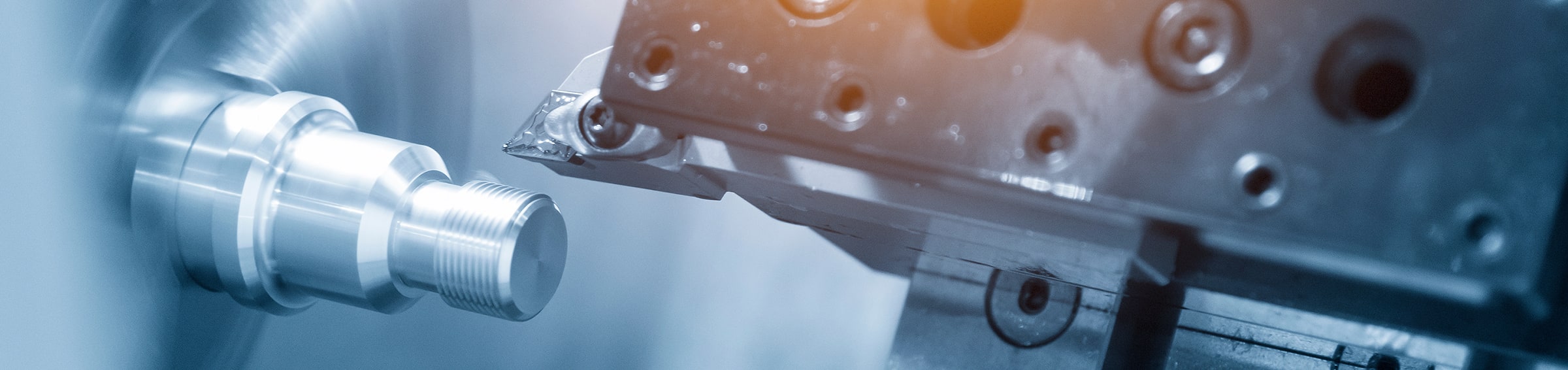
コラム column
【材料知識】A6061とA2017違いと使い道:エンジニアが知るべき事実
エンジニアの皆さん、アルミニウム合金のA6061とA2017について知っていますか?これらの違いや使い道について知識を深めてみませんか?この記事では、A6061とA2017の比較に焦点を当て、エンジニアが知るべき事実を詳しく解説していきます。異なる特性や適用範囲、製品開発における適切な選択肢について理解することで、より良い製品開発に繋げることができるでしょう。さあ、A6061とA2017の違いを知り、使い道を探求してみましょう。
1. イントロダクション
A6061とA2017は、その特性の違いにより異なる用途で活用されるべきです。A6061は耐食性と加工性に優れ、自動車部品や建築物の建材などに用いられます。一方、A2017は機械的強度が高く、航空宇宙産業や精密機器での使用が適しています。例えば、A6061は自転車のフレームや船舶の部材に、A2017は航空機の部品やギアなど、より高い強度が求められる部分に使用されます。これらの特性を理解することは、材料を適切に選択し、長期にわたる製品の信頼性と性能を確保するために重要です。結論として、A6061とA2017の選択は、その用途と求められる特性に応じて慎重に行うべきであり、エンジニアにとってこの知識は不可欠です。
2. A6061とA2017の基本的な違い
A6061とA2017は、どちらもアルミニウム合金でありながら、それぞれに特徴が異なり、使い道が分かれます。A6061は優れた耐食性と加工性を持ち、航空機や自動車の部品、建築材料など幅広い用途に使われます。一方、A2017はA6061よりも強度が高く、特に機械部品やプレス部品に適していますが、耐食性はA6061に劣ります。例えば、自動車のフレームや機械のギアなど、強度が求められる部位にA2017が選ばれることが多いです。これらの特性から、エンジニアは製品の要求性能に応じて適した合金を選択する必要があり、A6061とA2017の知識は非常に重要です。最終的には、耐食性と加工性のバランスを求めるならA6061、より高い強度を必要とする場合はA2017の選択が適切でしょう。
3. A6061の特性と利点
A6061は、その優れた機械的性質と耐食性から、幅広い産業で使用されています。この合金は、特に航空宇宙産業や自動車部品、そして建築材料などの分野で好まれる素材であり、軽量でありながら高い強度と優れた加工性を提供します。例えば、自動車のホイールやフレーム構造に使用されることが多く、その耐久性と加工の容易さは製造業者にとって重要な要素です。一方、A2017は強度が高いものの加工性がやや劣り、切削や成型時に少々の工夫が必要になりますが、コストパフォーマンスに優れているため、コストを抑えつつも高い強度が求められる製品に利用されます。結論として、A6061は汎用性が高く加工性に優れた素材であり、A2017はコストを考慮しつつ強度を要求する用途に適しています。これらの違いを理解することは、適切な材料選択においてエンジニアにとって必須の知識と言えるでしょう。
4. A2017の特性と利点
A6061とA2017というアルミニウム合金は、それぞれ特徴と利点があり、エンジニアが適切な材料を選択するためには、これらの違いを理解する必要があります。A6061は耐食性に優れ、加工性が高く、溶接しやすい性質を持っています。特に、自動車のホイールや建築構造物などに使用されます。対してA2017は機械的強度が高く、特に航空機の部品や精密機器に使われることが多いです。しかし、A6061に比べて耐食性は劣ります。例えば、A6061は海洋環境でも使用されることがあるのに対し、A2017はより内陸部での使用が推奨されます。適切な合金の選択は、製品の耐久性や性能を最大限に引き出す鍵となります。したがって、これらの違いを把握し、それぞれの合金が最適な用途で利用されることが重要です。
5. 材料選びの基礎知識:A6061とA2017
A6061とA2017はいずれもアルミニウム合金でありながら、その特性や用途には明確な違いがあります。A6061は耐食性や加工性が高く、自動車の部品や航空機の構造材として広く使用されています。一方でA2017は、A6061に比べて強度が高いため、精密機械や高負荷がかかる部分の材料として好まれます。例えば、A6061は自転車のフレームに使用されることが多い一方で、A2017はギアやロボットの部品などに利用されることが一般的です。このような違いを理解することは、材料を選ぶ際の大切な知識となり、適切なアルミニウム合金を選定することで、製品の信頼性と性能を最大限に引き出すことが可能です。
6. 建築と工事の積算基準:A6061とA2017のコスト
建築や工事で使用する材料選びは、コストと性能のバランスが重要です。その中で、アルミニウム合金のA6061とA2017は、コスト面において利点が異なります。A6061は耐食性に優れ、加工性も良好ですが、A2017はより高い強度を有しているため、用途に応じて選ばれます。例えば、A6061は自動車のホイールや建築の装飾材として好まれる一方で、A2017は航空機の部品や精密機器に用いられることが多いです。コストを考慮すると、A6061は一般的にA2017よりも安価で入手しやすいです。従って、総合的なコストパフォーマンスと目的に応じて、これらの材料は適切に選ばれるべきでしょう。
7. セメント系補修・補強材料としてのA6061とA2017
A6061とA2017は、それぞれ異なる特性を持つアルミニウム合金であり、これらの違いを理解することはエンジニアにとって重要です。A6061は耐食性に優れ、加工性が良いため、自動車の部品や建築の構造材料として一般的に利用されています。一方、A2017は強度が高い一方で加工性はやや劣りますが、高い疲労強度のため航空機の部品や精密機械の部材に使用されることが多いです。例えば、A6061は自動車のホイールや建築のフレームとして使われる一方で、A2017は航空機のフレームやギアなどの部品に適しています。したがってA6061は汎用性が高く、A2017は特定の用途に最適化されていると言えるでしょう。これらの特性を踏まえ、適切な合金を選択することが、製品の性能を最大限に引き出す鍵となります。
8. A6061とA2017の安全性と石綿対策
A6061とA2017は、どちらもアルミニウム合金でありながら、その特性と使い道に重要な違いがあります。A6061は耐食性や溶接性が良く、自動車のフレームや造船、航空機の部品に使用されます。対照的に、A2017は加工性が高く、自動旋盤での精密加工に適しているため、精密機器の部品や電子機器の筐体に用いられることが多いです。例えば、A6061はより耐久性が必要な外部構造に、A2017は複雑な形状を必要とする小型部品に適しています。これらの材料の選択は、製品の性能と寿命に直接影響を及ぼし、エンジニアにとって重要な判断基準となります。最終的には、A6061とA2017はそれぞれ異なる特性を持ち、適切に選択することで希望する工業製品の実現が可能となります。
9. 建設現場でのA6061とA2017の取り扱い
エンジニアにとって、アルミニウム合金のA6061とA2017の違いを理解し、適切な用途に用いることは重要です。A6061は耐食性や溶接性に優れ、さらに加工性も良好なため、自動車の部品や建築物の構造材として広く使用されています。一方、A2017は機械的性質が高い一方で加工が難しく、航空機材や高精度な機械部品など、高い強度が要求される場所に適しています。例えば、A6061は自転車のフレームや登山用具にも使われることがありますし、A2017は精密機器のギアや部品に採用されることがあります。これらはそれぞれの物理的特性に基づいた選択で、適材適所を考慮した結果です。結論として、A6061とA2017はそれぞれ異なる特性を持ち、使い道を正しく理解することで、その特性を最大限に活かすことができます。
10. エンジニアが知るべきその他の事項
アルミニウム合金のA6061とA2017は、工業分野でよく利用される素材ですが、その特性と用途には重要な違いがあります。A6061は優れた耐食性と加工性を持ち、自転車のフレームや航空機の部品など、ある程度の強度が求められる製品に使われます。一方でA2017は、A6061よりも強度が高いが耐食性は劣るため、精密機械の部品や自動車の部品など、より高い強度が必要とされる場面で選ばれます。例えば、自動車のサスペンションシステムでは、A2017の高い強度が活かされています。エンジニアはこれらの特性を理解し、それぞれの合金が最も効果を発揮する用途に適切に用いることが大切です。また、耐久性が求められる製品を設計する際には、これらの違いを考慮に入れる必要があります。
まとめ
A6061とA2017はともにアルミニウム合金であり、主に機械加工部品や航空機部品などに使用されます。A6061は耐食性に優れており、溶接性や加工性が高いのが特徴です。一方、A2017は高強度であり、熱処理によって強度を更に引き上げることが可能です。それぞれの特性に合わせて、使用する場面を選択することが重要です。
A6061かA2017か?プロジェクトに最適なアルミ合金の見極め方
アルミ合金を使ったプロジェクトを計画中ですか?A6061とA2017の違いが分からずに困っていませんか?この記事では、それぞれの特性や適用先について解説します。プロジェクトに最適なアルミ合金を見極めるための情報が満載です。
Contents
1. A6061とA2017の基本的な違いとは?
プロジェクトに適したアルミ合金を選ぶことは、成果の質を左右する重要な決定です。特にA6061とA2017は一般的に利用される合金であり、その特性を理解することが重要です。A6061は加工性が高く、耐食性にも優れるため、自動車の車体材料や建築資材に適しています。一方、A2017は強度が高い点が特長で、航空機の部品や精密機器など強度が求められる用途に利用されます。例えば、自動車の車体には耐食性と加工性を重視してA6061が選ばれる場合が多いですし、航空機の部品には高い強度が必要なためA2017が使われることが一般的です。最終的には、プロジェクトの要件に合わせて、適切なアルミ合金を選ぶことが成功へのカギとなります。
2. 異種アルミニウム合金のレーザ溶接におけるA6061とA2017
プロジェクトに最適なアルミ合金を見極める方法として、A6061とA2017の特性を比較することが重要です。A6061は耐食性に優れ、加工性も良好であるため、さまざまな産業で広く使用されています。一方、A2017は強度が高い点が特徴で、航空機の部品など要求性能が厳しい分野で利用されています。例えば、海や山など厳しい環境で使用する登山用具やマリンスポーツ用品には、耐食性の高いA6061が適しています。一方で、高い強度が求められる自動車の部品やロボットの骨組みには、A2017が選ばれることが多いです。最終的には、用途に応じて耐食性、強度、加工性などの要素を総合的に判断し、プロジェクトに最適な材料を選定することが大切です。
3. 自動車用ボルト向け6061とA2017アルミニウム合金線の比較
プロジェクトに適したアルミ合金を選定する際、A6061とA2017の選択は技術的な知識を要します。結論から申し上げると、特定の用途に応じて、どちらの合金が最適かが異なります。A6061は耐食性と溶接性に優れているため、建築や輸送機器に向いています。一方、A2017は機械加工性と強度が強みであり、精密機械や高負荷を受ける部品に適しています。例えば、自動車のボルトには耐久性が要求されるため、A2017が好まれることが多いです。しかし、海洋環境での使用など、腐食に対する高い耐性が求められる場合には、A6061が選ばれることが一般的です。したがって、アルミ合金を選ぶ際には、使用環境や必要な特性を総合的に考慮し、それぞれの利点を活かすことが肝心であるという結論に至ります。
4. アルミ合金の特徴と選び方:A6061とA2017のケーススタディ
プロジェクトに最適なアルミ合金を選ぶ際、A6061とA2017の違いを理解することが重要です。結論から言うと、用途に応じて適材適所での選択が求められます。A6061は耐食性に優れ、加工性が高く、溶接性にも優れているため、自動車の部品や建築材料など幅広い用途で使用されています。一方、A2017は強度が高いことが特徴で、航空機や鉄道車両の部品など、強度が求められる分野での使用が理想的です。例えば自動車のエンジンパーツには、高温下でも強度を維持するA2017が選ばれることが多く、一方で一般的な建築材料では、耐食性と加工性を重視したA6061が使われる傾向にあります。最終的な選択は、プロジェクトごとの必要条件をしっかりと見極めた上でなされるべきです。
5. アルミ合金押出型材四角棒におけるA6061とA2017の特性
プロジェクトに最適なアルミ合金を選ぶ際は、それぞれの特性を理解することが必須です。A6061は耐食性に優れ、加工性も良好であるため、自動車の部品や建築材料など幅広い用途に利用されています。一方、A2017は強度が高く、航空機の素材として使われることが多いですが、耐食性はA6061より劣るため、使用環境を選びます。例えば、自動車のエンジン部品には高い強度が求められるためA2017が選ばれがちですが、海辺の建築物には耐食性を優先してA6061が使用されることが一般的です。このように、目的に応じて最適な合金を選ぶことが、プロジェクトの成功に繋がります。最終的には、そのプロジェクトの具体的な要件に合わせて、A6061かA2017かを見極める必要があります。
6. アルミニウム合金材料の曲げ性能:A6061とA2017の分析
アルミニウム合金の中でも、特にA6061とA2017はプロジェクトに応じて適した選択が求められます。結論から言えば、加工性や耐食性を求める場合はA6061が、強度を重視する場合はA2017が適しています。なぜなら、A6061は加工が容易で、耐食性に優れており、様々な産業で幅広く使用されているためです。例えば、自動車の車体や建築物の構造材など、耐候性が重要視される場合に選ばれます。一方、A2017は強度が高く、特に航空機や軍事産業での使用が目立ちますが、耐食性には劣るため、その点を考慮する必要があります。したがって、プロジェクトの要件に応じた材料選定が必要で、耐久性と加工性のバランスを見極めることが重要です。
まとめ
アルミニウム合金A6061とA2017の違いを理解することは、プロジェクトにとって重要です。A6061は強度と耐食性に優れており、溶接や機械加工に適しています。一方、A2017は耐食性に優れ、熱処理によって強度を高めることができます。プロジェクトの要件に応じて、適切なアルミ合金を選定することが重要です。
【徹底比較】A5056とA2017の違いとは?選ぶべきアルミ合金のポイント解説!
アルミニウム合金を使用した製品を選ぶ際、A5056とA2017の違いを知っていますか?この記事では、A5056とA2017の特徴やポイントを徹底比較し、どちらを選ぶべきかを解説します。アルミニウム合金製品の選び方に迷っている方にとって、この記事はぜひ参考になるでしょう。
1. A5056とA2017の基本的な違いと概要
A5056とA2017は、それぞれ特有の特性を持つアルミ合金です。A5056は耐食性に優れ、特に海水での使用に適しています。それに対し、A2017は加工性に優れており、一般的な産業で幅広く使用されています。例えば、A5056は船舶や海洋関連施設での使用が挙げられ、A2017は自動車部品や電子機器の筐体など、精密な加工が必要な場面で好まれます。選ぶべきアルミ合金は、使用環境や目的によって異なります。耐食性が求められる場合はA5056、加工性を重視するならA2017と選択するのがポイントです。最終的に、それぞれの特性を理解し、用途に合った合金を選ぶことが重要です。
2. A5056の特徴と用途
A5056合金は、軽量かつ高い耐腐食性を持つため、航空宇宙や自動車部品など、強度と耐久性が求められる分野でよく使用されています。一方、A2017合金は加工性が良好でありながらも、強度が必要な構造材に適しており、多くの産業機械や建築物に採用されています。両者の大きな違いとしては、A5056がマグネシウムを多く含んでいるため耐食性に優れ、海水や化学薬品にさらされる環境でも使用できる点が挙げられます。例えば、A5056は船舶の部材や海洋構造物に適しており、A2017は自動車の軽量化を図る際の部品やロボットのフレーム材料として選ばれることが多いです。選択に当たっては、使用環境や必要な特性を考慮し、それぞれの合金の特徴を生かした適切な材料を選ぶことが大切です。
3. A2017の特徴と用途
A5056とA2017は、どちらも多岐に渡る産業で使用されるアルミニウム合金ですが、それぞれに適した用途が異なります。A5056は、その優れた耐食性と溶接性から、海洋関連の部品や輸送用容器などに好んで使用されます。一方、A2017は強度が高いため、航空機の部品や精密機器など、耐久性が求められる分野に適しています。具体的には、A5056は船舶のマストやファスナーに、A2017は航空機のフレームやギアに使われることが挙げられます。したがって、使用環境や求められる特性に応じて、最適なアルミ合金を選ぶことが重要です。A5056とA2017、各々の特徴を知ることが、適切な材料選びのポイントとなるでしょう。
4. A5056 A2017 違い:化学成分と物理的特性比較
A5056とA2017のアルミ合金は、それぞれ特有の特徴があり、用途に応じて選択することが重要です。総じて、A5056は耐食性に優れ海洋部品などに適しており、A2017は加工性に優れ機械部品などに適しています。例えば、A5056はマグネシウムを多く含むため、優れた耐食性を誇り、船舶や海上構造物に使用されることが多いです。一方で、A2017は銅を含んでいるため加工が容易で、精密な機械加工が必要な部品や、耐疲労性を求められる自動車の部品によく利用されます。選択する際には、使用環境や求められる性質を考慮し、それぞれの合金が持つ特徴を理解することが肝要です。最終的には、用途に最適な材料を選ぶことで、製品の耐久性と性能が最大限に発揮されるのです。
5. A5056 A2017 違い:加工性能の比較
アルミ合金のA5056とA2017は、それぞれに特色があり、選択する際のポイントは使用目的に合わせて異なります。結論から言うと、A5056は耐食性に優れている一方で、A2017は加工性が高いという特徴があります。例えば、A5056は海水に強いため、船舶や海洋構造物に適しています。一方、A2017は加工しやすく、自動車の部品や精密機器によく使用されます。特に、複雑な形状を加工する際には、A2017の性質が生かされます。最終的に、耐食性が重要な場面ではA5056を、加工性を重視する場合はA2017を選ぶべきです。適材適所に合わせたアルミ合金の選定が、製品の性能と寿命を最大化します。
6. A5056 A2017 違い:耐久性と耐蝕性の比較
A5056とA2017はそれぞれ特有の利点があり、選択する際には用途に適した合金を選ぶことが重要です。まず、A5056は耐蝕性に優れており、海水などの厳しい環境下でも利用できるため、船舶や海洋関連の構造物に適しています。一方でA2017は加工性に優れており、高い強度が必要な航空機や自動車部品などに用いられます。例えば、A5056は塩水にさらされることの多いマリンスポーツ用品に使用されることがあり、この耐蝕性は長期にわたる使用においても性能を維持するのに役立ちます。A2017は加工しやすさから、複雑な形状の部品製造にも適しています。結論として、A5056は耐蝕性を重視する場合に、A2017は加工性と強度を求める場合に最適な選択と言えます。
7. A5056 A2017 違い:コストパフォーマンスの分析
A5056合金とA2017合金の選択は、用途に最適な材料を選ぶ上で重要なポイントです。結論から申し上げると、A5056は耐食性に優れ、A2017は加工性が高いという大きな違いがあります。例えば、A5056は海水への耐性が必要な船舶や化学プラントに適しているのに対し、A2017は自動車や航空機の部品など精密な加工が求められる用途に適しています。A5056はマグネシウムを多く含むため耐食性に優れており、A2017は銅を含むために加工後の強度が増す特徴があります。これらの特性から、各合金の選択は、コストと必要な性質を考慮して行うべきです。最終的には、用途に合わせた適切な選択がコストパフォーマンスの高い製品に繋がるでしょう。
8. A5056とA2017:どちらがあなたのニーズに合うか?
A5056とA2017のアルミ合金は、それぞれ特有の特性があり、用途に応じて選ぶべきアルミ合金が異なります。A5056は、その耐食性と強度の高さから、海に面した建築物や輸送用容器などの外部構造物に適しています。一方、A2017は加工性に優れ、自動車の部品や精密機器など、細かい加工が必要な用途に向いています。具体的に例を挙げると、A5056は船舶の部品や海上プラットフォームの構造材料に用いられる一方で、A2017は航空機の一部や高精度な機械の部品に用いられることが多いです。このような特性を踏まえ、自身の要件に合うアルミ合金を選択することが重要です。総じて、A5056は耐蝕性と強度を、A2017は加工性を優先する場合に適しています。
9. A5056 A2017 違い:最終的な選択ガイド
A5056とA2017では、使用される場面に応じた特性の違いがあります。A5056合金は、海水や腐食性の強い環境でも強度を保つことができる耐食性に優れています。これは、船舶や海洋構造物に使用されることが多い理由です。一方、A2017合金は高い強度と良好な加工性を持つため、自動車の部品や機械部品に用いられることが多いです。例えば、A5056は船舶のマストやデッキ、A2017は自動車のフレームやギアなど、それぞれの特性に合わせた用途で選ばれています。最終的に選択する際には、それぞれのアルミ合金の特性を理解し、用途に応じた最適な材料を選ぶことが重要です。耐食性を重視するか、強度と加工性を重視するかで選択が分かれるため、これらのポイントを踏まえたうえで適切なアルミ合金を選びましょう。
10. A5056 A2017 違い:よくある質問と回答
アルミ合金のA5056とA2017は、それぞれ異なる性質を持ち、用途に応じて適切に選ばれるべきです。A5056は耐食性に優れた合金であり、海洋部品や建築材料としての使用が適しています。これは、A5056に含まれるマグネシウムが高い割合で合金化されているためです。一方、A2017は加工性に優れ、高強度を必要とする航空機の部品や精密機器の部材に適しています。この特性は、A2017に含まれる銅の含有量が高いことに由来しています。たとえば、A5056は塩水にさらされる環境での使用に適しているのに対し、A2017は高い強度と加工の容易さを活かして、複雑な形状の部品製造に用いられます。結論として、選択するアルミ合金はその用途の特性を鑑みて決定すべきで、それぞれの合金が持つ特有の性質を理解することが重要です。
まとめ
A5056とA2017との違いを理解することは、適切なアルミ合金を選ぶための大切なポイントです。A5056は耐食性や溶接性に優れており、軽量で加工性も良いため、航空機の部品などに使用されます。一方、A2017は強度が高く耐久性に優れており、構造材や工具部材に適しています。用途や条件に応じて適切なアルミ合金を選ぶことが重要です。
「A5056とA2017」プロジェクトに最適な材料は?用途と特性を比較検討
製品開発において、適切な材料を選択することは非常に重要です。特に、「A5056」と「A2017」という材料の違いや用途について比較検討することは、プロジェクトの成功に直結します。この記事では、どちらの材料が「A5056」と「A2017」というプロジェクトに最適なのか、その特性や用途に焦点を当てて解説していきます。製品開発に携わる方や材料選定に関心のある方にとって、興味深い情報が満載の内容となっています。
1. A5056とA2017の基本的な特性と違い
「A5056」と「A2017」の材料としての適用についての最適な選択はプロジェクトの要件によって異なります。A5056は抵抗力が強く、耐食性に優れているため、海洋環境や化学物質に晒される条件での利用に適しています。一方、A2017は加工性に富み、軽量でありながら高い強度を持つことが特徴です。このため、航空機の部品や自動車のフレームなど、重量削減が求められる用途に理想的です。例えば、船舶の建造にはA5056が選ばれることが多く、またA2017は多くの自動車メーカーによって選ばれています。結論として、各材料の特性を理解し、プロジェクトのニーズに合わせた選択が重要であると言えます。
2. A5056の地球温暖化への影響と資源循環
「A5056」と「A2017」という材料は、プロジェクトにおいてどちらが最適かという議論はよく行われます。結論から言うと、用途に応じて適切な選択をすることが重要です。例えば、A5056は強度と耐蝕性に優れており、航空機や自動車の部品に良く使用されます。対してA2017は、加工性が高く、やや強度は劣りますが、一般的な建築物や小型製品に適しています。具体的なプロジェクトを考慮に入れた場合、強度が求められる場合はA5056を選び、コストと加工性を重視するならばA2017が適していると言えるでしょう。最終的には、プロジェクトの要件に合わせ、両材料の特性を考慮して選択することが賢明です。
3. A2017の王子駅前まちづくり整備計画での利用可能性
A5056とA2017、これらはプロジェクトにおいてどのような材料として最適かという問いに答えるため、それぞれの用途と特性を比較検討することが重要です。A5056は耐食性に優れ、さらに溶接性や加工性にも秀でていますが、機械的強度はそこまで高くありません。逆にA2017は、軽量でありながら高い強度を持つことが特長ですが、耐食性には劣ります。例えば、A5056は化学プラントや食品工場など腐食性の強い環境下での使用に適していますし、A2017は航空機や自動車部品など、軽量かつ高強度が求められる分野で優れた性能を発揮します。したがって、王子駅前まちづくり整備計画においては、耐久性と加工性を重視するならばA5056、強度と軽量性を優先するならばA2017が選ばれるべき材料です。最終的には、計画の目的や具体的な条件に応じて、最適な材料選びが重要となるでしょう。
4. A5056とA2017を活用した市政経営の新展開
A5056とA2017は、それぞれ異なる特性を持つ素材であり、プロジェクトにおける適した素材の選定はその成功に不可欠です。A5056は耐食性に優れ、海辺の建築物や船舶などの素材として適しています。対してA2017は加工性が良いため、複雑な形状が要求される自動車部品や機械部品の製造に利用されます。例えば、A5056は海水にさらされやすい環境での使用を想定したプロジェクトには最適であり、長期的にも維持費を抑えることができるでしょう。一方、A2017は高度な加工が必要な場合に選ばれることが多く、その精密さが求められる場面では非常に価値があります。結論として、両素材は用途に応じてその特性が生かされるべきであり、プロジェクトごとに最適な素材を選ぶことが肝心です。
5. 手作りタルトシェルにおけるA5056とA2017の使用
プロジェクトにおいて最適な材料を選ぶ際には、その用途と特性を綿密に比較検討する必要があります。A5056とA2017は、それぞれ異なる特性を持つアルミニウム合金であり、用途に応じて適切な選択が求められます。A5056は、優れた耐食性と加工性を持つため、海洋環境や化学薬品にさらされる場所での使用に適しています。一方、A2017は強度が高いため、構造物の部材や高い強度が求められる機械部品に利用されることが多いです。例えば、手作りタルトシェルを作る際には、焼成中に膨張や収縮があるため、加工性と耐食性に優れるA5056が適材であると考えられます。結論として、それぞれの特性を考慮した上で、A5056は加工性や耐食性を重視する場面に、A2017は強度を最優先するケースに最適な材料です。
6. A5056とA2017のパラグアイでのダイズ栽培への応用
A5056とA2017、これらの材料選びがプロジェクトの成功を左右する。結論から言うと、用途に応じてA5056もしくはA2017が適している。A5056は耐食性に優れ、海洋構造物や化学プラントなど厳しい環境下での使用に適している。その一方でA2017は加工性が高く、自動車部品や建築材料など幅広い分野で利用されている。例えば、A5056は航空機の部材や船舶の内装材に使われることが多く、A2017は精密な機械部品や軽量な構造物の材料として重宝されている。これらの特性を理解し、プロジェクトの要件に合わせて適切な材料を選ぶことが肝要だ。最終的には、そのプロジェクトが最高の成果を上げるためには、用途と特性をしっかりと比較検討し、A5056かA2017のどちらかを選ぶべきである。
7. A5056とA2017材料の線虫発生生態への影響
プロジェクトにおける最適な材料を選択することは極めて重要です。特に「A5056」と「A2017」という二つの材料は、それぞれ異なる特性を持っています。A5056は高い耐食性と優れた加工性を有し、航空機や自動車の部品に適しています。他方、A2017は軽量でありながら強度が高いため、精密機器や電子部品に利用されることが多いです。具体例を挙げると、A5056は機械の外装に、A2017は内部のギアやフレームに使用されることがあります。結論として、プロジェクトにはその用途と必要とされる性質に合わせて、これらの材料の中から選択する必要があります。耐食性と加工性が求められる場合はA5056、軽量性と高強度が重視される場合にはA2017が最適であると言えるでしょう。
まとめ
A5056とA2017はどちらも航空宇宙産業に適した材料ですが、それぞれ異なる特性を持っています。A5056は耐久性に優れ、耐食性が高い一方、A2017は比較的軽量で加工性に優れています。用途に応じて適切な材料を選ぶことが重要です。
A5056とA2017の物性差:業界専門家が解説するアルミ合金の選択基準
アルミ合金は産業分野において広く使用されていますが、A5056とA2017の物性には何が違うのでしょうか?この記事では、業界専門家が解説するアルミ合金の選択基準についてご紹介します。もし製品開発や素材選定において悩んでいる方、異なる特性を持つA5056とA2017の比較に興味がある方にとって、この記事はきっと役立つことでしょう。
1. A5056とA2017の基本的な違いとは何か:アルミ合金入門
アルミ合金A5056とA2017は、それぞれ異なる特性を持っており、使用する分野によって選ばれるべき合金は変わります。A5056は耐食性に優れ、マリン用途や化学プラントなど厳しい環境下での使用に適しています。これに対してA2017は加工性に優れるため、自動車や航空機の部品など、精密な加工が求められる場面でよく用いられます。例えば、A5056は良好な耐海水性を活かして、船舶の部材や海洋構造物に利用されることが多いですし、A2017はその加工性と強度のバランスから、構造材料や複雑な形状が要求される部品製造に利用されています。結論として、A5056は環境耐性が求められる場合、A2017は加工性と強度が必要な場面で、それぞれの特性に合わせて選定することが重要です。
2. A5056の特性:中学数学で理解する合金の性質
A5056合金は、その耐食性に優れる特性から広く利用されています。一方、A2017合金は高い強度が特徴であるため、航空機材や精密機器など特定の用途に特化して使用されています。例えば、A5056は船舶の部材や海水に触れる構造物に用いられることが多く、その耐海水腐食性が求められます。一方でA2017は、高い機械的強度を必要とする航空機の構造部品に使われることがあります。よって、使用される環境や求められる性質によって、これら二つの合金の選択がなされるのです。結論として、アルミ合金A5056とA2017はそれぞれ独自の物性を持ち、これにより適した用途が異なることが専門家によって解説されています。
3. A2017の特性:等差数列を用いて解説するアルミの特徴
A5056合金とA2017合金は、その物性の違いから異なる用途に適しています。結論から言うと、A5056は耐食性に優れ、海洋関連の部品に適しているのに対し、A2017は高い強度が特徴で、航空機の部品などに用いられます。例えば、A5056は塩水に強いため、ボートや船舶の部材として使用されることが多いです。一方で、A2017は硬さと耐熱性を活かして、航空機のフレームや車両の部品としての使用が一般的です。どちらの合金もその特性を生かし、幅広い工業製品に不可欠な材料です。このように、A5056とA2017は使用される環境や要求される性能に応じて選択されるべきであり、それぞれの物性差が製品の性能や耐久性に直結するため、適切な選択が求められます。
4. A5056とA2017の化学的違いと数学的アプローチ
A5056とA2017の物性には、それぞれの用途に合わせた選択が重要です。A5056は海水や腐食性が高い環境に強い耐食性を持っているため、船舶や化学プラントの部材に使用されることが多いです。一方、A2017は高い機械的強度を持ち、航空機や自動車の部品などに適しています。例えば、船舶では外板にA5056が好まれる一方で、航空機ではA2017が骨格部分に使用されることがあります。このように、それぞれの物性の違いを理解し適切に選択することが、長期的な耐久性とコスト効率を考慮した材料選びには不可欠です。最終的に、アルミ合金を選ぶ際には、使用環境と必要とされる性質を照らし合わせ、最適な材料を選定することが求められます。
5. A5056とA2017の用途と適性:数学的思考で選ぶ合金材料
アルミ合金のA5056とA2017は、それぞれ特有の物性を有し、適した用途が異なります。A5056は、優れた耐食性を持ち、海洋環境や厳しい気候条件下でも使用されることが多いです。たとえば、船舶の建造や海洋構造物に利用されることが一般的です。一方、A2017は強度が高く、加工性にも優れているため、自動車や航空機の部品など、強度が求められる構造材料として幅広く使用されます。これらの特性を理解することは、最適なアルミ合金を選択する際に不可欠です。結論として、A5056は耐食性を重視する場合に、A2017は強度と加工性を求める際に選ばれるべき合金であり、目的に応じた適切な選択が求められます。
6. A5056 A2017 違いのまとめ:データ分析と数学的視点から
A5056合金とA2017合金は、アルミ合金選択において特性の理解が重要です。結論から言うと、A5056は優れた耐食性を持ち、A2017は加工性に優れています。A5056は海洋環境などの厳しい条件下でも使用できるため、船舶や高圧タンクなどに適している一方で、A2017は機械部品や自動車部品の加工に向いています。例えば、A5056は塩水に強いため船舶の建材として用いられ、A2017は易加工性を活かして精密な部品作成に用いられます。最終的には、これらの物性差を理解し適材適所に使用することで、それぞれの合金の長所を最大限に活かすことができるという結論に至ります。
まとめ
A5056とA2017はどちらも主に航空機や自動車部品などに使用されるアルミ合金ですが、その物性にはいくつかの違いがあります。A5056は耐食性に優れており、海水との接触に適しています。一方、A2017は強度が高いのが特徴であり、機械部品や溶接構造物に適しています。選択基準としては、使用目的に合わせた物性を考慮し適切な合金を選択することが重要です。
【アルミ合金比較】A5056とA2017、どのような違いがあるのか専門家が詳細に解説
アルミ合金の選択は、材料の特性や用途に合わせて慎重に行わなければなりません。A5056とA2017は、共に一般的に使用されるアルミニウム合金ですが、それぞれ異なる特性を持っています。この記事では、専門家による詳細な解説を通じて、A5056とA2017の違いについて理解を深めていきましょう。どの合金が特定の用途に最適なのかを知りたい方や、材料選択の際に迷っている方にとって、貴重な情報が得られることでしょう。
1. アルミ合金A5056とA2017の基本的な違い
アルミ合金A5056とA2017は、その成分と特性において重要な違いを持っています。A5056合金は、耐食性に優れ、特に海水に対して高い耐性を持つため、船舶や海洋関係の部品によく利用されます。これに対し、A2017合金は熱に強く、加工性が高い特徴を持ち、航空機や自動車の部品製造に適しています。たとえば、A5056は錆びにくい性質があるため、ヨットのマストや船体に使われることが多いです。一方でA2017は、その高い機械的強度のために、ロボットのアームや航空機のフレームなど、精密さと強度が要求される部分に使われることが多いです。結論として、これらの合金はそれぞれ特定の用途において優れた性能を発揮するため、適切な合金の選択が製品の品質と性能に直結すると言えます。
2. A5056 A2017 違いの化学成分と基礎データ
アルミ合金のA5056とA2017は、その用途と特性において異なる点があります。A5056は海水に強い耐食性を持ち、造船やマリン用品に適しています。これは、主にマグネシウムを5%以上含むことにより、優れた耐蝕性を発揮するためです。一方、A2017は銅を主要な合金元素としており、これによって強度が増すため機械部品や航空機の材料として用いられます。例として、A5056はより高い耐食性を活かして、海水の影響を受けやすい環境で使用される一方、A2017は強度が求められる自動車の部品や精密機器に使用されることが多いです。これらの違いを理解することで、適切なアルミ合金を選択することができるでしょう。最適な材料選定は、製品の性能を左右するため、非常に重要です。
3. A5056とA2017の特性と用途
A5056とA2017というアルミ合金は、それぞれ異なる特性を持っており、用途によって選ばれる材料が変わってきます。A5056は海水に強い耐食性を持ち、船舶やマリン用途などに優れた性質を発揮します。一方で、A2017は強度が高く加工性に優れており、航空機の部品や精密機器など、より強度が求められる分野で使用されます。具体例として、A5056はヨットのマストや船体の部品として、A2017は航空機の構造材料や自動車の部品として利用されています。これらの特性を理解し、用途に合わせたアルミ合金を選ぶことが重要です。最終的に、A5056はその耐食性から海に関連する用途に、A2017はその強度と加工性から機能性が求められる分野に適していると結論付けられます。
4. アルミニウム合金番号の意味とA5056 A2017の分類
アルミニウム合金のA5056とA2017は、それぞれ異なる特性を持っています。結論から言うと、A5056は優れた耐食性を持ち、海洋部品などに利用されることが多いです。一方、A2017は機械的性質が強く、高い加工性が求められる部品に用いられます。例えば、A5056は船舶の建材や化学プラントの部材に使われることが多く、塩水への強さを活かした用途に適しています。A2017は自動車や航空機の部品に利用され、高い強度と加工のしやすさから、精密な部品作りに役立てられています。最終的に、アルミ合金を選ぶ際には使用環境や必要な性質をしっかりと把握し、適した合金を選定することが重要です。
5. A5056 A2017 違いを考慮した設備部品の選び方
A5056とA2017のアルミ合金は、それぞれ特有の特性を有しており、用途に応じた選択が求められます。A5056は耐蝕性に優れ、海水にさらされる部品や耐食性が求められる環境での使用に適しています。一方、A2017は機械的性質が高く、強度と加工性のバランスが取れているため、航空機の部品や精密機器に多用されています。例えば、ボートの外装材や水中ロボットのフレームにはA5056が選ばれ、自動車のエンジン部品やロボットの関節部にはA2017が用いられることが多いです。したがって、環境や用途に応じて最適なアルミ合金を選択することが、製品の性能を最大限に引き出す鍵となります。
6. A5056 A2017 違いとAl-Si系合金との比較
アルミニウム合金のA5056とA2017は、用途や特性に応じて使い分けられる素材です。A5056は耐食性に優れ、海水にさらされる環境での使用に適しているのが特徴です。例えば、船舶やマリン用品に多く用いられます。一方、A2017はいわゆる硬質アルミニウム合金で、強度が要求される航空機部品や高張力ボルトなどに適しています。これらの違いは、それぞれの合金に添加されている元素の種類に由来しており、A5056にはマグネシウムが、A2017には銅が多く含まれています。従って、使用環境や耐久性の要件に基づき選択することが重要です。最終的には、それぞれの合金が持つ特性を理解し、適した用途に合わせて適切な選択をすることが、アルミ合金を用いる際の鍵となります。
7. A5056 A2017 違いとAl-Mg系合金との比較
アルミ合金A5056とA2017は、それぞれ特有の特性を持ち、異なる用途に適しています。A5056はアルミニウムに5%以上のマグネシウムを含む合金であり、海水や腐食性の強い環境に強い耐食性を持つことが知られています。これは、船舶や化学プラント等、厳しい環境下での使用が求められる部材に適用される例です。一方、A2017は銅を主要な合金元素とし、強度が高く加工性に優れているため、航空機の部品や精密機器の部品製造などに使用されます。この強度と加工性のバランスが、特に要求される分野での使用に適しています。結論として、A5056は耐食性を、A2017は強度と加工性を重視する場合に選ばれることが多いといえます。用途に応じた適切な選択が重要となるため、合金の特性を理解することが不可欠です。
8. 結論:A5056とA2017の選択における決定要因
A5056とA2017のアルミ合金は、それぞれ特有の特性を持ち、用途に応じて選ばれるべきです。A5056は耐食性に優れ、海洋関連の部品に適しています。しかし、A2017は機械的強度が高く、航空機や自動車部品によく使われます。たとえば、A5056は塩水にさらされる条件下でも優れた耐性を示すため、船舶の部品や海上構造物に用いられます。対照的にA2017は、加工硬化性が高いために、高い強度が求められる部位に使用されます。総じて、使用環境や必要とされる特性を考慮し、それぞれのアルミ合金の強みを活かす選択が重要です。この理解をもとに適材適所での利用を考えると、それぞれのアルミ合金はその価値を最大限に発揮するでしょう。
まとめ
A5056とA2017はどちらもアルミ合金ですが、それぞれに異なる特性があります。A5056は耐食性に優れ、溶接性も良い特徴があり、主に船舶や航空機の製造に使用されます。一方、A2017は強度が高く、熱硬化性もあるため、機械部品などの製造に適しています。用途や特性に応じて適切なアルミ合金を選ぶことが重要です。
【2023年版】A5052のフライス加工ガイド – 切削条件の最適化とは?
2023年版のA5052のフライス加工ガイドをお探しですか?本記事では、A5052のフライス加工における切削条件の最適化について詳しく解説します。A5052アルミニウム合金は、軽量で加工しやすい特性を持ち、幅広い産業で使用されています。このガイドでは、A5052のフライス加工における最適な切削条件や加工方法について、具体的なイラストを交えて分かりやすく解説します。A5052のフライス加工について知りたい方や切削条件の最適化に悩んでいる方にとって、このガイドは価値ある情報を提供することでしょう。
1. A5052 フライス加工の概要
A5052のフライス加工は、精密な加工が可能であり、そのために適切な切削条件の選定が必須です。A5052材は、その良好な機械加工性と耐食性から、多くの産業分野で利用されています。最適な切削条件を見極めることで、加工精度を高め、工具の摩耗を抑え、コストパフォーマンスを上げることができます。具体例として、切削速度や送り速度、切削深さを材質や加工形状に合わせて調整することが挙げられます。さらに、使用する工具の種類に応じて、冷却液の使用や、切削パスの最適化も重要です。結論として、フライス加工における最適な切削条件を見極めることは、A5052材の性質を活かし、高品質な製品を効率良く生産するための鍵となります。
2. A5052 フライス加工の切削条件の基本
A5052のフライス加工において、切削条件の最適化は極めて重要です。加工効率を高め、部品の品質を保ちながらコストを抑えるためには、適切なスピードとフィード率の設定が不可欠となります。例として、A5052は一般的なアルミニウム合金よりもやや硬く、加工には中間的なスピードが推奨されます。また、工具の摩耗を防ぐために、適切な冷却剤の使用も重要です。さらに、工具の種類や形状によっても適切な条件は変わってくるため、実際の加工前には事前試験を行うことも推奨されます。このように、A5052のフライス加工では、多くの要因を考慮した上で最適な切削条件を見極めることが、高品質な製品を効率的に生産する鍵となります。
3. フライス作業用切削工具の選定基準
A5052のフライス加工において、切削条件の最適化は製品の品質向上と効率的な生産に不可欠です。このアルミニウム合金は良好な加工性を持ちますが、適切な切削条件を見極めることが重要です。例えば、切削速度は材料の熱伝導率に合わせ中から高速で設定し、刃の摩耗を防ぐためには適切な潤滑が必要となります。また、工具の選定にあたっては、A5052の特性に合った刃先の形状やコーティングを選ぶことが肝心です。具体的には、刃の数が多く加工面が滑らかになるような工具を選び、切りくずの排出性も考慮する必要があります。このような最適化を行うことで、A5052のフライス加工は精度も向上し、生産効率も大きく改善されるでしょう。
4. 鏡面フライス加工システムの理解
2023年版A5052のフライス加工ガイドでは、切削条件の最適化が重要だと結論づけられています。その理由は、A5052というアルミ合金は、軽量かつ耐食性に優れているため、精密部品や航空機の部品など幅広い分野で使用されているからです。最適化された切削条件とは、適切な刃の速度や送り速度、冷却剤の使用など、フライス加工時の様々なパラメータの調節を指します。たとえば、A5052の切削には比較的低い刃の速度が推奨されることが一般的です。また、適切な切削油の使用は、仕上がりの質を高め長寿命化にもつながります。具体例として、ある工場では切削条件の見直しにより、仕上がり精度の向上と工具の摩耗減少を実現しました。結論として、切削条件を最適化することは、A5052フライス加工の効率と品質を大きく向上させるために不可欠であり、生産性の向上にも直結します。
5. 機械加工におけるA5052の特性と取り扱い
A5052のフライス加工における切削条件の最適化は、加工品質の向上とコスト削減に不可欠です。このアルミニウム合金は、軽量でありながら高い耐食性を有しているため、自動車や航空機の部品など幅広い用途で用いられます。最適な切削条件を見つけるためには、A5052の物性を理解し、適切な工具を選定することが重要です。例えば、炭素鋼用のカッターよりもダイヤモンドコーティングされた工具が推奨されます。また、高速での加工もA5052の良好な切削性を活かせますが、加工時の熱による変形を避けるためには適切な冷却方法を取り入れることが大切です。これらの点に留意し、試作を繰り返すことで、加工精度を高めつつ効率的な生産が可能になります。
6. トロコイダル加工とA5052の安定切削技術
A5052のフライス加工における切削条件の最適化は、高品質な製品を効率良く生産するために不可欠です。このアルミニウム合金は軽量でありながら高い耐食性を持ち、自動車や航空機の部品など幅広い用途に使用されています。最適な切削条件を見つけることは、ツーリングコストの削減と加工時間の短縮に繋がります。具体的な例としては、適切な切削速度の選定、使用するエンドミルの種類に応じた給送速度の調整、切削抵抗を考慮した深さや幅の制御などが挙げられます。これらの条件を最適化することにより、A5052材の耐性を損なうことなく、安定した加工を実現し、製品の品質を保つことができます。総じて、切削条件の最適化は加工効率の向上とコスト削減を実現し、競争力のある製品製造に寄与します。
7. A5052 フライス加工におけるトラブルシューティング
A5052のフライス加工では、切削条件の最適化により加工の品質と効率を高めることができます。最適化では、適切な切削速度、送り速度、切り込み深さを選定することが重要です。たとえば、切削速度が速すぎると工具の摩耗が早まり、遅すぎると加工時間が長くなるなど、不適切な条件設定は品質とコストの両面で損失を発生させます。また、A5052は一般的なアルミニウム合金であるため、潤滑液の選定にも注意が必要です。適切な潤滑を行うことで、切りくずの排出をスムーズにし、表面粗さを改善することができます。実際の加工例では、適切な潤滑液の使用により、加工品の表面品質が向上した事例が多く報告されています。結論として、A5052のフライス加工においては、切削条件の最適化が重要であり、そのための具体的な検討と試行錯誤が必要不可欠です。
8. A5052 フライス加工と切削液の役割
A5052のフライス加工において、切削条件の最適化は非常に重要です。これは、材質の特性上、A5052が比較的軟らかく、熱伝導率が高いため、適切な条件での加工が品質を決定するからです。具体的には、切削速度、送り速度、切削深さなどのパラメータを適正に設定することが重要です。例えば、高すぎる切削速度は材料の発熱を招き、精度を損なう恐れがあります。しかし、適切な速度であれば、滑らかな切削面を実現し、工具の摩耗も抑えることができます。このように、最適な切削条件を見極めることは、効率的かつ品質の高いフライス加工に不可欠であり、再度強調しますが、そのための知識と経験が要求されるのです。
9. A5052 フライス加工の経済性とコスト削減
A5052のフライス加工の経済性とコスト削減には切削条件の最適化が不可欠です。この合金は、加工性が良いため、適切な条件設定により、加工コストの削済と製品品質の向上を同時に達成することができます。例えば、適切な切削速度の選定は、工具の摩耗を抑え、長寿命化を実現し、結果としてコスト削減に寄与します。また、フライスの種類や切れ刃の角度の最適化も材料の負担を減らすことに繋がります。日本におけるA5052のフライス加工では、これらの要素を慎重に検討し、継続的な改善を促進することで、製造コストの低減と高品質な製品の供給が可能です。最適化の重要性を理解し、実践することは、製造業において競争力を維持する上での鍵となります。
10. まとめと次へのステップ
A5052のフライス加工においては、切削条件を最適化することが重要です。なぜなら、A5052はアルミニウム合金の中でも加工性が良好でありながら、不適切な条件で加工すると表面が傷つきやすくなるからです。具体的な例としては、切削速度の設定が挙げられます。適切な速度で切削を行うことで、材料の熱損傷を防ぎ、製品の品質を保つことができます。また、工具の選定や冷却剤の使用も、加工品質に大きく影響を及ぼします。最適な条件を見つけることは、時間とコストを節約し、より良い製品を生産するための鍵となります。結論として、A5052のフライス加工で優れた結果を得るためには、切削条件を慎重に選定し、継続的に最適化していくことが不可欠です。
まとめ
A5052はアルミニウム合金の一種であり、フライス加工に適した材料と言えます。この材料を効率的に加工するためには、適切な切削条件を設定することが重要です。適切な切削速度や送り速度、切削深さなどを最適化することで、作業効率を高めることができます。また、適切な切削液の使用や工具の選定も加工品質向上につながります。
【最新技術】A5052のフライス加工に適した工具と加工速度の選び方
加工業界では常に最新の技術や工具を使って効率的な加工が求められています。特にA5052のフライス加工においては、適切な工具と加工速度の選択が重要です。本記事では、A5052の特性やフライス加工に適した工具の選び方、加工速度について詳しく解説します。A5052のフライス加工にお悩みの方や最新技術を取り入れたい方にとって有益な情報となるでしょう。
1. A5052 フライス加工の基本概念
A5052のフライス加工では、適切な工具と加工速度の選定が重要です。これは、A5052のようなアルミ合金が、その優れた加工性により幅広い産業で使用されているため、効率的かつ正確な加工が求められるためです。具体的には、切削抵抗が低いカーバイド製のエンドミルや、高い切削能力を持つダイヤモンドコーティングの工具が選ばれることが多く、加工速度については、材質や厚みにより最適な速度が変動します。例えば、薄い材料や細かい加工を行う際には、より高速な回転が必要ですが、厚みがある場合は速度を落とし、切削負荷を調整することが重要となります。最適な工具と加工速度を選ぶことで、A5052の可能性を最大限に引き出し、製品の品質を保つことができます。
2. A5052Pの物性と加工の関連性
A5052のフライス加工に際しては、適切な工具選びと加工速度の設定が重要です。なぜなら、材料の特性に合った選択をすることで加工精度が向上し、工具の寿命を延ばすことができるからです。例えば、アルミニウム合金のA5052は、加工性に優れている反面、熱伝導率が高いため、切削時には工具の発熱を効率的に逃がす工具が推奨されます。また、切削速度も材質に適した範囲で選ぶ必要があります。A5052の場合は、高速での切削が可能ですが、適切な速度を見極めることで仕上がりの品質を確保することができます。したがって、A5052材を加工する際は、熱に強いコーティングが施された刃物を選び、かつ適切な切削速度に設定することが肝要です。これにより、高精度なフライス加工を実現し、生産性の向上に繋がるのです。
3. 最新工作機械技術の概要とA5052 フライス加工
A5052のフライス加工において最適な工具選びと加工速度の設定は重要です。結論から言うと、特定の工具と加工速度を選ぶことにより、加工精度や効率を大幅に向上させることができます。A5052は、その優れた加工性と耐食性から、自動車や航空機の部品など幅広い分野で使用されるアルミニウム合金です。適切な工具を選ぶには、材料の硬度や切削抵抗に合った刃の材質と形状を考慮する必要があります。具体的には、超硬合金やダイヤモンドコーティングされた工具が好まれ、加工速度についても、A5052の場合は中高速の範囲で効率よく加工するのが一般的です。実際に、精密な部品を効率良く生産した事例が多数報告されています。最終的には、試作を繰り返し、その中から最適な条件を見つけることが肝心です。
4. 中国の工作機械産業の動向とA5052 フライス加工への影響
A5052のフライス加工における最適な工具選びと加工速度の設定は、加工効率と品質を大きく左右します。A5052は、その耐食性や加工性の良さから、多くの工業分野で使用されているアルミニウム合金です。適切な工具を選ぶには、刃の材質や形状が重要であり、例えば、超硬合金製の工具は耐久性に優れ、精密な加工が可能です。また、フライス加工においては、加工速度の選定も重要で、A5052の場合、高速での加工が可能でありながら、品質を損なわないようなバランスを見極める必要があります。具体的な加工速度は、工具の仕様や加工機の能力、製品の要求品質によって決定されます。このように適切な工具と加工速度を選ぶことで、A5052のフライス加工は効率よく、かつ高品質な結果をもたらすでしょう。
5. 工作機械業界の最新トレンド
A5052のフライス加工における工具選定と加工速度の決定は、最適な加工効率と仕上がり品質を実現するために重要です。このアルミニウム合金は優れた耐食性と加工性を持ちますが、適切な工具や加工速度を選ばないと、加工時に欠陥が発生する可能性があります。例えば、切削速度が速過ぎると、材料が熱を持ちすぎてしまい、ツールへの負荷が過大になることがあります。逆に遅すぎると、加工効率が低下し、工具の摩耗が早まることがあります。適切な工具を選ぶ際には、A5052の物理的特性に合わせた切削工具が必要で、例えば、ダイヤモンドコーティングされたエンドミルなどが適しています。このように、A5052のフライス加工に適した工具と加工速度を選ぶことで、効率的かつ高品質な加工が可能になります。
6. 立形5軸と立形彫の新型機械とA5052 フライス加工
A5052のフライス加工に最適な工具と加工速度の選び方については、加工の品質と効率を左右する重要な要素です。A5052は、アルミニウム合金の一種であり、その特性上、耐食性と加工性が良好であることから、多くの産業で利用されています。適切な工具を選ぶ際には、切れ味が良く、長寿命であることが求められます。特に、超硬エンドミルやダイヤモンドコートエンドミルが推奨されることが多いです。また、加工速度に関しては、A5052の熱伝導性を考慮し、高速でありながらも工具や素材が過熱しないような範囲で設定することが重要です。具体的には、切削速度と送り速度をバランス良く設定し、精密な加工を実現することができます。結論として、A5052のフライス加工には、耐摩耗性に優れた工具の選択と、高い加工速度を保ちつつ素材の特性に合わせた速度設定が不可欠であり、これにより加工精度の向上と効率的な生産が実現されるのです。
7. A5052 フライス加工における工具選択の重要性
A5052のフライス加工において、適切な工具と加工速度の選択は、製品品質の向上に不可欠です。とりわけ、A5052というアルミニウム合金は、その優れた加工性と耐食性から、多様な産業で使用されています。この合金の加工に最も適した工具は、硬度と耐摩耗性に優れる超硬合金やダイヤモンドコーティング工具です。例えば、高速度で精度良く加工する際には、ダイヤモンドコーティング工具が適しており、摩耗を抑えながら、長寿命を保証します。また、適切な加工速度を見極めることは、工具の負担を減らし、製品の仕上がりを良好に保つ鍵となります。実際の加工例を見ても、精度を求められる部品では低い速度で丁寧に、大量生産を要する場合には、より高速な加工が求められる傾向にあります。このように、A5052をフライス加工する際は、工具選びと加工速度の見極めによって、最終的な製品品質に大きく影響を及ぼすため、慎重な選定が求められます。
8. A5052 フライス加工の最適な加工速度の決定方法
A5052のフライス加工に最適な工具と加工速度の選び方は、加工効率と仕上がり品質に大きな影響を与えます。A5052はアルミニウム合金の一種で、その特性に合った工具選びが必要です。例えば、専用の切削工具を使用することで、摩耗を減らし長寿命を保つことが可能です。また、適切な加工速度の設定により、切削抵抗を最小限に抑えることで、加工時の精度を高めることができます。具体的には、工具の材質や刃の数、A5052の厚みに応じて、速度を調整します。例として、細かい仕上がりが求められる場合は、低速で丁寧な加工を行います。逆に、大量生産で精度よりもスピードが求められる時は、高速加工が適しています。適切な工具と速度の選定は、A5052のフライス加工において、効率的かつ高品質な製品を実現する鍵となるのです。
9. A5052 フライス加工に関するよくある質問
A5052のフライス加工に適した工具や加工速度の選び方は、最適な加工品質と効率を実現するために重要です。A5052はアルミニウム合金で、その特性から一般的な切削工具ではなく、アルミニウム専用の切削工具を選ぶことが推奨されます。特に、ダイヤモンドコーティングされた工具はA5052の加工において良好な仕上がりを提供します。また、適切な加工速度は材料の質を保ちつつ、効率的な加工を可能にします。一般的に高速度で加工を行うことができるものの、過度に速い速度は工具の摩耗や製品の損傷に繋がる可能性があるため注意が必要です。実例として、工具メーカーはA5052の加工に最適な速度範囲を推奨しており、これを参考にすることが望ましいでしょう。このように工具選びと加工速度の適切な合わせ技により、A5052のフライス加工は効率的かつ高品質な結果を得ることが可能です。
まとめ
A5052のフライス加工に適した工具は、高硬度の切削工具が求められます。特に多くの刃を持つエンドミルが効果的であり、高速での加工が可能です。また、加工速度の選び方は材料の硬さや工具の材質によって異なりますが、適切な切削条件を設定することが重要です。
A5052素材を使ったフライス加工:工程の効率化と品質向上の秘訣
アルミニウム合金A5052は、その耐食性や耐久性の高さから様々な産業で広く使用されています。特に、機械部品の加工において、A5052は非常に重要な材料となっています。本記事では、A5052素材を使用したフライス加工に焦点を当て、工程の効率化と品質向上の秘訣について紹介します。フライス加工におけるA5052の特性や加工方法、工程の最適化などについて詳しく解説しますので、興味をお持ちの方はぜひご覧ください。
1. A5052 フライス加工とは?
A5052素材を使ったフライス加工は、製造業における効率化と品質向上に寄与しています。この素材は、優れた加工性と耐食性を持つため、航空機の部品から一般消費財まで幅広い用途で利用されています。特に、フライス加工においては、その優れた機械的性質が最大の利点となっており、精密な部品製造に不可欠です。例として、A5052を用いたフライス加工によって生産される部品は、その均一な表面処理と高い寸法精度により、最終製品の品質向上に大きく貢献しています。このようにA5052素材を活用することは、生産効率の向上だけではなく、製品の信頼性を高めることにも繋がります。総じて、A5052素材はフライス加工の分野で重要な役割を担い、工程の効率化と製品品質の向上の両方を可能にしています。
2. A5052 フライス加工の基本
A5052素材を使ったフライス加工は、その耐食性と加工性の良さから、工程の効率化と品質向上に貢献しています。A5052はアルミニウム合金の一種で、特に耐海水性に優れるため、船舶や化学プラントなどの部品製造に適しています。この素材を用いることで、切削抵抗が低くなり、工具の摩耗も少なくなるため、より精密な加工が可能となります。例えば、A5052を使用したフライス加工では、一貫した加工精度を維持しつつ、生産効率を上げることができます。また、仕上がりの品質も向上し、製品の信頼性が増すというメリットもあります。よって、A5052素材の選択は、高品質な製品を効率的に生産するうえでの秘訣と言えるでしょう。
3. 化合物熱電材料とA5052 フライス加工
A5052素材を使ったフライス加工は、工程の効率化と品質向上に大きな役割を果たしています。この素材は、強度と加工性のバランスが取れているため、様々な産業での利用が見受けられます。具体的には、A5052は航空機の部品や自動車の部材としての使用が一例です。フライス加工においては、この素材は優れた切削性を持ち、精密な加工が可能です。また、長期にわたる使用においても、耐食性に優れるため、製品の耐久性を保つことができます。このようにA5052素材は、フライス加工における効率化と高品質な製品製造に寄与しており、多岐にわたる産業での需要が高まっているのです。最終的には、A5052を採用することで、コスト削減と製品の信頼性の両方を実現することができるため、重宝されています。
4. フライスカッター構造と工具の長寿命化
フライス加工においてA5052素材は、工程の効率化と品質向上に大きく寄与しています。A5052とは、優れた耐食性と加工性を持つアルミニウム合金であり、フライス加工に最適な材料の一つです。この合金を使用することで、カッターの長寿命化が図られ、結果として工具交換の回数が減少し、生産効率が向上します。例えば、A5052を用いたフライス加工では、切削抵抗が低減されるため、加工面の仕上がりが滑らかになります。また、耐食性に優れているため、長期にわたって製品の品質を維持することが可能です。これらの特徴により、A5052を用いたフライス加工は、航空機や自動車などの精密部品製造において、その有効性が高く評価されています。再度結論として、A5052素材を使用することで、工程の効率化と品質向上が可能となり、製造業における競争力の強化に寄与します。
5. 6面フライス加工 vs 4面フライス加工:手順と違い
A5052素材を使用したフライス加工は、工程の効率化と品質向上の秘訣です。このアルミニウム合金は、優れた加工性と強度を兼ね備えており、精密な部品製造に適しています。例えば、航空機の部品や自動車の部品など、高い信頼性が求められる製品に頻繁に利用されています。A5052素材を用いることで、工具の摩耗が少なくなり、加工中の材料の安定性が高まります。結果として、不良品の発生率が下がり、製品の品質が向上します。また、素材が持つ優れた加工性によって、加工時間が短縮され、コストパフォーマンスも向上するのです。このように、A5052素材を選択することは、加工の効率と製品の品質の両方を高める重要な要素となっています。
6. 複合加工機を用いたA5052 フライス加工の効率化
A5052素材を使ったフライス加工は、製造業における効率化と品質向上のカギを握っています。特に、その強度と耐食性から、A5052は航空機や自動車などの部品製造に広く採用されています。フライス加工における工程の効率化は、時間とコストの削減に直結し、スピーディな生産サイクルを実現します。例えば、多機能工作機械を用いることで、複数の工程を一つの機械で完結させることが可能となります。これは工程間の移動時間の短縮だけでなく、加工精度の向上にも寄与し、ひいては製品品質の一貫性を保つことにつながります。結果的に、A5052素材の特性を活かした高品質な製品を、より効率的に生産することが可能となり、市場競争力を強化します。
まとめ
A5052素材を使用したフライス加工は、工程の効率化と品質向上を実現するために重要です。A5052は耐食性、機械的性質、溶接性に優れた素材であり、これにより加工性が向上します。また、切削油の種類や刃具の選定、加工条件の最適化などの工夫によって、高い加工効率と品質を実現できます。フライス加工においてA5052素材を使用する際には、これらの秘訣を活用することで、より良い加工結果が期待できます。
A5052 アルミ合金のフライス加工 – 効率的な方法と注意点
アルミ合金のフライス加工に興味はありますか?A5052というアルミ合金は、その軽さと耐食性から幅広い産業で使用されています。この記事では、A5052アルミ合金のフライス加工に焦点を当て、その効率的な方法と注意点について紹介します。フライス加工の基本から応用まで、まだ知られていない情報を知ることができます。さらに、A5052アルミ合金に特化した上級テクニックも取り上げます。もしあなたがこの分野に興味を持っているなら、ぜひこの記事を読んでみてください。
1. A5052 フライス加工の基礎
A5052アルミ合金のフライス加工は、その優れた加工性と経済性から、幅広い工業分野で注目されています。フライス加工においては、まず切削条件の選定が重要で、これには合金の種類や硬さなどの材質、加工する形状、精度要求等を考慮する必要があります。特にA5052アルミ合金は、良好な切削性を活かすために適切な切削速度と送り速度の選定が肝心です。例えば、一般的なフライス加工では、A5052アルミ合金の場合は高い切削速度を適用することが多いですが、過度な速度は切削熱の増加や工具の摩耗を早める可能性があります。また、均一な表面仕上げを目指す場合には、工具の選択にも注意が必要です。加工面の質を左右するこれらのポイントを適切に管理することで、A5052アルミ合金のフライス加工はより効率的かつ精密に行えるのです。これらを踏まえた上で加工を進めることで、A5052アルミ合金のフライス加工は、高品質かつ高効率な結果をもたらすでしょう。
2. A5052 アルミ合金の特性と加工の利点
A5052アルミ合金のフライス加工はその高い効率と加工のしやすさから、多くの産業分野で利用されています。この合金は優れた耐食性と加工性を持つため、航空機や自動車の部品として広く採用されているのです。具体的には、A5052は一般に良好な成形性を有し、特に冷間加工に適しています。そのため、複雑な形状の部品を作成する際にも均一な仕上がりが期待できます。しかしながら、フライス加工を行う際には、適切な切削速度や冷却剤の使用、ツールの選択に注意を払うことが重要で、これにより加工時の歪みや表面の傷を最小限に抑えることが可能です。結論として、A5052アルミ合金のフライス加工は効率的で高品質な部品製造を可能にしますが、その特性を十分理解し、適切な加工条件を選定することが成功の鍵となります。
3. コスト削減のためのA5052 フライス加工戦略
A5052アルミ合金のフライス加工は、その優れた加工性とコスト効率から、工業用途に広く利用されています。この合金の効率的な加工を実現するためには、適切な切削条件の選定が不可欠です。例えば、切削速度や送り速度、切削液の選定によって、工具の摩耗を抑えつつ、高い精度の加工を行うことができます。また、A5052合金特有の熱伝導性を考慮した工具の冷却方法の工夫も重要です。効率的な加工を行う上での注意点としては、合金成分や材料の状態によって加工性が異なることが挙げられ、そのためには予め材料の特性を理解し、適切な加工条件を見極める必要があります。適切な加工の進め方を行うことで、コスト削減に繋がり、製品の品質向上にも寄与するため、フライス加工戦略は非常に重要です。
4. A5052 フライス加工用の適切なツール選択
A5052アルミ合金のフライス加工は、その耐食性と加工性の良さから多くの工業分野で利用されています。適切なツールを選択することで、加工効率が大幅に向上し、製品品質も安定します。例えば、A5052合金の加工には、切削抵抗が低く長寿命である超硬合金製のエンドミルが推奨されます。これにより、切削速度を上げることができ、加工時間の短縮とコスト削減に繋がります。しかし、適切な冷却剤の使用や、チップの交換頻度を適切にするなど、注意点も多々あります。最終的に、適切なツール選択と加工条件の最適化が、A5052アルミ合金のフライス加工の鍵を握ります。正しい知識と技術で品質と効率の両立が可能になります。
5. A5052 フライス加工における切削液の活用
A5052アルミ合金のフライス加工は、適切な切削液の使用により、工具の摩耗を抑え、加工精度を高めることが可能です。この合金は良好な加工性を持ちながらも、硬質なため工具への負担が大きいという特徴があります。そのため、冷却潤滑剤として切削液を活用することで、工具と材料の摩擦を減少させ、発熱を抑制します。たとえば、適切な切削液を用いることで、長時間の作業においても切削速度を保ちつつ、工具の耐久性を向上させることができます。さらに、切削液は切りくずの除去にも役立ち、これにより加工面の仕上がりを改善することができるのです。最終的には、切削液を適切に活用することで、A5052アルミ合金のフライス加工を効率的かつ高品質に行うことが可能になります。
6. A5052 フライス加工のための安定した作業手順
A5052アルミ合金のフライス加工は、その優れた機械的特性と加工のしやすさから、産業界で広く採用されています。適切な方法で加工を行うことは、製品の品質を保証する上で非常に重要です。具体的には、適切な切削速度の選定、使用する工具の選択、冷却剤の利用などが挙げられます。たとえばA5052の場合、その特性を生かすためには鋭い刃を持つ工具を使い、適切なフィードレートとスピンドル速度で加工することが推奨されます。さらに、加工中の発熱を抑えるための冷却剤の適切な使用は、工具の摩耗を減らし、仕上がりの質を高めると共に、長寿命化にも寄与します。以上の点に注意してフライス加工を行うことで、A5052アルミ合金はその潜在能力を最大限に発揮し、精度の高い部品製造に貢献することができるのです。
7. A5052 フライス加工に関するよくある問題と解決策
A5052アルミ合金のフライス加工は、その耐食性や加工性の良さから工業分野で広く用いられる技術です。適切な手法を用いれば、加工効率を大幅に向上させることが可能ですが、注意が必要です。例えば、A5052合金の特性を十分理解した上で、適切な切削工具や切削条件を選択することが肝要です。適正な切削速度や送り速度を見極め、工具の摩耗を常にチェックし、冷却液の使用も適切に行うことで、精度の高い加工が実現します。また、フライス加工においては、加工時に生じる振動にも注意が必要で、これを適切に管理することで、仕上がりの品質を保ちつつ、工具の耐久性も高めることができます。最適なフライス加工方法と注意点を理解することで、A5052合金を用いた製品の製造効率と品質を同時に高めることができるのです。
まとめ
A5052アルミ合金のフライス加工は、適切な切削条件と工具選択が重要です。切削速度や切り込み量、適切な切削油の使用などの工程を工夫することで効率的に加工することが可能です。また、切削熱による変質を抑えるために、十分な冷却を行うことも重要です。加工の際には、刃先が過度に摩耗しないように注意が必要です。