは、主に金属を削って形を作り出す加工技術の一つです。一方、マシニングは、フライス加工を含む様々な種類の工作機械を使用して金属などの材料を加工する総合的な技術を指します。この二つの違いを理解することは、精密な部品製造において非常に重要です。
フライス加工では、回転する刃を使用して材料から余分な部分を削り取ります。この方法は、複雑な形状や平面、溝を作るのに適しています。たとえば、自動車のエンジン部品や航空機の部品製造において、フライス加工は不可欠です。
一方、マシニングは、旋盤加工や研削加工など、フライス加工以外にも様々な加工技術を含んでいます。これは、一つの部品を作るために複数の工程が必要な場合、それぞれの工程で最適な加工方法を選択するためです。例えば、円筒形の部品を作る場合は旋盤加工が、非常に滑らかな表面が必要な場合は研削加工が選ばれます。
結論として、フライス加工はマシニングの中の一つの技術であり、マシニングはより広範囲の加工技術を総合的に指します。各加工技術の選択は、製造される部品の形状や精度、表面仕上げの要求に依存します。理解と適用の正確さが、高品質な製品製造への鍵となるでしょう。
5. マシニングセンタの選び方
5-1. マシニングセンタの種類と特性
フライス加工とは、工作機械を使用して物質を削り取る加工方法の一つで、主に金属加工で利用されます。これに対し、マシニングとは、フライス加工を含む広範な加工技術の総称であり、旋盤加工や研磨なども含まれます。つまり、フライス加工はマシニングの一部というわけです。
フライス加工の特徴は、複雑な形状や精密な部品を高い精度で加工できる点にあります。例えば、航空機の部品や自動車のエンジン部品など、精度が求められる分野で広く採用されています。これに対してマシニングは、使用する機械や加工方法によって加工できる物の範囲が広がり、より多様な製品製造に寄与しています。
結論として、フライス加工はマシニングの一環として特定の加工技術を指し、マシニングはそれよりも広い加工技術の範囲を指します。フライス加工による精密な部品製造の重要性は高く、日本の製造業においても中心的な役割を果たしています。
5-2. 購入時のポイントと注意事項
フライス加工とは、工作機械を用いて金属などの材料から所望の形状や寸法を削り出す加工方法の一つです。これに対し、マシニングとは、フライス加工を含む広い範囲の機械加工全般を指します。そのため、フライス加工はマシニングの一部という関係にありますが、フライス加工特有の違いがあります。例えば、フライス加工は主にフライス盤を使用して行われ、回転する刃を用いて材料を削ることが特徴です。これに対して、マシニングには旋盤加工や研削加工など、他の機械加工方法も含まれます。フライス加工は、その精度の高さや複雑な形状も加工できる点で、多くの製造業で重宝されています。しかし、それぞれの加工方法には適した用途があり、製造工程を選定する際にはその違いを理解しておくことが重要です。結論として、フライス加工はマシニングの一環として非常に有効な方法であり、その特性と適用範囲を把握することが製品製造の効率化と品質向上に繋がります。
5-3. コストパフォーマンスの考慮
フライス加工とは、主に金属製品の表面を削って形を整える加工技術のことです。マシニングとの違いは、使用される機械や加工のアプローチにあります。フライス加工は、回転する刃を使用して材料を削り取る手法で、形状や溝を精密に作り出すのに適しています。一方、マシニングは、より広義の概念であり、フライス加工も含む多様な加工技術を指します。例えば、旋盤加工はマシニングの一形態であり、材料自体を回転させながら固定された刃で削ることで製品を形成します。
日本において、フライス加工は製造業で広く採用されており、自動車部品や電子機器など、日常生活で使用される多くの製品にこの技術が活用されています。特に、高度な精度と複雑な形状が求められる製品において、その有効性が発揮されます。
結局のところ、フライス加工とマシニングの違いを理解することは、製造プロセスの選択や技術の適用範囲を広げる上で重要です。日本の製造業におけるこれらの技術の活用は、製品の品質向上や生産効率の向上に寄与しています。
6. 精密加工のプロを目指すために
6-1. 精密加工に必要なスキルと知識
フライス加工とは、工作機械を使用して材料から不要な部分を削り取り、製品の形状を作り出す加工方法の一つです。この技術は、製品の精密さと効率性を高めるために広く利用されています。しかし、マシニングと混同されがちですが、実は両者には明確な違いがあります。フライス加工は回転する刃を使って材料を削ることに特化しており、特に平面や溝、歯車などの加工に適しています。例えば、自動車のエンジン部品や飛行機の構造部材など、複雑な形状を持つ製品の製造に不可欠です。一方、マシニングはより広義に工作機械を使用した材料の加工全般を指し、フライス加工もその一種と言えます。つまり、フライス加工はマシニングの一部でありながら、その特化した技術と用途によって区別されるのです。この理解を深めることで、製造業の現場ではより適切な加工方法を選択し、効率的かつ高品質な製品製造に繋がるでしょう。
6-2. 継続的な学習と技術習得
フライス加工とは、工作機械を用いて金属などの材料を削り取る加工方法の一つです。この技術は、精密な部品を製造する際によく使われます。マシニングと比較すると、フライス加工は特に平面や溝、歯車などの形状を加工するのに適しています。例えば、自動車や家電製品の部品製造において、フライス加工によって複雑な形状が実現されています。
マシニングはより広義の概念で、フライス加工だけでなく、旋盤加工や研磨加工など、材料を削り取るあらゆる工程を含む言葉です。つまり、フライス加工はマシニングの一部ということになります。フライス加工の特徴は、その精度の高さと、複雑な形状も実現できる柔軟性にあります。例を挙げると、機械部品の溝や、複雑なカーブを持つ部品などがこれに該当します。
このように、フライス加工とマシニングの違いを明らかにすることで、各加工方法の利点を理解し、適切な製造技術を選択することが可能になります。フライス加工の精度と柔軟性は多くの産業で重宝されており、その技術の進化は今後も続くことでしょう。
6-3. 業界で求められる専門家になるためのステップ
フライス加工とは、金属やプラスティックなどの材料を削って形を整える加工方法です。これに対して、マシニングは、フライス加工を含むより広い範囲の加工技術を指します。つまり、フライス加工はマシニングの一部と考えることができます。たとえば、フライス加工では、回転する刃を使って材料の表面を削りますが、マシニングには旋盤加工のように材料自体を回転させて形を整える方法も含まれます。日本において、精密な部品製造にはこれらの技術が不可欠であり、自動車や電子機器などの産業で広く利用されています。フライス加工の具体的な例としては、エンジンの部品を製造する際に使われることがあります。このように、フライス加工はマシニングの中でも特に重要な技術であると理解することが大切です。結論として、フライス加工はマシニングの範疇に含まれる特定の加工技術であり、日本の製造業における精密部品の生産に欠かせない役割を果たしています。
まとめ
フライス加工とマシニングの違いについて詳しく解説します。フライス加工は工作機械を使用して材料を削る加工方法であり、一方のマシニングは工具を使って工作物に形状を付ける加工方法です。これらの方法の違いを知ることで、それぞれの特性や利点を理解し、効果的に活用することができます。
アルミ加工の疑問を解決!よくある質問とその回答集
「アルミ加工」や「金属加工」といった用語に興味を持っているけれど、具体的にどんなことができるのか分からないという方も多いのではないでしょうか?そんな疑問を持つ皆さんに向けて、この記事ではアルミ加工に関するよくある質問とその回答をまとめました。アルミ加工の基本から応用まで、知っておくべきことが詳細に解説されています。金属加工に興味がある方、またはアルミ加工についてもっと知りたいと思っている方々にとって、参考になる内容がたくさん詰まっています。ぜひ最後までお読みいただき、アルミ加工に対する理解を深めていきましょう。
1. アルミ加工金属加工における基本知識
アルミ加工に関する疑問は、プロから初心者まで幅広い人々にとって一般的なものです。アルミは非常に加工しやすい金属であり、その軽量さと耐腐食性により、自動車や建築材料、家庭用品など、さまざまな場所で使用されています。たとえば、自動車の部品に使われると、重量を軽減し燃費を改善することができます。また、耐久性と美観を求める建築材料としても、アルミは重宝されています。加えて、日常生活においてはキッチン用品や電子機器の筐体などにも用いられており、その利用範囲は広いです。しかし、アルミ加工には専門的な技術が必要であり、加工方法によって特性が大きく変わることもあります。よって、こうした加工技術に関する知識を深めることが、製品の品質向上に繋がります。アルミ加工の疑問が解決されると、より効率的で品質の高い製品作りに役立つでしょう。
2. アルミ加工の際の注意点
アルミ加工は、その優れた特性から幅広い産業で用いられていますが、加工時にはいくつかの注意が必要です。アルミニウムは軽量でありながら強度が高いため、自動車や航空機の部品などに多く用いられています。しかし、アルミニウムは熱伝導率が高く、加工中に熱が局部的に集中しやすいため、適切な冷却技術が不可欠です。また、工具の摩耗が激しいため、専用の切削液を使用するなどして、工具の管理にも注意が求められます。具体例として、アルミ加工で使用されるエンドミルは、切れ味の持続性を保つためにダイヤモンドコーティングが施されることがあります。アルミ加工の際のこれらの注意点を守ることで、製品の品質を高め、加工効率も向上させることができるのです。
3. よくあるアルミ加工金属加工の質問と回答
アルミ加工に関して疑問を感じることは、初心者だけでなく経験者の中にも多くあります。アルミ加工は、その軽量性と耐食性から多くの業界で採用されており、金属加工の中でも特に利用範囲が広い材料の一つです。しかし、加工方法や用途に応じた技術の選択に関しては、しばしば疑問が持たれます。たとえば、なぜアルミは熱処理をするのか、また、特定の加工にはどのような工具が必要なのかなど、具体的な質問が寄せられます。これらの質問に対し、アルミの物性を理解することで、適切な加工技術や工具の使用が可能になることを専門家は説明します。例えば、アルミ合金の種類によって熱処理の方法を変える必要があることや、アルミ専用の切削液を使用することが推奨されていることなどが挙げられます。これらの知識を持つことで、より効率的で高品質なアルミ加工を行うことができるでしょう。
4. ステンレス加工とアルミ加工の違い
ステンレス加工とアルミ加工は、どちらも金属加工の中で重要な位置を占めていますが、それぞれに特徴が異なります。アルミ加工はその軽さから、航空機や自動車などの分野で特に重宝されているのです。この軽量性は、製品の燃費改善にもつながります。また、アルミニウムは優れた熱伝導性を持っており、熱交換器やクッキングウェアなどにも利用されています。一方で、ステンレスは耐食性に優れており、厨房器具や医療機器など、衛生的な環境が求められる場所での使用が一般的です。なお、加工技術や設備によっても、それぞれに適した加工方法が異なり、これらを理解することは金属加工を扱う上で不可欠です。アルミ加工に関する疑問や質問があれば、専門家に相談するのがおすすめです。
5. めっき加工におけるアルミの特性
アルミ加工に対する疑問を解決するため、よくある質問にお答えします。アルミは軽量でありながら強度が高いため、多くの金属加工の分野で使用されます。たとえば、自動車や航空機の部品においてアルミはその軽量性を活かし、燃費の向上に貢献しています。また、耐食性に優れるため建築物の材料としても選ばれやすいです。しかし、アルミは熱伝導率が高く、めっき加工時に熱を均等に分散させる必要があるなど、特有の注意点があります。結論として、アルミ加工はその優れた特性を理解し、適切に加工することで、そのポテンシャルを最大限に引き出すことができるのです。
6. アルファフレームとは?アルミ加工金属加工の応用
アルファフレームは、アルミ加工技術を活用した製品の一例で、金属加工の分野において注目を集めています。なぜなら、アルファフレームは、その軽量性と高い強度を生かし、様々な産業で利用されるからです。例えば、輸送機器のフレームや建築資材として使われ、その汎用性の高さから多岐にわたる用途に適応しています。さらに、アルミニウムは錆びにくいため、耐久性に優れ、メンテナンスのコスト削減にも繋がります。このような特性から、アルファフレームは、今後も様々な場面での需要が見込まれ、アルミ加工・金属加工の技術がさらに進化することによって、その利用範囲は広がっていくことでしょう。
7. 装飾金物のアルミ加工について
装飾金物のアルミ加工は、その軽さと加工のしやすさから多くの場面で使用されています。アルミニウムは軽量でありながら強度が高く、さらに耐食性にも優れているため、幅広い製品に利用される理由があります。例えば、建築物の部品や家具の装飾、さらには自動車のパーツに至るまで、アルミ加工は多岐にわたり活躍しています。特に建築物における装飾金物では、その耐久性と美観が要求されるため、アルミニウムの持つ特性が非常に重宝されます。また、アルミニウムはリサイクルが容易という利点もあり、環境への配慮を考慮する現代においても、その需要は高まる一方です。このように、様々な利点を持つアルミ加工は、今後も多くの分野で利用され続けるでしょう。
8. ブラスト加工とアルマイト処理の基礎
アルミ加工に関する疑問を多く持つ方々へ、その疑問を解消するための情報を提供します。アルミ加工は、その軽量さと耐食性から様々な業界で重宝されています。例えば、自動車産業や航空機材料として、また建築材料としても使用されています。なかでも、ブラスト加工とアルマイト処理はアルミ加工の一般的な方法です。ブラスト加工は、アルミの表面を研磨して滑らかにするために行われ、表面の小さな傷を除去し、均一な質感を与えます。一方、アルマイト処理は、アルミ表面に酸化皮膜を形成させることで、耐食性を高める効果があります。これらの加工は、アルミの機能性を高め、長期間の使用に耐えうる製品を作り出すために不可欠です。結論として、アルミ加工は金属加工の重要な分野であり、ブラスト加工やアルマイト処理によって、製品の質と寿命を向上させることができるのです。
まとめ
アルミ加工についてよくある疑問や質問について、以下のような回答があります。Q:アルミ加工とはどのようなものですか?A:アルミ加工とは、アルミニウムという金属材料を加工し、加工品を製造することです。Q:アルミ加工の製法にはどのようなものがありますか?A:アルミ加工の製法には、切削加工やプレス加工、溶接加工などがあります。Q:アルミ加工製品の使用用途は?A:アルミ加工製品は自動車部品や建築材料、機械部品など、さまざまな分野で使用されます。
【プロが教える】アルミ加工の基本と金属加工の違いを徹底解説!
金属加工の中で重要な一環を担うアルミ加工。本記事では、アルミ加工の基本から金属加工との違いについて詳しく解説します。アルミ加工の基本的な仕組みや特長、そして金属加工との比較までを網羅。アルミ加工の世界への理解を深め、技術や知識を磨くための一助となることでしょう。
1. アルミ加工とは?基本概念の紹介
アルミ加工とは、アルミニウムを切ったり曲げたりして形を変えることです。この金属は他の金属に比べて軽量でありながら強度を持っており、錆びにくいという特性を持っています。これらの特徴から、アルミは航空機から日用品まで幅広い分野で使用されています。例えば、自動車の部品や缶ジュースの容器など、私たちの身の回りにある数多くの製品にアルミが加工されて使われています。金属加工と聞くと難しいと思われがちですが、アルミ加工は比較的容易であり、独自の加工技術も多く存在しています。これらの方法を理解することで、より効率的かつ高品質な製品作りに繋がります。結論として、アルミ加工はその特性と加工のしやすさから、多くの産業で重宝されているのです。
2. 金属加工とアルミ加工の違い
金属加工とは広い範囲に及ぶ技術であり、アルミ加工はその一環を担っています。金属加工には鉄やステンレスなどさまざまな材料が使用されますが、アルミ加工は、その軽さと強度、そして加工のしやすさから、自動車や航空機、電子機器など幅広い産業で活用されています。さらに、アルミは優れた耐食性を持っており、特に屋外での使用に適しています。例えば、自動車のボディや飛行機の機体などは、軽量化を実現しながら耐久性を保つためにアルミが選ばれています。これらの特性から、アルミ加工は金属加工の中でも特に重要な位置を占めており、その技術の進歩は各産業の発展に不可欠です。結論として、アルミ加工の基本を理解することは、金属加工全般の理解を深める上でとても重要であり、これらの知識が産業の革新に寄与することに繋がります。
3. アルミ加工の種類とその特徴
アルミ加工は、その軽量性や耐食性から多くの産業で利用されています。金属加工の中でも、アルミ加工は独自の技術と知識が求められる領域であり、他の金属とは異なる特有の加工法を持っていることが大きな特徴です。例えば、アルミニウムは熱伝導率が高いため、溶接時には特別な技術が必要となります。また、アルミの酸化膜を活用したアルマイト処理は、耐食性を高めるだけでなく、美しい仕上がりを実現することもできます。さらに、アルミは加工しやすく、曲げや切削加工においても比較的容易に形状を変えることができます。これらの特性を生かした加工技術は、航空機材や自動車部品、家電製品など幅広い製品に応用されており、アルミ加工の重要性は今後も高まることでしょう。結論として、アルミ加工は特殊な技術を要する一方で、その応用範囲の広さと加工の容易さから、金属加工の中でも特に重要な位置を占めています。
4. 切削加工の基礎とアルミ加工への応用
アルミ加工は、軽量で錆びにくいなどの特性を持つことから、様々な産業で重宝されている技術です。比較的柔らかい金属であるため、加工しやすいという利点がありますが、他の金属加工とは異なるポイントも多いです。例えば、アルミは熱伝導率が高いため、切削加工中に発生する熱を逃がすための工夫が必要です。また、アルミの表面には酸化皮膜が形成され、これが切削刃の摩耗を早めることもあります。適切な潤滑剤の選定や切削条件の調整が、成功へと繋がります。アルミ加工のプロから学ぶことで、これらの特性を理解し、効率的で高品質な加工が可能になるでしょう。再度結論を述べると、アルミ加工は専門的なテクニックが求められる分野で、基本を学ぶことが極めて重要です。
5. アルミ加工の難しさと解決策
アルミ加工は、その特性から金属加工の中でも特に注意を要する工程です。その理由は、アルミニウムが軽量で熱伝導率が高く、柔らかいため、加工時において形状を保持しにくく、切削工具への負担も大きくなりがちです。例として、切削加工では、アルミニウムの柔らかさが原因で工具が詰まりやすく、また熱が局所的に集中しやすいため、精度の高い加工が難しいという問題があります。しかし、工具の選定に工夫を凝らすことで、これらの問題はある程度解決可能です。例えば、アルミ専用の切削工具を使用することや、適切な冷却剤を用いることで、加工精度を向上させることができます。したがって、アルミ加工においては、金属の性質を深く理解し、適切なツール選びと加工方法を学ぶことが重要であり、それによって加工の難しさを克服し、品質の高い製品を生み出すことができるのです。
6. 金属加工の方法とアルミ加工の選択肢
アルミ加工は、その軽量性や耐食性から、多くの産業で重宝されています。金属加工と比較した場合、アルミは加工しやすい特性があり、特に精密な部品製造においては優れた材料となります。例えば、航空機の部品や電子機器の筐体など、高度な技術を要する製品に用いられることが多いです。しかしながら、加工の方法によっては、材料の特性を十分に活かせない場合もあります。適切な加工技術の選択は製品の品質を決定づけるため、プロの知識が必要不可欠です。したがってアルミ加工の基本を理解し、それぞれのプロジェクトに適した方法を選ぶことが、製品の成功に結びつくのです。
7. 機械加工の基礎知識とアルミへの適用
アルミ加工は金属加工の中でも特に扱いやすく、多くの産業で利用されています。金属加工と比較して、アルミは軽量でありながら強度が高く、耐食性にも優れているため、自動車や航空機の部品から日用品まで幅広い用途に適しています。例えば、自動車のエンジン部品や航空機のフレームに使用されることが多いですが、これはアルミニウムの軽さと強度が求められるからです。加えて、アルミは加工しやすい性質を持っており、切削や曲げ、溶接などの工程でも扱いやすいという利点があります。特に、精密な部品を必要とする電子機器の分野では、その加工のしやすさが重宝されています。最終的にアルミ加工は、その優れた物性と加工性のバランスが、多様な製品の製造に貢献していると言えるでしょう。
8. 鋳造法とアルミ加工の関連性
アルミ加工は金属加工の中でも特に技術が要求される分野であり、他の金属加工とは異なる独自の特性を持っています。その理由として、アルミニウムは軽量でありながら強度を持ち、熱伝導性や耐食性に優れているため、航空機材や自動車部品など幅広い製品に利用されています。具体的な例を挙げると、アルミニウムは鋳造法によって複雑な形状の部品を製造するのに適しており、これは他の金属では難しいことも珍しくありません。このようにアルミ加工は、その特性を活かした加工技術が求められるため、専門の知識と技術が不可欠です。結論として、アルミ加工の理解を深めることは、多様化する金属加工のニーズに応え、より高品質な製品を生み出すために重要なのです。
9. アルミ加工のメリット・デメリット
アルミ加工には、金属加工の中でも特有のメリットとデメリットが存在します。アルミニウムは軽量でありながら強度が高く、熱伝導性や耐食性に優れているため、航空機や自動車など幅広い分野で利用されています。例えば、自動車の部品では、アルミの軽量性が燃費の改善に寄与しています。また、耐食性が高いことから、建築材料としても外壁材や屋根材などに用いられることがあります。しかし、加工時には他の金属と比べて柔らかいため、精密な加工を要する場合には、技術的な工夫や設備投資が必要になることがあります。さらに、アルミは他の金属に比べて耐摩耗性が低いため、使用環境によっては表面処理などの追加的な対策が求められることもあります。これらの特性を理解し、適切に対応することでアルミ加工はより効果的になります。
10. アルミ加工の最新技術と将来性
アルミ加工は、その軽さや加工の容易さから多くの産業で使用され、金属加工の領域においても独自の位置を占めています。通常の鉄や銅と異なり、アルミニウムは加工時の応力が少なく、また熱伝導性に優れているため、電子機器の放熱部材など精密な部品作りにも適しています。例えば、自動車のエンジン部品や航空機の構造材としてもアルミ合金が欠かせない素材です。現代においてアルミ加工技術は進化を続け、その軽量性を活かした最新の自動車や航空機への応用例も増えています。将来的には、より高度なアルミ加工技術が求められるでしょうし、その展開はさらに幅広い分野へと広がると考えられます。最終的に、環境への影響を考えたサステナブルな材料選択としても、アルミニウムの利用はますます重要になっていくことでしょう。
まとめ
アルミ加工はアルミニウムを加工することを指し、金属加工は様々な金属を加工することを指します。アルミ加工には切削加工や溶接加工などがあり、金属加工にはそれに加えて鍛造や鋳造などの加工方法があります。アルミ加工ではアルミニウムの特性を理解し適切な加工法を選択することが重要です。一方、金属加工では材料ごとの特性を把握し、適切な加工法を選ぶことが求められます。
金属加工から学ぶ!アルミ素材の特性と加工時の注意点
アルミ素材の特性と加工時の注意点を学ぶことは、製造業や金属加工に携わる方々にとって重要なテーマです。アルミ加工における課題に直面し、その解決策を模索している方も多いのではないでしょうか。本稿では、アルミ素材の特性や加工時の注意点について詳しく解説しています。アルミ加工に関心がある方や技術向上を目指す方々にとって、貴重な情報となることでしょう。
1. アルミ加工金属加工の基礎
アルミは軽量でさびにくいという特性から、自動車や航空機の部品、さらには日用品に至るまで幅広く使用されています。しかし、金属加工においてアルミの特性を理解し、適切に扱わなければ、その優れた特性を十分に活かすことはできません。具体的には、アルミは熱伝導率が高いため加工時には工具や機械の温度管理に注意が必要です。また、柔らかく加工しやすい一方で、切削時にはバリが発生しやすく、仕上げにも細心の注意が求められます。適切な工具選びと加工パラメータの調整が、アルミ加工の品質を左右すると言っても過言ではありません。このように、アルミ素材の特性を把握し、それに合わせた加工技術を身につけることで、高品質なアルミ製品を生み出すことが可能になります。
2. アルミ素材の種類とその特性
アルミ素材は軽量でありながら強度が高いため、航空機や自動車など多岐にわたる産業で重宝されています。特に、その加工性に優れ、熱伝導率が高いことから冷却部品にも用いられることが多いです。例えば、アルミ合金の中でもA6061は耐食性があり、機械加工にも適しており一般的な用途に広く利用されています。しかしアルミ加工には注意が必要で、切削時には工具の摩耗が激しいことや、アルミの熱膨張による精度の問題が生じることがあります。そのため、適切な切削液の使用や、温度管理が重要になってきます。最終的に、適切なアルミの種類の選択と加工方法の理解を深めることで、金属加工の幅が広がり、より質の高い製品を作り出すことが可能になります。
3. アルミ加工の基礎知識と技術
アルミ加工は金属加工の中でも特に注目されており、それはアルミ素材の優れた特性によるものです。アルミは軽量かつ強度があり、加工性に富む金属で、航空機や自動車など幅広い分野で使われています。しかし、その加工には注意が必要です。アルミの熱伝導率は高く、切削時には熱が局所的に集中しやすいため、適切な冷却が必須です。また、アルミは柔らかいため、工具の摩耗が起こりやすいという点も考慮しなければなりません。具体的な例としては、アルミ合金の種類によって適した切削速度が異なるため、材料の種類に応じた適正な加工条件の選定が重要となります。最終的に、適切な知識と技術をもってアルミを加工することで、その素晴らしい特性を最大限に活かすことができるのです。
4. アルミ合金の切削加工とその特徴
アルミ加工は、金属加工における重要な分野の一つです。アルミは軽量でありながら強度を持つため、多くの産業で利用されています。しかし、加工する際にはいくつかの注意点があります。まず、アルミは熱伝導率が高いため、加工時には熱が素早く拡散されることを理解する必要があります。これにより、切削工具に過度な負担をかけずに加工が可能ですが、一方で工具の摩耗を早める原因にもなります。例えば、アルミのフライス加工をする際は、適切な切削速度と冷却液の使用が重要です。また、アルミは柔らかい金属なので、切りくずが詰まりやすく、これを避けるためにはシャープな刃を使用し、定期的に切りくずを除去する必要があります。最終的には、これらの注意点を押さえつつ適切な工具を選び、適正な加工条件を見極めることで、アルミは非常に加工しやすい素材であると言えます。
5. アルミ材ごとの特性と加工時のメリット/デメリット
アルミ加工はその軽量性や耐食性に優れた特質から、幅広い産業で利用されています。しかし、加工する際にはいくつかの注意点があります。例えば、アルミニウムは軟らかく熱伝導性が高いため、加工時には熱管理が重要となり、切削液を適切に使用しなければなりません。また、種類によっては硬い物質を含むため、工具の摩耗が激しくなることもあります。これは、加工技術や工具選びにも影響を与えるため、アルミの特性を理解することが不可欠です。さらに、アルミニウムの種類によっては、耐熱性や強度が異なるため、製品の用途に応じた材質選びも重要です。結論として、アルミ加工はその特性を理解し、適切な加工方法を選択することで、そのメリットを最大限に活かすことができるのです。
6. アルミニウムと他素材の比較分析
アルミニウムは金属加工において、その軽量さや耐食性により様々な産業で好まれています。アルミ加工は特有の注意が必要ですが、正しく処理することにより、その優れた性質を最大限に発揮することができます。例えば、アルミは熱伝導率が高いため、加工時には熱による変形に注意が必要です。また、アルミは他の金属と比較して柔らかいため、切削加工では工具の摩耗を防ぐために専用の刃物が推奨されます。また、アルミの表面は酸化しやすいので、加工後は適切な表面処理が欠かせません。最後に、これらの注意点を守ることで、アルミは航空機の部品から家庭用品まで、幅広い用途に利用される頼もしい素材となります。結論として、アルミ加工の際にはその特性を理解し、適切な方法を取ることが重要です。
まとめ
金属加工において、アルミ素材は軽量であるため取り扱いが比較的容易です。また、耐食性や耐蝕性に優れており、耐久性にも優れています。一方で、アルミ素材は軟らかいため、加工時には切削や加熱による注意が必要です。特に熱加工時には適切な冷却が必要です。