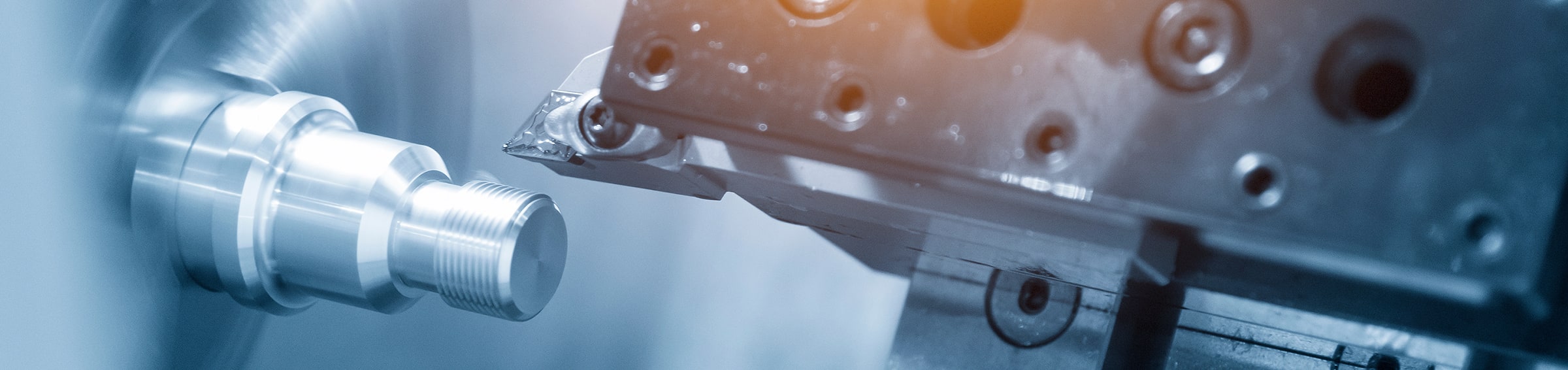
コラム column
【加工屋さん必読】A5052アルミの品質向上を図る切削テクニック
A5052アルミの品質向上を図る切削テクニックについて知っていますか?本記事では、A5052アルミの切削加工における品質向上のためのテクニックについて解説しています。A5052アルミを使った加工において、切削加工がどのように品質向上につながるのか、具体的な方法や注意点について詳しく紹介しています。A5052アルミの切削加工に興味がある方は、ぜひご覧ください。
1. A5052 切削加工の基礎知識
A5052アルミ合金の切削加工を行う際には、品質向上のためいくつかのテクニックがあります。まず、このアルミ合金は耐食性と加工性が高く、多くの加工屋さんに利用されていますが、適切な方法で加工しなければ、その優れた特性を生かすことができません。例えば、切削速度の最適化、適切な切削液の選択、そしてツールの状態を常に良好に保つことが重要です。具体的には、高速での粗切削を行い、仕上げ切削では低速に切り替えることが品質向上に繋がります。また、A5052アルミ合金の切削においては、非鉄金属用の切削液を使用することで、切削性能を高め、工具の寿命を延ばす効果が期待できます。最適な加工条件のもとで切削を行うことで、A5052アルミ合金の品質を向上させ、より良い製品作りに寄与することができるのです。
2. A5052 切削加工における表面層の重要性
A5052アルミニウム合金の切削加工は、品質向上が求められる分野であることから、その技術の精度を高めることは非常に重要です。この合金は、軽量かつ耐食性に優れた素材であるため、航空機や自動車など幅広い産業で利用されています。品質を左右する大きな要素の一つに、切削加工によって生じる表面層の性質があります。適切な切削条件を見極め、表面粗さを最適化することで、耐久性や耐食性が飛躍的に向上します。例えば、切削速度や送り速度、工具の選択など細かなパラメータの調整により、加工面の微細な損傷を減少させることが可能です。また、冷却液の適切な使用も、加工時の熱影響を抑制し品質向上に寄与します。まとめると、A5052アルミの切削加工においては、表面層の性質を理解し、適切な切削条件を見極めることが品質を大きく左右するため、技術者はこれらの点に注意を払う必要があります。
3. A5052 切削加工とDIJETターニングツールの関係
A5052アルミの品質向上を図る切削加工には、適切なテクニックが必要不可欠です。この素材は強度と耐食性に優れていますが、加工時には工具の選定や切削条件が品質に直結します。例えば、DIJETのターニングツールは、切削速度の安定化や長寿命が期待され、A5052の加工に適しているとされています。このような高精度な工具を使用することで、素材固有の性質を損なわず、かつ精度の高い加工が可能となります。その結果、切削面の仕上がりが向上し、製品の品質が一層高まるのです。したがって、A5052アルミを加工する際には適切な工具を選び、正しいテクニックを用いることが品質向上の鍵となります。
4. アルミニウムA5052の機械加工の最新動向
アルミニウムA5052は、その加工性の良さから多くの加工屋さんに重宝されています。しかし、加工技術が品質向上の鍵を握ることは明白です。特に、切削加工においては、精密な技術が求められるため、より良い製品を作るための方法として以下のテクニックが挙げられます。まず、適切な切削液の使用は、工具の摩耗を減少させ、長寿命化を図る上で非常に重要です。また、適正な切削速度と送り速度の選定は、A5052の持つ特性を最大限に生かしながら、精度の高い加工を可能にします。具体例としては、微細なバリの発生を防ぐために、切削工具の選定にも気を配ることが重要です。締めくくりとして、これらの技術を駆使することで、A5052アルミニウムの加工精度は大きく向上し、より品質の高い製品製造に繋がるのです。
5. ZXコートUPMILLシリーズによるA5052の加工効率化
A5052アルミは、その優れた加工性により幅広い加工屋さんにとって重宝がられています。しかしながら、より品質を向上させる切削テクニックを理解することが、製品の精度向上に不可欠です。具体的には、ZXコートUPMILLシリーズのエンドミルを使用することで、A5052の切削加工における効率と仕上がりが格段に向上します。このエンドミルは、特殊なコーティングが施されており、アルミの粘着による刃物の摩耗を防ぎつつ、滑らかな切削を実現します。また、エンドミルの形状もA5052の切削特性に合わせて最適化されているため、余計なバリの発生を抑え、加工面の精度を高めます。このようにZXコートUPMILLシリーズを利用することは、A5052アルミの品質を向上させるための効果的な手段であり、加工屋さんにとっては大きなメリットとなります。
6. 切削工具の選定とA5052 アルミニウムの加工性
A5052アルミニウムの品質向上には適切な切削工具の選定が不可欠です。この合金は加工性が高く、器具や部品の製造に広く使用されています。しかし、工具が不適切だと仕上がりの精度に影響を及ぼすだけでなく、材料の無駄遣いにもつながるため、適正な切削工具の選定は生産性を左右する重要な要素となります。例えば、刃の形状や材質、コーティングの種類によって、切削時のアルミニウムの発熱量や粉塵の発生量が大きく変わります。また、工具の刃の数や回転速度の調整も、A5052のようなアルミ合金の加工時には品質向上に不可欠です。最適な工具を選ぶことで、精度の高い加工を実現し、材料の無駄を減らし、生産効率の向上にも寄与します。結局のところ、A5052アルミニウムの加工において品質を高めるためには、切削工具の選定に妥協しないことが重要です。
7. ソリッドエンドミルとA5052 切削加工の組み合わせ
A5052アルミニウム合金の加工において、品質を向上させることは業界全体の目標です。そのためには、適切な切削テクニックが必要不可欠です。例えば、ソリッドエンドミルはA5052の加工に特に適しており、その組み合わせは、精度の高い仕上がりを実現します。この工具を使用することで、材料の硬度に適応し、加工中の振動を抑制し、より滑らかな表面を作り出すことが可能になります。さらに、適切な切削速度と送り速度の設定により、切削抵抗を最適化し、工具の寿命を延ばすこともできます。このようなテクニックを駆使して、A5052の品質を向上させることは、加工屋さんにとって重要です。結論として、適切な工具の選択と切削条件の最適化により、A5052アルミの加工品質は飛躍的に向上します。
8. A5052 切削加工におけるトラブルシューティングと対策
A5052アルミの切削加工時に品質向上を実現するためには、適切なテクニックが必要です。この合金はその優れた可塑性と耐食性により、自動車や航空機の部品など、多くの産業で利用されています。しかし、その柔軟性が原因で切削時にはバリが発生しやすかったり、仕上がりの精度に影響を及ぼすことがあります。こうした問題を解決するためには、刃の進行速度や送り速度を調整すること、適合する潤滑油の使用、切削工具の選択に気を使うことなど、具体的な対策を講じる必要があります。加えて、仕上げには充分な時間をかけ、必要に応じて後工程での研磨を行うことが望ましいです。これらのテクニックを駆使することで、A5052アルミの加工品質は格段に向上し、より高品質な製品を提供することが可能になります。
9. A5052 切削加工プロセスの最適化と工程管理
A5052アルミニウム合金はその優れた加工性と耐食性により、幅広い産業で使用されています。しかし、品質向上のためには適切な切削テクニックが不可欠です。例えば、切削速度や送り速度の最適化、適切な冷却液の使用は加工時の変形を防ぎ、より高精度な製品を生産する上で重要です。また、工具の選定にも注意が必要で、A5052の性質に合った刃物を使用することで、摩擦や切削抵抗を減らし、工具の摩耗を抑えることができます。さらに、加工後のバリ取りや表面処理を丁寧に行うことで、製品の品質を一層高めることが可能です。これらのテクニックを駆使して品質向上を図ることで、我々はより信頼性の高い製品を提供し得るのです。
10. A5052 切削加工の未来:革新的技術と展望
A5052アルミニウム合金は、その優れた加工性能と耐食性により、幅広い産業で利用されています。品質向上のためには、適切な切削テクニックが必要不可欠です。具体的には、切削速度や送り速度、工具の選択に注意を払うことで、加工面の精度を高め、工具寿命を延ばすことが可能です。さらに、切削液の適切な使用は、発熱を抑え、製品の品質を向上させます。例えば、ある加工屋さんでは、これらのテクニックを駆使し、製品の表面粗さを大幅に改善することに成功しました。その結果、顧客満足度の向上とリピート率の増加が見られました。このように、適切な切削テクニックの実践は、A5052アルミの品質を向上させるだけでなく、ビジネスの成功にも直結するのです。
まとめ
A5052アルミの切削加工において品質向上を図るためには、適切な切削テクニックを採用することが重要です。適切な切削速度や刃具の選定、切削液の使用などがポイントとなります。また、適切な工具の選択や刃物の状態管理によって加工精度を向上させることが可能です。品質向上を図るためには、熟練した加工技術や最新の切削技術を取り入れることが重要です。
【現場の効率化】A5056の切削加工時間を短縮する方法
今日の現場では、効率化がますます重要視されており、A5056の切削加工時間を短縮する方法に関心が集まっています。A5056は高強度のアルミニウム合金であり、その切削加工は慎重な計画と適切な方法が必要です。この記事では、A5056の切削加工における効率化のポイントやコツについて解説します。A5056の切削加工に携わる皆さんは、ぜひこの記事を参考にして、作業効率の向上に役立ててください。
1. A5056切削加工の基礎知識
A5056の切削加工時間を短縮することは、製造コストを削減し効率を向上させる重要な要素です。そのためには、適切な切削条件の選定が不可欠です。例えば、切削速度、送り速度、切り込み深さを最適化することにより、一回の加工でより多くの材料を効率的に除去できます。具体的には、A5056の材質特性に合わせた刃具の選定が、加工時間の短縮に貢献します。また、CAD/CAMソフトウェアを利用した加工プログラムの事前シミュレーションによって、無駄な工程を削減し、よりスムーズな切削パスを実現することも有効です。これらの改善策を講じることで、A5056の切削加工時間を短縮し、製造現場の効率化に寄与することができます。
2. 工数削減のためのA5056切削加工事例紹介
A5056の切削加工時間を短縮することは、生産効率を高め、コスト削減に直結します。そのためには、切削条件の最適化が非常に重要です。例えば、適切な刃の選定や、切削速度の調整を行うことで、加工時間を削減できる場合があります。具体的には、刃の形状が切削抵抗を低減させ、材料の除去率を上げる設計を選ぶこと、また、高速度鋼や超硬材料を使用した工具を使用することで、より速い切削速度での加工が可能になります。工具メーカーから提供されるカタログや専門家の知見を参考に、A5056の特性に合った最適な工具と加工条件を選定し、試作と改善を繰り返すことが効率化の鍵となります。こうした取り組みにより、切削加工時間の短縮を実現し、生産性の向上に寄与することが可能です。
3. A5056切削加工における環境改善策
A5056の切削加工の効率を向上させることは、生産性を高める上で重要です。そのためには、まず適切な工具の選択が必要不可欠です。具体的には、A5056に最適化された切削工具を使用することで、摩耗を減らし、加工時間の短縮に寄与します。例えば、超硬材質で作られたエンドミルは、耐久性に優れており、精度の高い加工が期待できるため、A5056のようなアルミニウム合金の加工に適しています。また、切削液の選定も重要で、適切な切削液を用いることで工具の冷却と潤滑が得られ、切削抵抗を下げることができます。このように工具と切削液の最適化を図ることで、A5056の切削加工時間を有効に短縮することが可能です。
4. A5056切削加工不良の原因と対策
A5056の切削加工時間を短縮することは、製造業におけるコスト削減に直結します。この合金の加工においては、工具の選定や切削条件の最適化が重要となります。例えば、高速度鋼や超硬合金を使用した工具は、耐久性と効率性を向上させ、加工時間の短縮に寄与します。また、適切な切削速度や送り速度の設定は、加工面の仕上がりを良くし、再加工の必要性を減少させます。さらに、最新のCNC技術を取り入れることで、作業の自動化と精度の向上が期待でき、結果として加工時間の削済みに繋がります。これらの方法を組み合わせることで、A5056の切削加工時間の短縮が実現し、生産性の向上に貢献します。
5. 切りくず搬送・処理装置の役割と効率化
A5056の切削加工時間の短縮は、生産効率の向上に直結します。具体的な理由として、切削加工時間が短縮されると、それに伴い機械の稼働時間が減少し、電力消費が抑えられるため、経済的なメリットが生まれます。また、加工待機時間の短縮によって、次の工程への移行が迅速になり、全体の生産性が向上します。実際に、A5056の加工時間短縮を実現するため、刃物の材質の見直しや、最適な切削条件の検証、さらには切削液の改善などが試みられています。これらの取り組みにより、工具の摩耗が抑えられ、正確な加工を継続できるため、加工精度の向上にも寄与します。結論として、A5056の切削加工時間を短縮することは、コスト削減と生産性向上の両面で企業にとって重要な施策であり、積極的な取り組みが求められます。
6. 高能率A5056切削加工技術の展望
A5056の切削加工時間を短縮することは、製造業における生産性向上に直結します。理由は、素材の特性に応じた最適な加工方法を見極めることで、無駄な工程を削減し、コストと時間の節約につながるためです。例えば、A5056のようなアルミニウム合金は、適切な切削液の使用や適正な切削速度の選定により、加工時間を大幅に短縮できることが知られています。また、専用の工具を用いることで素材への負担を減らし、耐久性を高めることができるため、長期的な視点で見ても効率が良くなります。これらの方法を踏まえると、A5056の切削加工における時間短縮は十分に可能であり、それは生産性の向上に大きく寄与するでしょう。
7. 工具費用の低減に向けたA5056切削加工の工夫
A5056の切削加工時間を短縮することは、生産性の向上に直結します。この目的を達成するためには、適切な工具の選択と加工パラメータの最適化が重要です。例えば、特定の材料に対応したコーティングが施された切削工具を用いることで、耐久性が向上し、工具交換の頻度が低減します。また、加工速度や送り速度を事前のテストを通じて最適化することで、効率よく材料を削り取ることが可能になります。実際に、これらの対策を実施した工場では、加工時間が20%短縮されるなどの成果を報告しています。結論として、工具選定とパラメータの調整により、A5056の切削加工時間を効果的に短縮し、生産効率を高めることができるのです。
8. 切削工具の長寿命化とA5056切削加工への応用
A5056の切削加工時間を短縮することは、生産効率を大幅に向上させるために重要です。具体的な方法としては、切削工具の選定に着目し、より耐久性が高く効率の良い工具を使用することが挙げられます。例えば、ダイヤモンドコーティングされたエンドミルなどは、A5056のようなアルミニウム合金の加工において長寿命であり、工具交換の頻度を減らすことができます。このようにして工具寿命を延ばすことで、連続加工時間が長くなり、結果として加工時間の短縮とコスト削減につながります。最終的には、適切な工具を選定することにより、A5056切削加工の効率化を実現することが可能です。
9. 総括
A5056の切削加工時間を効率化することは、生産性の向上に直結します。理由としては、加工時間の短縮が材料コストの削減と機械の稼働率向上に寄与するためです。具体的な方法としては、新しい切削液の採用や最新の工具技術の導入が挙げられます。例えば、耐久性に優れた切削工具を使うことで、交換頻度が減少し、無駄な停止時間を削減できます。また、切削条件の最適化によっても、加工効率は格段に上がります。これらの施策を総合することで、A5056の切削加工時間の短縮が達成され、結果として生産効率が高まるのです。
まとめ
A5056の切削加工時間を短縮するためには、適切な切削条件や工具の選定が重要です。切削速度や送り速度、切削液の使い方などを最適化することで効率的な加工が可能です。また、最新の切削加工技術や工具を導入することも効果的です。現場の生産性向上に向けて、効率化を図るためには継続的な改善が不可欠です。
A5052の切削加工でコスト削減!タイムセービングのコツとは?
アルミニウム合金A5052の切削加工では、コスト削減とタイムセービングが重要な要素となります。この記事では、A5052の切削加工における効果的なコスト削減とタイムセービングの方法について解説します。A5052の特性や適切な加工方法について知り、効率的な生産プロセスを構築するためのヒントを提供します。
1. A5052 切削加工とは?
A5052の切削加工ではコスト削減を実現することが可能です。この成果の理由は、A5052合金が軽量で耐食性に優れ、加工性が良いためです。例えば、自動車や航空機の部品製造において、A5052の効率的な加工は材料費や加工時間の削減に直結します。精密な加工が求められる産業分野で、A5052を使うことにより、加工時の切削抵抗が少なく、工具の摩耗も軽減されるため、総合的なコストパフォーマンスが高まります。最終的には、A5052の切削加工はコスト効率を高めるだけでなく、製品の品質向上にも寄与し、企業の競争力を高める一助となるのです。
2. A5052 切削加工のコスト削減戦略
A5052の切削加工におけるコスト削減は、製造業の利益向上に直結します。この合金は、その優れた加工性と耐食性から、さまざまな産業で広く利用されています。コスト削減の鍵は効率的な工程管理にあります。例えば、切削工具の選定によって加工時間を大幅に短縮できます。また、切削条件の最適化は、工具の摩耗を減らし、交換頻度の低減にもつながります。具体的には、A5052の高速切削に適した工具を使用し、適切な速度と給送で加工を行うことが重要です。効率的な切削加工は、材料コストだけでなく、労働コストの削済にも効果的であり、結果として全体の生産コストを下げることができます。このように、適切な工具選定と条件設定によって、A5052の切削加工は、より経済的で効率的なものとなるのです。
3-1. 切削条件の最適化とは?
切削加工において、A5052のようなアルミニウム合金を扱う際は、コスト削減とタイムセービングを図ることができる最適化の手段があります。コスト削済の鍵となるのは、切削条件の選定に他なりません。具体的には、適切な切削速度、送り速度、切り込み量を選ぶことで、工具の摩耗を減らし、長寿命化を実現することが可能です。たとえば、A5052の場合は比較的柔らかい材質であるため、高速での加工が可能であり、これがタイムセービングに直結します。しかしながら、あまりにも高速すぎると工具の過度な摩耗や加工不良を引き起こすリスクがあります。したがって、材質や仕様に応じた適正な切削条件を見極めることが、効率的な加工フローを築く上で不可欠です。これにより、生産性を高めつつ、コストを抑制することが可能になり、結果として加工の品質向上にも寄与することになります。
3-2. 切削条件選定システムの活用
A5052の切削加工を行う際、コスト削減は重要なポイントです。コストを削減するためには、効率よく加工を行うことが必要です。具体的には、切削速度や送り速度、刃の交換タイミングの最適化を行い、無駄な時間を省くことがコツです。例えば、A5052は切削抵抗が低いため高速での加工が可能となります。しかし、適切でない条件で加工を行うと、刃の摩耗が早まり結果的にコスト増につながります。加工条件を事前にシミュレーションし、最適な条件を見極める切削条件選定システムの活用がコスト削減に繋がります。結論として、適切な切削条件の選定により、A5052の切削加工で効率を上げることがコスト削減への近道と言えます。
4. 工法転換によるA5052 切削加工の効率化
A5052の切削加工でコスト削減を実現するためには、効率的な工法への転換がカギとなります。A5052のようなアルミニウム合金は、その優れた加工性能により、多くの工業製品に使用されていますが、切削工程のコストが高まっているのも事実です。解決策の一つとして、高速かつ精密な切削を可能にする最新の工具の使用や、工程の自動化の促進が挙げられます。たとえば、マルチタスク加工機を導入することで、複数の工程を一つの機械でこなすことができ、作業時間の短縮と設備投資の削減につながります。また、切削条件の最適化により、工具寿命を延ばし、頻繁な交換コストを抑えることも可能です。このように工法を見直すことで、A5052の切削加工を効率化し、究極的にはコスト削減に繋がるのです。
5. 設備投資とA5052 切削加工コストの関係
A5052の切削加工においてコスト削減を実現するには、適切な設備投資が重要です。なぜならば、最新の切削機械を導入することで加工速度の向上と精度の向上が期待でき、結果的に時間当たりの生産性が向上するからです。具体的には、自動工具交換機能や高性能な切削液の使用が挙げられます。これらは、A5052のようなアルミ合金の加工時に発生しやすい熱や摩耗を最小限に抑え、切削工具の寿命を延ばし、連続稼働時間を増やすことができます。また、CAD/CAMソフトウェアによる事前の加工シミュレーションを行うことで、無駄な試作や加工ミスを減少させることが可能となります。これらの技術投資によって、A5052の切削加工でのコスト削減とタイムセービングが実現できるのです。
6. A5052 加工機の基本メリット
A5052の切削加工では、そのコストパフォーマンスの優秀さから、多くの企業がコスト削減に成功しています。特に、A5052は加工性が良好でありながら、耐腐食性にも優れているため、様々な産業で利用されているアルミニウム合金です。コストを削減するためのタイムセービングのコツとしては、適切な切削条件の選定や効率的な工具の使用が挙げられます。例えば、切削スピードやフィード率の最適化、チップの形状を選定することで、工具の摩耗を低減し寿命を延ばすことができます。また、CNCなどの最新技術を取り入れた機械を使用することにより、加工時間の短縮と精度の向上が図れるため、結果的にコスト削減に繋がります。最適な切削条件と効率的な工具を選択することで、A5052の加工コストを削減し、生産性の向上を実現することが可能です。
7. 工程短縮によるA5052 切削加工のコスト削減
A5052の切削加工におけるコスト削減は、工程の短縮を鍵としています。このアルミニウム合金は、その加工性の良さから多くの産業で利用されていますが、加工時間が長くなるほどコストも増大するため、工程の効率化が求められます。具体的には、適切な工具の選定や切削条件の最適化を行うことで、無駄な加工時間を削減できます。例えば、切削速度を上げることで一回の加工でより多くの素材を削り取ることが可能になり、結果として加工時間が短縮されます。また、耐久性の高い工具を使用することで、工具交換の頻度を減らし、連続加工が可能になることも一つの方法です。こうした技術的な工夫により、A5052の切削加工における生産性は向上し、コスト削減に繋がります。総じて、工程を見直し、最適化することで、A5052の切削加工のコストを削減できることが結論づけられます。
8. A5052 切削加工における環境影響評価
A5052の切削加工によってコスト削減を実現するには、工程を見直すことが鍵となります。なぜなら、A5052はアルミニウム合金であり加工性が良いため、切削条件を最適化することで加工時間を短縮し、結果的にコストを削減できるからです。例えば、切削速度や送り速度を上げる、適切な切削液を使用することで、加工効率が向上します。さらに、専用の切削工具を用いることで、一つの工具で複数の工程を行えるようにし、工具交換の時間も削減することができます。これらの工夫により、A5052の切削加工では、コストを抑えつつ品質を保持することが可能です。コストを低減しながら効率的な生産を目指すことで、企業の競争力を高めることができるでしょう。
9. 生産性向上への道:A5052 切削加工の研究動向
A5052の切削加工においてコスト削減を実現するためのタイムセービングのコツは、効率的な工程設計と適切な工具選択にあると結論づけられます。なぜならば、A5052はアルミニウム合金の一種で、耐食性や加工性に優れる一方で、切削工程でのコストパフォーマンスも求められます。具体的な例として、多刃エンドミルの使用や最適な切削速度の選定が挙げられます。多刃エンドミルを使うことで、一度に多くの切削が可能となり、工数を減らしつつ加工時間を短縮できるためです。また、材料と工具の組み合わせに応じた切削速度の適正化は、工具の摩耗を抑え、耐久性を高めることで長期的に見てコストを抑制します。したがって、A5052の切削加工でコスト効率を高めるためには、これらのポイントに注意を払うことが重要となります。
まとめ
A5052はアルミニウム合金の一種であり、その切削加工においては適切な工具選びと適正な切削条件が重要です。適切な切削速度や切削量を選定することで、コスト削減と作業時間の短縮が実現できます。また、切削液の使用や適切な刃先形状の選定も重要です。これらのコツを抑えることで、A5052の切削加工における効率的な生産が可能となります。
【工作機械必見】A5056の切削加工を成功させるポイント
工作機械業界におけるA5056の切削加工に興味はありますか?A5056は高い強度と耐食性を持ち、幅広い用途で使用されています。この記事では、A5056の切削加工を成功させるためのポイントについて詳しくご紹介します。切削加工に関する知識や技術に興味がある方、必見の内容となっています。
1. A5056切削加工の基礎知識
A5056の切削加工は技術者にとって重要な課題です。この素材の成功した加工には、特有の性質を理解し、適切な工具と条件を選択することが不可欠です。A5056は、優れた耐食性を持つアルミ合金でありながら、柔軟性と強度を両立しているため、航空機や自動車部品など幅広い用途に利用されています。そのため、切削時には、工具の摩耗を防ぐために低速で慎重に加工すること、切削液を適切に使用して熱と摩擦を最小限に抑えることが重要です。具体的な例としては、エンドミルの使用時には刃先の角度を適切に選定し、チップの形状にも注意を払う必要があります。これにより、A5056の特性に合わせた最適な切削が可能となります。このようなポイントを抑えることで、A5056の切削加工は成功に導かれるでしょう。
2. 工作機械の種類とA5056の加工適性
工作機械におけるA5056の切削加工の成功は、正しい知識と方法の理解に大きく依存します。まず、その軽量性と優れた耐食性から、A5056合金は航空機の部品や海洋関連設備に多用されています。これを加工する際のポイントは、適切な工具選びと切削条件の調整にあります。例えば、切削速度や送り速度を合金の特性に合わせて最適化することで、精度の高い加工が可能になります。また、冷却液の使用で切削時の熱を抑制し、工具の摩耗や製品の変形を防ぐべきです。最適な条件での加工は、長期にわたる工具の寿命を保ち、コスト削減と生産性の向上にも繋がるため、再度、適切な工具と条件設定の重要性が強調されます。
3. A5056切削加工における材料の特性
A5056の切削加工に成功するためには、その材料特性を理解することが不可欠です。A5056はアルミ合金の一種で、軽量でありながら高い強度を持つため、航空機の部品や自動車部品といった高い耐久性が求められる分野でよく使用されます。しかし、この材料は切削時に発生する熱により、工具の摩耗を早めることがあります。そのため、適切な切削速度と冷却方法を選択することが、加工精度を保ちつつ工具の寿命を延ばすために重要です。例えば、低速で丁寧に加工を行い、効率的な冷却液を使用することで、工具の摩耗を抑えつつ、精密な加工が可能になります。総じて、A5056の切削加工では、材料の特性を踏まえた加工条件の選定が成功の鍵を握ると言えます。
4. 切削仕上面の粗さを改善する方法
切削加工において、仕上面の粗さは製品品質を左右する重要な要素です。特にA5056のようなアルミ合金は、その加工性に注意が必要です。成功の鍵は、適切な切削条件の選択にあります。具体的には、刃の材質選びや切削速度、フィードレートを合金の特性に合わせて最適化することが重要です。例えば、A5056は比較的軟らかいため、高速な切削が可能ですが、切削速度が高すぎると熱がこもってしまうため、適度な速度の選択が求められます。さらに、高品質な工具を使用することで、切削時の振動を低減し、仕上面の粗さを向上することができます。最終的には、これらのポイントを踏まえた上で、慎重な加工計画と丁寧な作業が、A5056の切削加工を成功に導くでしょう。
5. A5056のエンドミル加工の切削条件
A5056の切削加工を成功させるためには、適切な切削条件の選定が重要です。A5056はアルミニウム合金であり、その特性上柔らかく粘りがあるため、切削時にはツールに対する負担が大きくなりがちです。具体的には、エンドミルを使用する際は、高い切削速度と適正な送り速度を設定することがポイントです。例えば、切削速度を高く設定し過ぎると工具の摩耗が激しくなり、低すぎると切削面にバリが発生しやすくなります。また、冷却液の使用も切削面の仕上がりを良くし、工具寿命を延ばすのに役立ちます。適切な切削条件を見極め、精度の高い加工を目指しましょう。最終的には、材料の特性を理解し、それに合った加工条件を選定することが、A5056の切削加工成功の鍵を握ります。
6. NC加工プログラムの基本とA5056加工
A5056の切削加工に成功するためにはいくつか重要なポイントがあります。まず、このアルミ合金はその優れた耐食性や加工性により、多くの工業分野で利用されていますが、その特性を理解することが不可欠です。具体的には、A5056合金は一般のアルミ合金に比べて柔らかいため、正しい工具選びと切削条件の設定が鍵となります。例えば、鋭い刃先を持つエンドミルを使用すると、素材への負担を減らし、精密な加工が可能になります。また、適切な切削速度や送り速度を見極めることも重要で、これによりバリの発生を抑えつつ、効率的な加工を実現できるでしょう。最終的に、これらのポイントに注意を払うことで、A5056の加工においても高品質な成果物を得ることが可能となります。
7. 機械学習を活用したA5056の切削面粗さ判別
A5056の切削加工に成功する重要なポイントは、適切な工具選択と切削条件の最適化です。このアルミ合金は加工性が良く、軽量かつ耐食性に優れているため、航空宇宙や自動車産業での需要が高まっています。適正な刃具を選び、切削速度や送り速度、切り込み深さを適切に設定することで、効率的かつ精密な加工が可能になります。実際に、高速で安定した加工を可能とする超硬エンドミルの使用や、切削油を使った冷却を行うことで、A5056の優れた切削面を得ることができます。これらのポイントを押さえることで、A5056の加工における品質と生産性を向上させることが期待できます。
まとめ
A5056の切削加工を成功させるポイントは、適切な切削速度と刃先形状を選定することです。A5056は耐食性に優れており、切削時に発生する熱をうまく制御する必要があります。また、適切な切削油を使用することで切削時の摩擦を減らし、切削表面の仕上がりを向上させることができます。さらに、適切な切削工具や工作機械の選定も成功の鍵となります。
【A5056の特性】切削加工のコツと注意点
金属加工において、A5056は非常に重要な素材です。その特性を理解し、効果的に切削加工を行うためには、慎重かつ正確なアプローチが求められます。この記事では、A5056の特性に焦点を当て、効果的な切削加工のコツや注意点について解説します。A5056を使用した加工作業を行う際には、この情報が役立つことでしょう。
1. A5056切削加工の概要
A5056は、優れた耐食性と加工性を持ち、多くの産業で利用されているアルミニウム合金です。切削加工を行う際には、材料の特性を理解することが成功の鍵です。例えば、A5056は加工硬化しやすい性質を持っているため、低い切削速度と大きな切削深さで加工することが推奨されます。また、専用の工具を使用し、定期的な冷却を行うことで、切りくずの排出をスムーズにし、工具の摩耗を防ぐことができます。切削油の選択も重要であり、A5056に適したものを使用することにより、切削効率を高め、表面品質を向上させることが可能です。これらのコツと注意点を踏まえ、A5056の加工には適切な方法が求められるのです。
2. A5056の物理的・化学的特性
A5056合金は、その優れた耐食性と加工性から、幅広い工業分野で切削加工が行われています。この合金を加工する際には、その特性を理解することが重要です。A5056は、アルミニウムとマグネシウムを主成分とする合金で、熱処理によって硬度を調整することができます。しかし、硬度が高い状態では切削加工時の工具の摩耗が激しくなるため、適度な硬さで加工することがコツです。また、A5056の優れた延性のおかげで、加工中に発生する熱が分散されやすく、切削時の熱影響を軽減できることも大きな利点です。しかし、切削速度や送り速度が適切ではないと、加工面に傷がついたり、精度が落ちる原因になります。このため、切削条件の選定には細心の注意を払う必要があります。要するに、A5056合金を効率よく、かつ高精度に加工するためには、合金の物理的・化学的特性を理解し、適切な切削条件の選定が欠かせません。
3. 切削加工におけるA5056の利点
A5056は、その優れた加工性により、切削加工分野で高い評価を受けています。この合金は特に、耐食性と加工性のバランスが求められる部品製造において、その真価を発揮します。例えば、精密な部品を必要とする航空機産業や自動車部品の製造において、A5056の均一な材質が加工時の安定性をもたらし、高品質な製品を効率良く生産することに貢献しています。しかし、この合金を加工する際には、工具の摩耗や切削速度の適正な調整が重要となります。適切な切削条件を見極めることが、A5056の持つ潜在能力を最大限に引き出し、無駄な材料の消耗を防ぐ鍵です。結論として、A5056の加工には特有のコツが必要であり、その特性を十分理解し、適切に対応することで、高品質な製品製造が可能となります。
4. 効果的なA5056切削加工の部品形状設計
A5056の切削加工において効果的な部品形状の設計は、加工の効率化とコスト削減に繋がります。A5056は良好な加工性を持つ一方で、材質特有の注意点を理解することが重要です。例えば、A5056はアルミニウム合金の中でも比較的柔らかいため、刃具の摩擦熱による軟化や、切削時の変形が起きやすいのです。これを避けるためには、あらかじめ切削抵抗が少なくなるように部品の形状を設計し、適切な切削速度と給送速度を選定する必要があります。また、切れ刃の鋭い工具を使用して、加工面の仕上がりを良くし、余分な負荷がかからないように注意することも肝心です。結論として、A5056の切削加工においては、材質の特性を踏まえた部品形状の設計と工具選定が、効率的な加工を実現するための鍵となります。
5. アルミニウムA5056の製造技術
アルミニウムA5056は、その優れた耐食性と加工性により、様々な工業製品の部材に用いられています。しかし、その特性を最大限に引き出すためには、適切な切削加工のテクニックが必要です。A5056のような非鉄金属の加工においては、刃物の摩耗を防ぎながら精度の高い加工を行うために、適正な切削速度の選定と冷却液の使用が重要です。例えば、A5056を加工する際には、一般的な鉄系材料よりも速い切削速度で切削し、加工熱の発生を抑えるために十分な冷却液を供給することが推奨されます。また、工具の鋭利さを保つことで、材料の粘着による工具の損傷を防ぎます。適切な切削条件のもとで加工を行うことは、品質の向上だけでなく、コストの削減にもつながります。従って、A5056の特性を理解し、切削加工におけるコツと注意点を押さえることが重要です。
6. A5056切削加工に適した旋削用チップの選定
A5056の素材はその優れた加工性により、多くの工業分野で使用されています。しかし、適切な切削加工を行うためにはいくつかのコツが必要です。まず、A5056は比較的軟らかい材質であるため、切削速度は高めに設定することが推奨されます。また、精度良く加工を行うためには、切れ味の鋭いチップを選択することが重要です。例えば、アルミニウム専用のポジチップや鏡面加工が可能な専用チップが効果的です。しかし、切削速度が高いため熱が発生しやすく、その熱によって工具の耐久性が低下することがあるため注意が必要です。適切な潤滑剤の使用によって、熱の影響を抑えつつスムーズな加工を実現することができます。総じて、A5056の切削加工は適切な工具選びと熱の管理が鍵となります。
7. フライス加工の基本とA5056
A5056合金のフライス加工は、その優れた機械的性質により幅広い産業で重宝されています。この合金を利用する際のコツとして、適切な切削速度の選定が挙げられます。A5056は耐食性と加工性に優れており、特に薄板加工や複雑な形状を持つ製品の加工に適しています。例えば、航空宇宙産業では、その軽量かつ強度が求められる部品の加工に使用されます。しかし、適切な工具選択や冷却液の使用が不適切だと、工具の摩耗や製品の精度低下を引き起こす可能性があるため注意が必要です。最適な加工条件を見極めることで、A5056の加工時の課題を克服し、高品質な製品を効率よく生産することができます。このため、材料の特性を理解し、加工条件を適切に管理することが非常に重要となります。
8. A5056切削加工の最適な切削速度
A5056合金は航空機や自動車の部品として広く使われているが、その加工には特別な注意が必要です。この合金の切削加工の最適な速度を見つけることが重要であり、適切な速度で加工することで精密な部品を製造できます。例えば、速すぎると材料が熱を持ちすぎてしまい、切削工具の摩耗が激しくなったり、仕上がりの品質が損なわれる可能性があります。逆に、遅すぎる速度では加工時間が余分にかかり、効率が落ちる原因となります。適切な切削速度を見つけることで、これらの問題を避け、品質の高い加工が可能になります。したがって、A5056合金を加工する際には、実際の作業条件に合わせた最適な切削速度の設定が切削加工の成功の鍵となります。
9. 低速切削時の溶着防止策
低速切削時にA5056のようなアルミニウム合金を扱う際には、溶着に注意しなければなりません。その理由として、アルミニウムは軟らかく、熱伝導率が高いため、切削中に発生する熱で工具と材料が容易に溶着してしまう性質があるのです。これを防ぐためには、以下の点を意識すると良いでしょう。まず、適切な切削液の使用が必須です。これにより熱の発生を抑え、工具の冷却を助けます。次に、適した切削速度と送り速度の選定も重要です。速すぎると工具の摩耗が進み、遅すぎると溶着のリスクが高まります。さらに、鋭利な工具を使用し、定期的なメンテナンスを行うことで、切削面の品質を保ちながら溶着を防げます。これらのコツと注意点を心がけることで、A5056の切削加工時における溶着を有効に防止することができます。
まとめ
A5056は耐食性に優れ、溶接性も良いアルミニウム合金です。切削加工を行う際には、十分な潤滑油を使用し、適切な切削速度と切削量を設定することが重要です。また、切削工具の選定にも注意が必要で、硬度が高いため硬質の切削工具を使用することが望ましいです。加工時には適切な冷却を行い、加工後は熱処理を施すことで強度を確保することができます。
切削加工業者必見!A5052の効率的な加工方法を徹底解説
切削加工業者の皆さん、A5052の効率的な加工方法について知りたいですか?この記事では、A5052の効率的な加工方法について徹底解説しています。もし新しい加工方法や最新の情報を知りたい方は、ぜひ読んでみてください。
1. A5052 切削加工の基礎知識
A5052の切削加工は、その優れた加工性と耐蝕性で多くの業界で用いられています。結論から言うと、A5052の効率的な加工方法には、適切な工具選択、切削条件の最適化、適切な潤滑が不可欠です。理由として、A5052は比較的柔らかいアルミニウム合金であるため、切削工具に負担をかけずに加工することができますが、不適切な条件下では材料が工具に張り付いたり、加工面の仕上がりが悪くなることがあります。例として、エンドミルを使用する際には、刃の数を多くすることで滑らかな切削が可能となり、加工面の品質が向上します。また、切削速度や送り速度を適切に設定することで、加工効率を高めることができます。潤滑剤を選ぶ際にも、A5052の材質に合ったものを選ぶことで、工具の摩耗を減らし長寿命化を図ることが可能です。したがって、これらの点に注意して加工を行うことで、A5052を効率良く加工することができるという結論に至ります。
2. エンドミルを使用したA5052の効率的な加工方法
A5052の切削加工において、エンドミルを使用することは非常に効率的です。A5052は軽量で耐食性に優れたアルミニウム合金であり、特に航空機の部品や産業機械の部材などに利用されます。その加工には、工具の選定が重要で、エンドミルは精度の高い加工が可能なため推奨されます。具体的には、良好な切りくず排出能力を持つ2枚刃や3枚刃のエンドミルを使用すると、切削抵抗が少なくなり、A5052のような非鉄金属の加工に適しています。加工速度と送り速度のバランスに注意し、適切な冷却液を使用することで、切削加工時の発熱を抑え、工具の寿命を延ばすことができます。エンドミルを正しく選定し、適切な加工条件を見極めることで、A5052の加工はより効率的かつ経済的になります。結論として、A5052の加工においてエンドミルの選択と使用法をマスターすることが、高品質な製品を効率的に生産する鍵となるでしょう。
3. 切削油剤の選択とA5052 切削加工への影響
A5052の切削加工において重要なのは、適切な切削油剤の選択です。切削油剤は加工精度や工具の耐久性に大きく影響を及ぼし、効率的な加工を実現するために欠かせません。具体的には、A5052との相性が良く、切削熱を効果的に除去し、かつ工具との摩擦を軽減する種類の油剤を使用することが推奨されます。実際に、適合する油剤を使用した場合、摩擦や熱による損耗が減り、工具寿命が延びるとともに、加工面の仕上がりも良くなることが報告されています。したがって、A5052切削加工においては、油剤選びに十分な注意を払い、加工効率と品質を保つべきです。
4. A5052 切削加工における切削条件の最適化
A5052の切削加工における効率化は、コスト削減と品質向上の両面において極めて重要です。このアルミニウム合金は、その優れた加工性と耐食性で知られており、さまざまな産業界で広く利用されています。効率的な加工を実現するためには、適切な切削条件の選定が不可欠です。例えば、切削速度はA5052の材質特性に合わせて調整する必要があり、速すぎると工具の摩耗が激しくなり、遅すぎると加工時間が増えてしまいます。また、切削液の使用は切削抵抗を低減させ、仕上がり面の品質向上に寄与します。さらに、工具の選定も重要で、A5052に適した刃の材質や形状を選ぶことで、長期的な工具の寿命を保ちながら精密な加工が可能になります。最適な切削条件下での加工は、無駄なトラブルを避け、コストパフォーマンスを高めることに繋がりますので、ぜひ参考にしてください。
5. 難削材A5052の品質工学的アプローチ
A5052の切削加工は、その優れた可成形性と耐食性により工業分野で広く利用されているものの、加工性には工夫が必要です。これはA5052が比較的軟らかく、切削時に工具に粘着しやすい特性を持つためです。しかしながら、適切な切削液の選択や工具の材質を工夫すれば、効率的かつ高品質な加工が可能となります。例えば、切削液には冷却性能が高く、粘着性を低下させるタイプを選ぶことが推奨されます。また、工具の材質には硬質コーティングがされた超硬合金が適しており、耐摩耗性の向上に寄与します。これらの対策を講じることで、A5052の加工性を向上させ、製品の品質を保ちつつ生産効率も高めることができます。
6. A5052 切削加工の生産性向上戦略
A5052の切削加工においては、生産性の向上が求められています。A5052はアルミニウム合金の一種であり、非鉄金属加工の現場ではその優れた加工性と腐食抵抗力から広く利用されています。しかし、加工時の効率化は常に業界の大きな課題です。具体的な方法としては、適切な切削工具の選定、切削条件の最適化、そして切削液の使用が挙げられます。例えば、高速度鋼よりも硬質合金を使った工具を選ぶことで、耐久性を保ちつつ加工速度を上げることが可能です。また、切削速度、送り速度、切り込み量を事前に計算し最適化することで、無駄な工具摩耗を減らし生産効率を高めます。切削液の使用は、工具の冷却や切りくずの排出を助け、品質の一貫性を保つためにも重要です。これらの方法を適切に組み合わせることで、A5052の効率的な加工が実現し、生産性の向上に繋がります。
7. 切削加工技術の進化とA5052の加工
A5052の切削加工は技術の進化と共に、より効率的かつ精密な方法が求められています。このアルミニウム合金は、その優れた耐食性や加工性のために広く利用されていますが、適正な工具選択と切削条件の最適化なしには、そのポテンシャルを最大限に引き出すことはできません。例えば、A5052を加工する際には、ダイヤモンドコーティングされたエンドミルを使用すると、耐久性が格段に向上し、長期にわたる精密加工が可能になります。また、適切な切削速度や送り速度を見極めることで、バリの発生を抑え精度の高い加工が実現します。このように、正しい工具と条件を選ぶことで、A5052の加工は効率的かつ高品質に行え、製品のコスト削減にも繋がります。最適な切削加工法を採用することで、A5052の可能性を最大限に活かしましょう。
8. A5052 切削加工のトラブルシューティングと対策
A5052合金は、軽量かつ加工性に優れるため、多くの切削加工業者にとって重宝されています。しかし、適切な加工方法を行わなければ、工具の摩耗や加工精度の低下を招く可能性があります。効率の良い加工には、刃物の選定、速度設定、冷却液の利用といったポイントが重要です。たとえば、アルミニウム合金専用の刃物を使用することで、加工面の滑らかさを保ちながら、摩擦を減少させることができます。加工速度に関しては、A5052の特性に合わせて適正な範囲を見極める必要があります。また、適切な冷却液を用いることで切削熱を効果的に逃がし、工具の寿命を延ばし品質を維持することが可能です。これらを総合することで、A5052の加工効率を大幅に向上させることができるでしょう。
9. A5052 切削加工に関するよくある質問
A5052の切削加工に取り組む際、効率性を重視することは極めて重要です。このアルミニウム合金は優れた加工性を持っており、適切な工具と加工条件を選定することで、加工コストを抑えつつ高品質の製品を提供できます。具体的には、シャープなエッジを持つ切削工具を使用し、低い切削抵抗と高い放熱性を利用します。また、適度な切削速度と給料で作業を行うことが重要であり、これによりバリの発生を抑制し、製品の仕上がり品質を高めることができます。繊細な操作が求められるA5052の加工においては、これらのポイントを押さえ、切削加工のルールを守ることで、効率的かつ精度の高い加工が実現します。
まとめ
A5052は耐食性・耐食性に優れ、加工性も良いアルミニウム合金です。切削加工の際は、適切な切削速度や切削深さを選定することが重要です。また、冷却剤の適切な使用や工具の適切な選択も加工効率を高めるポイントです。加工の際には適切な工具や切削条件を選定し、効率的な切削加工を心がけましょう。
A5056切削加工の基礎!素材の選定から表面仕上げまでの一連の流れ
金属加工においてA5056は非常に重要な素材の一つです。本記事では、A5056の切削加工に焦点を当て、素材の選定から表面仕上げまでの一連の流れについて解説します。A5056の特性や適切な切削条件、加工時の注意点など、基本から応用まで幅広くカバーしたコンテンツとなっています。金属加工に携わる方々や興味をお持ちの方々にとって、A5056切削加工に関する貴重な情報が満載です。
1. A5056切削加工入門
A5056切削加工は精密機器や部品製造に不可欠な工程であり、素材選定から表面仕上げまで正確な知識が求められます。まず、適切な素材選定が重要です。A5056のようなアルミ合金は、軽量でありながら強度が高く、加工性に優れているため、航空機の部品や自動車の部材によく使用されます。次に、切削加工の際には、工具の選択が品質に大きく影響します。適切な切削工具を使用することで、材料の無駄を減らし、効率的な加工が可能となります。具体例として、エンドミルやドリルなどの工具が挙げられます。これらはA5056のような材料を正確かつスムーズに加工するために特化しています。最後に表面仕上げでは、目的に応じた研磨やコーティングが行われ、製品の耐久性や見た目を向上します。結論として、A5056切削加工は、適切な素材の選定から正確な工具使用、丁寧な表面処理に至るまでの一連の流れを理解し遂行することで、高品質な製品を生産する礎となります。
2. A5056アルミニウム合金の選定基準
A5056アルミニウム合金の選定は、切削加工において重要な要素です。この合金が選ばれる理由は、その優れた加工性と耐蝕性にあります。特に、航空宇宙産業や自動車産業において、精密な部品を必要とする場合、A5056合金はその要求を満たす素材として適しています。具体的には、この合金は比較的低い硬度を持ちながら、高い強度を維持しているため、切削工具への負担が少なく、耐久性のある部品を生産することが可能です。表面仕上げにおいても、滑らかで均一な仕上がりが得られるため、最終製品の質を高めることができます。これらの特性から、A5056合金は切削加工における素材選定において、優れた選択肢の一つと言えるでしょう。
3. 切削条件の理解と設定
切削加工における適切な切削条件の理解と設定は、効率的かつ精度の高い加工を実現するために不可欠です。はじめに、A5056という材料は航空宇宙産業でも使用されるアルミニウム合金であり、その優れた加工性により広く利用されています。適切な切削条件を選定することで、材料の特性を最大限に活かし、製品の品質を確保することができます。例えば、切削速度や送り速度、刃の数などが適正に設定されれば、表面粗さを最適化し、耐久性や機能性を高める表面仕上げを得ることが可能です。このように、A5056材料を加工する際、適切な切削条件を見極め、それに基づいて精密な切削を行うことが、望ましい製品を製造する上で極めて重要であると言えます。
4. 6面フライスと4面フライスの違い
A5056切削加工は、精密な機械部品を生産する際に欠かせない工程です。この工程では、適切な素材選定がまず重要であり、強度や耐熱性など加工物の用途に最適な特性を有するA5056というアルミニウム合金の供給が重視されます。次に、精密な加工を実現するための切削工具の選択と切削条件の設定が行われ、A5056の高い加工性を生かし、寸法精度や形状を確保するための工程が進められます。例えば、航空宇宙分野の部品では、この合金の軽量性と高強度が利点として挙げられ、要求される精度を満たすため細部にわたる加工が施されます。最終的には表面仕上げによって製品の品質をさらに高め、摩擦係数の低減や耐食性の向上に寄与します。こうして、A5056切削加工は、最初の素材選定から最後の表面仕上げまで、一貫した流れの中でその品質が管理されるのです。
5. A5056切削加工手順
A5056切削加工における基礎知識は、製造業において非常に重要です。本文では、素材の選定から表面仕上げまでの流れを簡単に理解できるよう説明します。まず、A5056とはアルミニウム合金の一種であり、その加工性の高さから多くの産業で利用されています。素材の選定では、製品の用途や強度、耐久性を考慮し適したA5056を選びます。加工には、フライス加工や旋盤加工などの方法があり、図面に基づいた正確な寸法で素材を削り出します。次に、精密な加工を経て形状が出来上がると、バリ取りや研磨などの表面処理が行われ、製品は最終的な仕上げを施されます。この一連の流れを理解し、適切に適用することで、高品質なA5056加工品が得られるのです。
6. 銅電極加工用ロングネックスクエアエンドミルの概要
銅電極加工用のロングネックスクエアエンドミルは、精密な切削加工に欠かせない工具である。その最大の理由は、この特殊なエンドミルが持つ独自の形状と切削能力にある。銅という素材は優れた熱伝導率と加工性を持ちながらも、柔らかいため加工時には振動や変形が起きやすいという特徴を持っている。ロングネックスクエアエンドミルは、その長いネック部分によって、深い溝や細い壁の加工が可能となり、銅の電極加工において細部まで精密な仕上がりを実現する。加えて、四角い刃先は角の加工においても優れた性能を発揮し、どう角度効率よく材料を削り取ることができるのだ。エンドミルのこのような特性を最大限に活かすことで、複雑な形状の銅電極も高品質で効率的に仕上げることが可能になる。このため、銅電極加工用ロングネックスクエアエンドミルは、精密な電極を必要とする多くの産業にとって不可欠な工具となっている。
7. 切削液の選択と正しい使い方
切削加工における切削液の選択と正しい使い方は、作業効率の向上と工具の寿命延長に不可欠です。切削液には冷却と潤滑の役割があり、適切なものを選ぶことで加工物の品質が向上し、工具の摩耗を抑えることができます。例えば、一般的な鋼の加工には水溶性の切削液が使用されますが、アルミニウム合金の加工には、化学反応を引き起こすことがない特殊な切削液が推奨されます。また、切削液は定期的に交換することで、常に最適な性能を維持することが重要です。最後に、環境への影響を考慮して、使い終わった切削液は適切に処理することが求められます。こうした一連の流れを把握し実践することで、A5056切削加工の効率と品質が、さらに向上することでしょう。
8. 表面仕上げのテクニックとコツ
切削加工において、表面仕上げは製品品質を左右する非常に重要な工程です。そのため適切な素材選定から始め、精密な加工を行うことが不可欠です。例として、A5056というアルミニウム合金は、その優れた加工性と耐食性から航空機や自動車部品など幅広い用途に利用されています。加工時には、素材の状態を見極めることで工具の摩耗を抑え、効率良く仕上げを行うことができます。また、カッターの選定や切削速度、送り速度の調整も表面品質に影響を与えます。精度を求める場合、しばしば使用されるダイヤモンドカッターや高速度鋼など、適した工具を選択することが大切です。最終的な製品の精度を保証するため、適切な切削液の使用や細部にわたる注意深い検査が必須であり、この一連の流れを理解し適切に実施することで、高品質な表面仕上げを実現することができます。
9. A5056切削加工のトラブルシューティング
A5056切削加工では、適切な素材選定から始まり、精密な加工技術を経て、最終的な表面仕上げまでが重要です。なぜなら、これらの段階を正しく行わないと、製品の品質に大きく影響を及ぼすからです。例えば、素材としてA5056アルミニウム合金を選ぶ場合、その耐食性や加工性の良さを考慮に入れた上で、切削条件を最適化する必要があります。特に、工具の選択や切削速度、送り速度といったパラメータは、製品の寸法精度や表面品質に直結するため、慎重な調整が不可欠となります。最終的には、バリ取りや研磨などの表面仕上げ工程を施し、製品の品質を高めることが求められます。この一連の流れを正確に実行することで、A5056切削加工を成功させることができます。
10. A5056切削加工での安全対策
A5056切削加工は、その特性上高精度な加工が可能であり、自動車や航空機の部品製造において不可欠な技術です。適切に素材を選定し、加工を行うことで、製品の品質向上に大きく寄与します。まず、素材選定ではA5056の耐食性や強度が求められる局面での使用を考慮に入れ、適した切削工具を選ぶことが重要です。次に、精密な測定器を用いて寸法を厳密に管理し、切削条件を適切に設定することで、高品質な表面仕上げを実現します。具体例としては、航空機の翼や自動車のエンジン部品など、精度が求められる部品の加工にA5056が用いられています。最終的には、品質検査を行い、規定の基準を満たしていることを確認することで、製品の信頼性を保証します。以上の一連の流れを繰り返すことで、A5056切削加工の技術は一層洗練され、産業界におけるその価値を高めています。
まとめ
A5056は高強度アルミニウム合金であり、高性能の切削機械や適切な工具を使用すれば、精密な加工が可能です。素材の選定から表面仕上げまでの一連の流れを適切に実施することで、高品質な製品を生産することができます。
A5056アルミ合金を使いこなす!効率的な切削加工テクニック
A5056アルミ合金は非常に人気のある素材であり、効率的な切削加工テクニックをマスターすることは重要です。この記事では、A5056アルミ合金を使いこなすためのヒントやテクニックを紹介します。切削加工におけるA5056の特性や最新の技術について学び、効率的な切削加工プロセスを理解する手助けになるでしょう。
1. A5056 切削加工の基本
A5056合金はその優れた加工性と耐蝕性から、工業部品や構造材料に幅広く使用されています。この合金を効率的に加工するには、適切な切削技術の適用が必要です。例えば、低い切削速度ではA5056の長寿命化を図ることができ、また、適切な切削油の使用は摩擦を減少させてより滑らかな仕上げを実現します。さらに、定期的な工具の点検や交換を行うことで、精度の高い加工を維持することが可能です。加工工程を最適化することで、A5056合金はその特性を最大限に活かし、製品の品質を向上させることができます。したがって、これらの切削加工テクニックを身につけることは、A5056合金を扱う上で非常に重要です。
2. A5056 アルミ合金の特性と加工の理論
A5056アルミ合金はその優れた強度と耐食性から、多くの工業分野で欠かせない素材です。この合金を効率良く切削加工するには、適切な技術が必要です。具体的には、A5056の特性に合わせた切削速度、切削液の使用、そして専用の切削工具を選定することが重要です。たとえば、A5056は比較的柔らかいため、早い切削速度で加工すると材料が熱を持ちやすくなります。これを防ぐには、適度な速度での加工と適切な切削液の使用が効果的です。さらに、専用の切削工具を用いることで、アルミ合金特有の粘りによる刃先の損傷を防ぎ、加工精度を高めることが可能です。結果として、これらの技術を駆使すれば、A5056アルミ合金を効率的に、かつ高品質に加工することができるのです。
3. A5056 切削加工の条件設定
A5056アルミ合金は、その優れた加工性と耐食性のバランスから、多くの産業で使われています。特に、効率的な切削加工を行うことで製品の品質を左右し、生産コストを抑えることが可能です。A5056アルミ合金の加工には特有の技術が必要で、適切な条件設定が重要です。具体的には、刃の速度や送り速度、冷却液の使用量など、切削条件を最適化することがカギとなります。例えば、適切な切削速度を見極めることで、素材の熱変形を防ぎ、精度の高い加工を実現することができます。また、冷却液を適量使用することで、刃先の摩耗を抑え、より長いツール寿命を確保することもできます。このように最適な条件設定により、A5056アルミ合金はより効率的に加工され、高品質な製品へとつながるのです。
4. A5056 アルミ合金の工具材料選定
A5056アルミ合金の効率的な切削加工を実現するためには、適切な工具材料の選定が重要です。この合金は優れた耐蝕性と加工性を持っているものの、適切な工具を使用しなければ、工具の摩耗が早まる原因となります。特に、炭素鋼や高速度鋼よりも硬質の超硬合金やダイヤモンドコーティング工具を用いると、耐用年数を延ばしつつ精密な加工が可能になります。例えば、A5056アルミ合金を用いた航空機部品の製造においては、精度が求められるため、切削速度や送り速度の最適化とともに、これら高品質の工具を選定することが不可欠です。適正なツールを選ぶことで、加工精度の向上、生産性の向上、そしてコスト削減にも繋がります。したがって、A5056アルミ合金の加工にあたっては、材料の特性を理解し、最適な工具を選ぶことが重要であると結論付けられます。
5. コスト削減のためのA5056 切削加工戦略
A5056アルミ合金の切削加工は、高い効率と精度を要求される作業です。この合金は軽量でありながらも高い強度を持っているため、航空宇宙や自動車産業での需要が高まっています。そのため、A5056の効率的な加工技術をマスターすることが重要です。具体例としては、適切な切削油の使用や、適切な速度での切削が挙げられます。これらの要因を最適化することにより、工具の摩耗を減少させ、加工精度を向上させることが可能となります。結果として、製造コストの削済みと生産性の向上が期待できます。このため、A5056合金の切削加工における効率的なテクニックの習得は、製造コストの削減と製品品質の向上に直結するのです。
6. A5056 切削加工における工具の選定と使用条件
A5056アルミ合金の切削加工は、適切な工具の選定と使用条件によって、加工の効率が大きく変わります。この合金は軽量でありながら強度が高いため、航空機や自動車などの部品に多用されています。しかし、その特性から加工時には工具の摩耗が激しく、また、切りくずの排出も問題となり得ます。適切な工具を選び、切削速度や送り、冷却液の使用といった条件を最適化することが重要です。例えば、超硬チップを用いた工具は、耐摩耗性に優れA5056のような硬質材料の加工に適しています。また、高速切削に適した工具は、切りくずの排出を助け、加工精度を向上させます。最適な条件で加工を行うことで、A5056アルミ合金の加工性を高めることができ、製品の品質向上と生産効率の向上が期待できます。結局のところ、適切な工具選定と使用条件の最適化が、A5056アルミ合金の切削加工における鍵となります。
7. 難削材としてのA5056 アルミ合金の加工戦略
A5056アルミ合金は航空機や輸送設備などで求められる強度と軽量性を兼ね備えた素材であるため、切削加工においても高い精度と効率が要求されます。しかし、この合金はその硬さと粘り気のため、加工時に工具の摩耗が進みやすく、難削材とされています。適切な切削技術を用いることで、工具の消耗を抑えつつ、精密な加工が可能となります。例えば、高速度で安定した切削を実現するためには、適切な切削速度の選定と、冷却液を効果的に使用することが重要です。また、専用の切削工具を選ぶことで、A5056アルミ合金の特性に合わせた加工が実現し、製品の品質向上と生産性の向上が期待できます。これらのテクニックをマスターすることで、A5056アルミ合金の高効率な切削加工が可能になり、より多くの産業での利用が進むことでしょう。
まとめ
A5056アルミ合金の切削加工においては、適切な切削速度や刃物の選定が重要です。適切な冷却や潤滑も切削品質を向上させます。また、工具の選択や加工条件の最適化が重要です。特に高速切削や高送りの際には、工具の耐摩耗性や熱伝導性に注意が必要です。
高品質なA7075切削加工品を実現するためのトラブルシューティングガイド
こんにちは、A7075切削加工に関わるトラブルや課題に直面したことはありませんか?技術者や製造業の皆様にとって、A7075アルミニウム合金の切削加工は多くの挑戦が伴う作業です。そのため、本ガイドでは、高品質なA7075切削加工品を実現するためのトラブルシューティングに焦点を当て、解決策を提供します。
1. A7075切削加工の基本理解
A7075切削加工が高品質な製品を生むためには、トラブルシューティングが欠かせません。A7075は、航空宇宙産業などで使用される高強度アルミニウム合金で、その加工には特有の注意が必要です。例えば、切削速度や工具の選択に誤りがあると、仕上がりに欠陥が生じたり、工具の寿命に影響を与える可能性があります。さらに、適切な冷却液の使用は、加工中の発熱を抑え、製品の精度を保つのに役立ちます。実際の事例として、冷却液の流量や温度を調整することで、切削加工時の材料の応力を低減し、仕上がりの質を向上させた例が報告されています。このように、A7075の加工には適切な手順と知識が不可欠であり、トラブルを未然に防ぐことで、高品質な切削加工品の製造が可能となります。
2. A7075切削加工における一般的な問題点とその解決策
A7075の切削加工は、その高い強度と軽量性から、航空機や自動車部品などの精密な製品に広く利用されています。しかし、加工時には様々な問題が起こり得ます。これらの問題を解決することで、製品の品質を保ち、生産効率の向上を図ることができます。例えば、切削工具の選定が不適切だと、工具の摩耗が早まったり、製品の寸法精度が落ちる可能性があります。これを防ぐためには、A7075の材質特性に合った切削工具を選択し、適切な切削条件を設定することが重要です。また、加工時の振動や切りくずの排出不良も一般的な問題であり、これらは工具の切れ刃角度を調整することや切削液の使用によって改善されることが多いです。これらの具体的な対策を講じることで、A7075切削加工の品質を高めることができるのです。
3. A7075切削加工のための最新工具とシステム
A7075材の切削加工で高品質な製品を実現するためには、適切なトラブルシューティングが不可欠です。このアルミ合金は強度が高く、航空宇宙産業をはじめとする多くの分野で需要がありますが、加工時には固有の問題が生じやすいため注意が必要です。例えば、工具の摩耗が早く進行する、また加工面の粗さが理想的でないといった問題があります。これらの問題に対処するため、最新の切削工具の使用や、切削条件の最適化が重要となります。特に、工具の素材やコーティング、刃の形状を選定する際は、A7075材特有の性質を考慮に入れることが重要です。また、高度な切削システムを導入することで、工具の摩耗を抑制し、加工精度を高めることが可能になります。結論として、A7075の切削加工には専門的なアプローチが必要であり、適切な工具選定とシステム導入を行うことで、高品質な加工品を実現できるのです。
4. 長野県におけるA7075切削加工の特色と技術
高品質なA7075切削加工品を実現するためには、長野県が持つ特色と技術が重要です。長野県は、精密機械部品の製造において非常に高い技術力を有しており、これがA7075切削加工品の品質向上に貢献しています。具体的には、A7075という素材は非常に硬質であるため、通常の加工技術では対応が難しい場面も多々あります。しかし、長野県にはこれを可能にする高度な技術と経験豊かな技術者が存在し、精密な切削加工が可能となっています。また、特殊な工具を用いることで、耐久性や精度が要求される部品の加工も実現しています。このように、長野県で培われた技術と経験は、A7075切削加工品の高品質を支える基盤となっており、他地域にはない競争力を持っています。
5. A7075切削加工に関するトラブルシューティングの実例
A7075切削加工品の高品質を実現するためには、具体的なトラブルシューティングが欠かせません。A7075は航空機材などにも使われる高強度アルミニウム合金であり、その加工には特有の注意が必要です。例えば、切削速度の不適切な設定は、材料の焼き付きや工具の摩耗を引き起こし、加工精度の低下を招くことになります。また、クーラントの使用不足や不適切な使用は、切削熱の過剰な蓄積を招き、製品の品質に深刻な影響を及ぼすことがあります。実際に、適切な切削液の選定と供給方法を見直すことで、これらの問題は大幅に改善されます。このように、各種のトラブルに対する的確な診断と解決策の実施は、A7075切削加工品の品質を保つ上で不可欠です。最終的には、トラブルシューティングを通じて、品質の安定したA7075切削加工品を効率良く生産することが可能になります。
6. A7075切削加工の最新技術動向と未来のビジョン
A7075材を用いた切削加工は、その高い強度と軽量性から多くの工業分野で求められる技術です。しかし、加工時のトラブルは品質低下の一因となります。そのため、適切なトラブルシューティングが重要です。例えば、切りくずの排出不良や加工面の粗さは、適切な工具選択や切削条件の見直しにより改善されます。また、加工精度のバラツキは、機械のメンテナンス状態や工具の摩耗具合をチェックすることで、対策を講じることが可能です。これらの具体的な対策を実行することで、A7075の切削加工品質を高めることができます。最終的には、これらの対応策を踏まえた上で、品質の安定した加工品の提供が可能となり、顧客満足度の向上にも繋がるのです。
まとめ
A7075切削加工において品質を高めるためのポイントは、適切な切削速度と刃先の形状です。切削速度は高速であることが重要であり、刃先の形状は適切なものを使用することで、切削面の質を向上させることができます。また、適切な冷却や潤滑も重要であり、それらを管理することで高品質なA7075切削加工を実現することができます。
【品質向上】A2017切削加工におけるトラブル回避策と効率的なテクニック
A2017切削加工における問題を解決して効率的に生産性を向上させようとしている方々にとって、この記事は重要な情報源になります。A2017合金の切削加工に関するトラブル回避策や効率的なテクニックについて詳しく解説していきます。A2017合金を使用した切削加工における課題に直面している場合、この記事を参考にすることで問題の解決や生産性の向上につながるかもしれません。
1. A2017切削加工の基本と重要性
A2017切削加工は、製造業において重要なプロセスの一つです。その品質向上は生産効率と製品の信頼性を高める上で不可欠です。前提として、この加工においては正確な工具選定や適切な切削条件が必要ですが、トラブルを避け、効率化を実現するためのポイントを押さえることが求められます。たとえば、工具の摩耗を常にモニタリングすることで、不具合が発生する前に予防保全を行い、製品の精度を保持できます。また、最新のCNCプログラミングを駆使し、加工パスを最適化することで、工具の負担を減らし生産時間を短縮できる場合があります。このような工夫を行うことにより、A2017切削加工はより高品質で効率的なものとなり、製品価値を高めることができるのです。
2. A2017切削加工における切粉の影響と管理
A2017切削加工において品質向上を図るためには、切粉の影響とその管理が非常に重要です。A2017の加工時に生じる切粉は、機械の摩耗や製品の不良を引き起こす一因となります。この問題を避けるためには、適切な切削液の使用が効果的です。切削液は切粉を洗い流し、摩擦熱を減少させることで、切粉による悪影響を抑制します。また、切削工具の選定にも注意が必要です。例えば、A2017に最適化されたコーティングや形状を持つ工具を使用することで、切粉の発生を抑えることができます。定期的なメンテナンスの実施も重要であり、切削工具の摩耗をチェックし、タイミング良く交換することで、常に最良の切削状態を維持することができます。結論として、切粉の影響を最小限に抑えつつ、A2017切削加工の品質を向上させるには、切削液の適切な使用、工具選定、及び定期的なメンテナンスが不可欠です。
3. 工具の寿命とA2017切削加工の耐久性
A2017切削加工はその高い耐久性と効率性から、多くの工業分野で重宝されています。しかし、加工トラブルを避け、工具の寿命を延ばすためには、適切なテクニックと知識が不可欠です。例えば、工具の刃先の状態を常に監視し、摩耗が見られた場合には速やかに交換すること、適正な切削速度と送り速度の設定が挙げられます。これにより、工具の過度な負荷を防ぎ、精密かつ効率的な加工を実現できます。また、A2017材の特性に合わせた冷却液の使用も、加工品質の向上と工具の摩耗防止に繋がります。このように適切なメンテナンスと操作によって、A2017切削加工のトラブルを回避し、工具の寿命を延ばし、最終的には生産効率の向上が図れるのです。
4. A2017切削加工におけるリスクアセスメント手法
A2017切削加工における良好な成果を得るためには、トラブルを未然に防ぎ、効率的な加工技術を習得することが重要です。一つの大きな課題は、加工時の機械トラブルや材料の損傷ですが、これらは適切なリスクアセスメントを行うことで大幅に減少させることが可能です。例えば、事前の工具の点検や加工プロセスの見直しは、潜在的な問題を発見し、対策を講じる上で有効です。材料特有の挙動を理解し、それに適した切削条件を選定することも、品質の向上に不可欠です。実際に欠陥が少なく、スムーズな加工が実現できた事例も多数報告されています。こうしたアプローチにより、A2017切削加工はより安全かつ効率的に進めることができ、結果的に全体の生産性の向上に寄与します。
5. 切削工具の刃先の悪化原因とA2017切削加工での対策
A2017切削加工では、品質向上のためにトラブルを回避し、効率的な加工テクニックを身につけることが重要です。まず、切削工具の刃先が悪化する主な原因は、不適切な工具の使用や加工条件の誤りにあります。例えば、刃先の摩耗を防ぐためには、適切な切削スピードや送り速度を選択し、冷却剤を正しく使用する必要があります。また、A2017材に適した切削工具を選定することも、刃先の損傷を抑制し、加工精度を保持する上で大切です。切削工具自体の材質やコーティング、形状を最適化することも、品質を保つための要素の一つです。これらの点に注意を払い、継続的なメンテナンスを行うことで、A2017切削加工における品質向上が期待できます。結論として、適切な工具選定と加工条件の最適化により、加工トラブルを回避し、効率的なA2017切削加工を実現することができます。
6. ステンレス鋼のA2017切削加工とドリル切削の特徴
A2017切削加工において品質向上を図ることは、製造業者にとって非常に重要な課題です。A2017のようなアルミニウム合金は、その優れた加工性能により多くの工業製品で使用されていますが、加工時のトラブルを避けるためには適切な技術が必要です。例えば、適切な切削油の使用は、切削工具の摩耗を減らし、切削面の仕上がりを向上させることができます。また、切削速度や送り速度の最適化、冷却方法の改善も重要です。これらの技術を組み合わせることで、効率的に高品質なA2017切削加工を実現することができるのです。結局のところ、これらの適切な対策とテクニックを用いることで、製品の品質は格段に向上し、生産効率も高めることができるでしょう。
7. A2017切削加工現場でのトラブル回避策
A2017切削加工におけるトラブルは、品質の低下を招くため、効率的な回避策が不可欠です。この問題を解決するために、まずは適切な工具選択と切削条件の最適化が重要です。具体的には、A2017材に適した切削工具を使用し、切削速度や送り速度を材質に応じて調整することが挙げられます。これにより、刃の摩耗を減らし、精度の高い加工を実現できます。さらに、定期的な工具の点検や交換を行い、常に最良の状態で加工に臨むことも重要です。加工機の保守管理も欠かせません。予防保全により機械の突然の故障を防ぎ、常に安定した生産を維持することができます。結論として、これらの措置により、A2017切削加工のトラブルを大幅に回過し、生産性の向上に寄与することが期待されます。
8. A2017切削加工の最適化と効率的なテクニック
A2017切削加工はその精度と効率から多くの工業分野で重宝されています。しかし、その過程で起こるトラブルを避け、より高品質な製品を生産するには、適切な工夫とテクニックが必要です。例えば、刃の摩耗を抑制するために適正な冷却剤を使用すること、また切削条件を適切に設定することで、工具の耐久性を高めることができます。更に、工具の精度を定期的にチェックし、必要なメンテナンスを行うことで、加工精度の低下を防ぐことも重要です。これらの対策を講じることで、A2017切削加工のトラブルを減らし、効率的な製造プロセスを実現することが期待できます。結論として、適切な管理とテクニックの実施により、切削加工の品質向上と生産性の向上が見込めるのです。
まとめ
A2017切削加工において品質向上を図るためには適切な切削条件の設定や工具の選定が重要です。また、適切な冷却や潤滑を行うことで切削時の摩擦や熱の影響を抑え、トラブルを回避できます。加工精度を向上させるためには適切な切削速度や切削深さ、刃先形状などのテクニックに注意することが重要です。